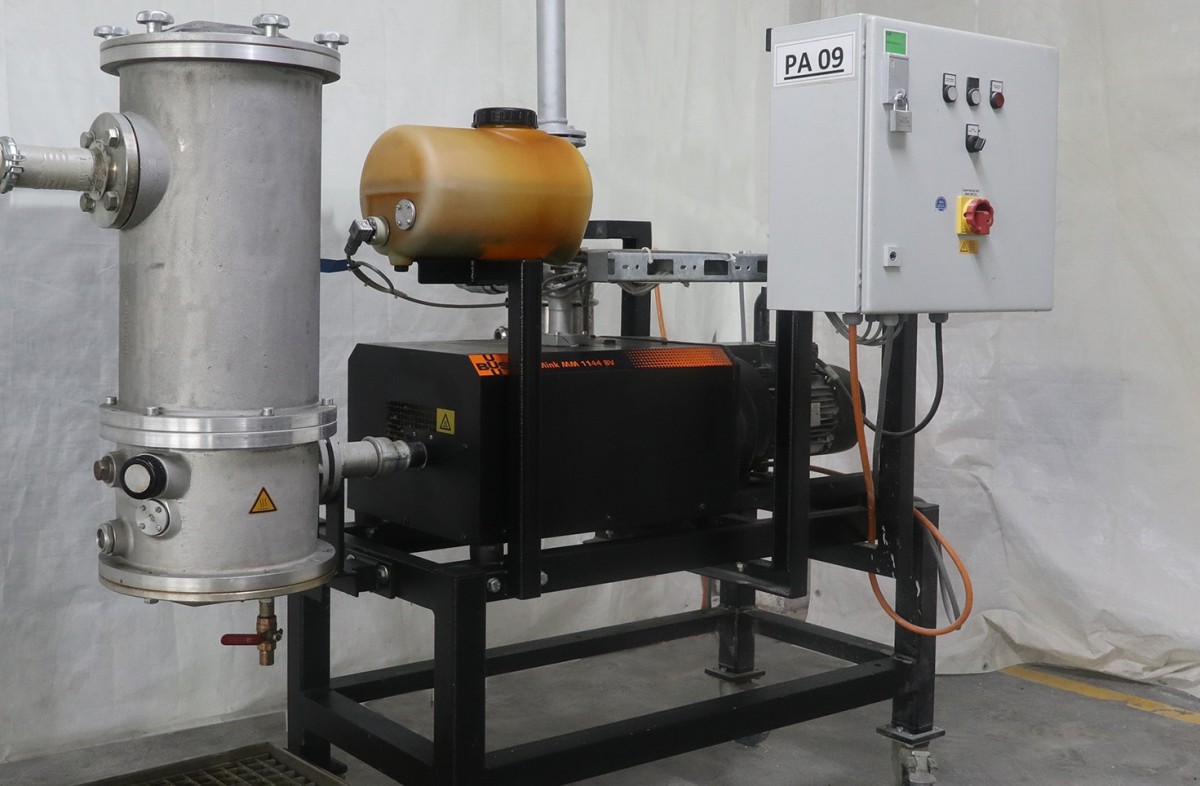
Technologie de vide moderne pour le dégazage de matériaux en fusion lors d'une extrusion
Cependant, il existe une constante pour toutes les extrudeuses : pour l'extraction des vapeurs et des gaz du matériau en fusion présent dans les sections à vis, PolyComp fait confiance uniquement aux systèmes de dégazage PLASTEX de Busch Solutions de Vide. Ces systèmes, équipés de pompes à vide à becs MINK, offrent une fiabilité exceptionnelle et une grande facilité d'entretien.
-
Fig. 1 : l'un des sept systèmes de dégazage PLASTEX chez PolyComp. Ils sont installés à l'étage au-dessus des extrudeuses.
