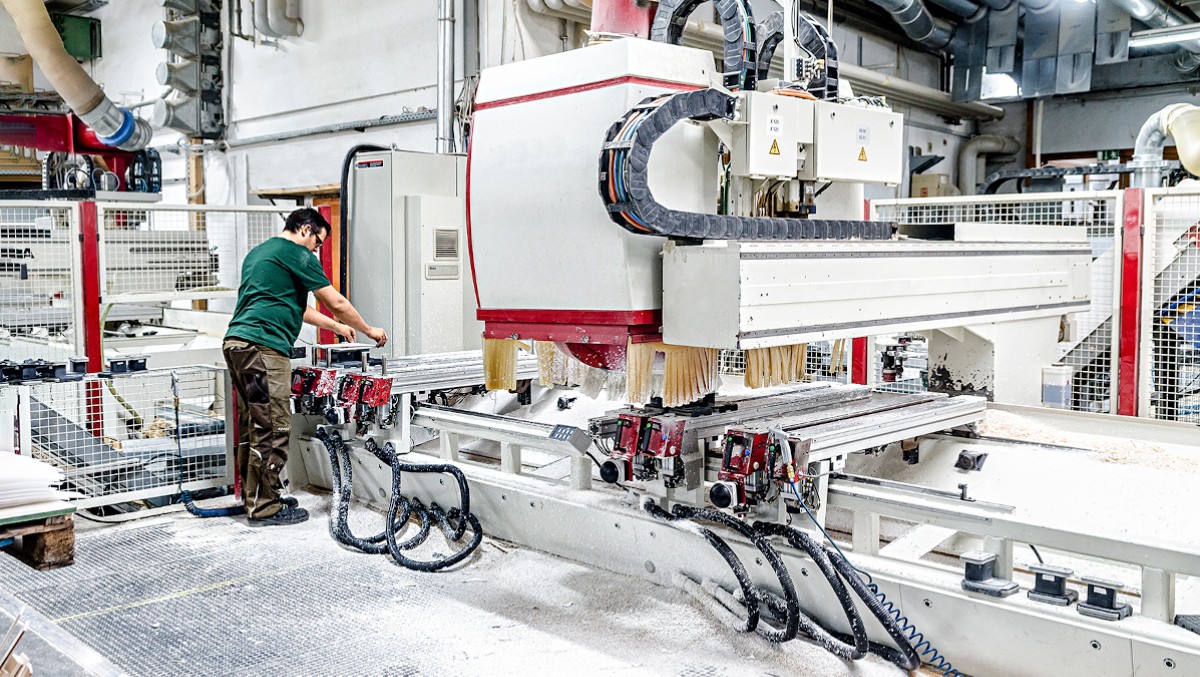
Source: Busch Vacuum Solutions
Vacuum Pumps in CNC Routers: Repair or Replace?
A Comprehensive Guide
If the vacuum pump in your CNC router is malfunctioning, you are faced with a choice: repair or replacement. Our guide will take you through both options and provide recommendations on when it makes sense to repair vacuum pumps and when to replace them. We will also look at how to spot and diagnose common issues before they lead to system failure.
-
Source: Busch Vacuum Solutions.
The starting point:
diagnosis and decision-making
Regardless of the chosen course of action, the initial step in deciding whether to repair or replace your vacuum pump always involves testing and diagnosis. A factory-trained service technician who specializes in vacuum pump services carefully inspects the equipment to identify the underlying problem. The technician will, for example, use specialized equipment to measure the vacuum pump’s pressure and flow rates and inspect key components such as the motor, bearings, valves and seals for signs of wear or damage.
Repair
If your vacuum pump can be repaired, faulty components are removed and replaced and the equipment is returned to manufacturer specifications.
Pros
Cons
- Cost effective: If the issue is minor, or the vacuum pump is relatively new, there may only be a few spare parts to replace.
- Low environmental impact: Fewer resources are used and less waste is produced.
- Potential for higher costs in the long term: If the vacuum pump’s issues are difficult to repair, they may reappear.
- Fixes only one specific problem: Vacuum pump repair doesn’t guarantee that new problems won’t arise in the future.
Replacement
If you opt to replace your vacuum pump, the existing one will be removed and a brand new pump will be installed.
Pros
Cons
- Higher reliability: New vacuum pumps have entirely new components and may be more energy efficient.
- New warranty: A new unit comes with a new warranty, offering peace of mind and potentially reducing future repair costs.
- Higher upfront costs: Purchasing a new vacuum pump means higher initial costs.
- Longer installation time: Installing and integrating a new vacuum pump may require more time than minor repairs.
-
Source: Busch Vacuum Solutions
Key considerations
Before deciding whether to repair or replace your vacuum pump, it’s important to consider five key criteria.
1) Costs
If your existing vacuum pump has only a minor issue, a repair may be the more economical option. However, you should also consider longer-term maintenance and repair costs. As a vacuum pump gets older, for example, it may require more frequent servicing. This could add up to more than the price of a replacement over time, even though this will require a much larger immediate outlay.
Example:
For a CNC routing machine experiencing vacuum pump failure, review the pump’s maintenance history and failure reports. Assess the labor and parts expenditure for the equipment in the past six to twelve months and consult with operators regarding its performance.
If the vacuum pump has had multiple failures within the last year, along with various minor issues and complaints from staff, this may indicate that the asset is approaching the end of its useful life.
Calculate the repair costs:
Let’s assume the parts for the vacuum pump repair would cost 3,000 US Dollars: labor another 1,000 US Dollars, and operation downtime would cost another 1,000 US Dollars. That totals 5,000 US Dollars for a complete repair.