À propos de PolyComp
Fondé en 2000, grâce à une opération de rachat par ses cadres, PolyComp et son siège social sont implantés à Norderstedt, en périphérie de Hambourg en Allemagne. En 2013, PolyComp a été intégré au groupe Feddersen, basé à Hambourg, dont le domaine d'activité est le commerce mondial de produits chimiques et techniques.Au cœur du métier de PolyComp se trouvent les composés à base de polyoléfine (PP/PE), ainsi que des produits tels que : EVA, PA, PBT, PC, ABS, EVOH, POM et PMMA. Ces compounds sont mélangés à différents additifs, tels que du carbone ou des fibres naturelles, des matériaux d'apport simples ou des perles de verre, des pigments ou des cires colorants.
Compounds sous forme de films
L'une des spécialités de PolyComp est le compound sous forme de film, qui nécessite des quantités extrêmement faibles de gel. Le processus de production comprend une étape d'extrusion qui nécessite des configurations de vis spécifiques et l'application d'un changeur de filtre avec une précision de filtration très élevée. L'entreprise utilise au total huit extrudeuses à vis unique ou à deux vis. Le matériau en fusion est dégazé dans six extrudeuses. Jusqu'en 2009, l'entreprise utilisait des pompes à vide à anneau liquide pour ce processus.La mise au rebut de l'eau utilisée devenait de plus en plus problématique car les gaz et les vapeurs se mélangeaient à l'eau et se condensaient. Le coût du traitement de l'eau ou de sa mise au rebut ne cessait d'augmenter.
Notre solution
En 2009, à la recherche d'une solution soucieuse de l'environnement, l'entreprise a pris contact avec Busch, qui lui a proposé un système de dégazage PLASTEX (Fig. 1) qui ne nécessitait aucun fluide de fonctionnement. Le système se compose essentiellement d'une pompe à vide à becs MINK (Fig. 2), d'un filtre séparateur en amont et d'un filtre fin. Les filtres sont utilisés pour séparer les condensats et les solides. Les pompes à vide à becs MINK ne nécessitent aucun fluide de fonctionnement, comme de l'huile ou de l'eau. Ceci signifie que les vapeurs et les gaz pompés n'entrent pas en contact avec un quelconque fluide de fonctionnement, avec lequel ils pourraient se mélanger ou réagir. Cependant, même la technologie de séparation la plus minutieuse ne peut pas toujours empêcher les monomères résiduels de pénétrer à l'intérieur des pompes et d'y subir un craquage. Pour cette raison, la pompe à vide à becs MINK est équipée d'un dispositif de rinçage. Ceci permet à une quantité de liquide de rinçage précisément dosée d'être injectée dans la pompe à vide, selon des intervalles de temps définis, pour dissoudre les produits de craquage. Le responsable de la maintenance, Stefan Stolp, a défini la quantité de liquide de rinçage et les intervalles de rinçage pour chacun des matériaux extrudés. Le processus de rinçage peut se dérouler pendant les temps d'arrêt ou même lorsque la production est en cours.-
Fig. 2 : pompes à vide à becs MINK au cœur des systèmes de dégazage PLASTEX. Grâce à leur principe de fonctionnement sans contact, elles ne nécessitent aucun fluide de fonctionnement, comme de l'huile ou de l'eau.
L'ingénieure Simone Patermann a identifié un autre avantage de l'utilisation des systèmes de dégazage PLASTEX. En tant que responsable de la production, elle a toujours un œil sur la consommation d'électricité, du fait que PolyComp est certifié ISO 50001, la norme relative aux systèmes de management de l’énergie.
En 2018, PolyComp a lancé une nouvelle ligne d'extrusion, dont le cœur est une extrudeuse à deux vis et dont le débit de sortie peut atteindre 1 500 kilogrammes par heure. Les deux dispositifs de distribution latérale (Fig. 3) permettent l'ajout simultané de différents types de matériaux d'apport en poudre et leur mélange, le tout avec une capacité de production élevée. Un dispositif de distribution latérale peut être raccordé à un système de dégazage PLASTEX. Ceci permet de réduire le volume des matériaux d'apport et de tripler la masse volumique par rapport à un dispositif de distribution latérale sans dégazage. Ceci augmente de manière significative le débit de sortie total.
-
Fig. 3 : les deux dispositifs de distribution latérale montés sur l'extrudeuse à deux vis. Un système de dégazage PLASTEX permet de réduire le volume lors de l'ajout d'un matériau d'apport. Source : PolyComp