If we know that the vacuum pump has failed four times in the last two years since it began having problems (or two times per year on average), we can assume that maintaining this pump will cost a minimum of 10,000 US Dollars per year.
You may also want to consider the long-term maintenance costs of one type of vacuum pump over another. If your vacuum pump is a vane-type design that experiences premature vane wear, it is possible to save costs by switching to a different type of vacuum technology. For example, do you have to change the vanes, filters, and oil often? Consider a dry claw vacuum pump that does not have vanes, oil filters or process oil that requires regular maintenance.
If your existing vacuum pump has only a minor issue, a repair may be the more economical option. However, you should also consider longer-term maintenance and repair costs. As a vacuum pump gets older, for example, it may require more frequent servicing. This could add up to more than the price of a replacement over time, even though this will require a much larger immediate outlay.
Example:
For a CNC routing machine experiencing vacuum pump failure, review the pump’s maintenance history and failure reports. Assess the labor and parts expenditure for the equipment in the past six to twelve months and consult with operators regarding its performance.
If the vacuum pump has had multiple failures within the last year, along with various minor issues and complaints from staff, this may indicate that the asset is approaching the end of its useful life.
Calculate the repair costs:
Let’s assume the parts for the vacuum pump repair would cost 3,000 US Dollars: labor another 1,000 US Dollars, and operation downtime would cost another 1,000 US Dollars. That totals 5,000 US Dollars for a complete repair.
If we know that the vacuum pump has failed four times in the last two years since it began having problems (or two times per year on average), we can assume that maintaining this pump will cost a minimum of 10,000 US Dollars per year.
You may also want to consider the long-term maintenance costs of one type of vacuum pump over another. If your vacuum pump is a vane-type design that experiences premature vane wear, it is possible to save costs by switching to a different type of vacuum technology. For example, do you have to change the vanes, filters, and oil often? Consider a dry claw vacuum pump that does not have vanes, oil filters or process oil that requires regular maintenance.
2) Process requirements
Evaluate whether your existing vacuum pump is still the best option for your process. If your vacuum pump is always running flat-out, or reserve pumps are regularly coming online to meet demand, the process may have outgrown the pump’s current capabilities. Replacement could therefore be a sensible option. This will help avoid production delays and ensure you maintain optimal quality and performance.
Evaluate whether your existing vacuum pump is still the best option for your process. If your vacuum pump is always running flat-out, or reserve pumps are regularly coming online to meet demand, the process may have outgrown the pump’s current capabilities. Replacement could therefore be a sensible option. This will help avoid production delays and ensure you maintain optimal quality and performance.
3) Service history
Has this same problem occurred before? Examine the service history to be sure. Regular maintenance actions like replacing spare parts such as seals, gaskets, or vanes are usually part of regular maintenance, but if larger issues keep cropping up, repairs may no longer be an option.
Has this same problem occurred before? Examine the service history to be sure. Regular maintenance actions like replacing spare parts such as seals, gaskets, or vanes are usually part of regular maintenance, but if larger issues keep cropping up, repairs may no longer be an option.
4) Energy efficiency
Many new generations of vacuum pumps are more energy-efficient than the one before. For example, dry claw vacuum pumps are friction-free and have highly efficient motors. You should therefore consider the benefit of replacing your current vacuum pump with one that consumes less energy. Depending on the difference in consumption between your current vacuum pump and the newest technology, your energy bills could sink considerably. And your carbon footprint too.
Many new generations of vacuum pumps are more energy-efficient than the one before. For example, dry claw vacuum pumps are friction-free and have highly efficient motors. You should therefore consider the benefit of replacing your current vacuum pump with one that consumes less energy. Depending on the difference in consumption between your current vacuum pump and the newest technology, your energy bills could sink considerably. And your carbon footprint too.
5) Technical features
Consider the state-of-the-art technology in your current vacuum pump. Do more modern vacuum pumps come with new technical features that could benefit your CNC routing process? If so, now might be the right time to invest. Some features can be added to an existing vacuum pump – an ECOTORQUE variable speed drive or OO digital services for intelligent monitoring of your vacuum pump.
However, if your pump is getting older, it may not be compatible with these newer features that have become available since its purchase. This could mean missing out on optimization opportunities for your process. Therefore, you should consider how important these options are to you and your process. This could sway your decision between repairing or replacing your vacuum pump.
Consider the state-of-the-art technology in your current vacuum pump. Do more modern vacuum pumps come with new technical features that could benefit your CNC routing process? If so, now might be the right time to invest. Some features can be added to an existing vacuum pump – an ECOTORQUE variable speed drive or OO digital services for intelligent monitoring of your vacuum pump.
However, if your pump is getting older, it may not be compatible with these newer features that have become available since its purchase. This could mean missing out on optimization opportunities for your process. Therefore, you should consider how important these options are to you and your process. This could sway your decision between repairing or replacing your vacuum pump.
-
Source: Busch Vacuum Solutions.
Identifying and troubleshooting common vacuum pump issues
Vacuum pumps rarely fail without warning. However, it can be hard to catch the early symptoms of a problem. Regular maintenance is the first step: A problem spotted early is generally easier to repair.
It is also helpful to familiarize yourself with common issues and the telltale signs of a failing vacuum pump:
It is also helpful to familiarize yourself with common issues and the telltale signs of a failing vacuum pump:
- Decreased performance: If your vacuum pump struggles to maintain the necessary vacuum level or if the CNC machine is not holding materials in place as effectively as it should, it could indicate an issue with the vacuum pump.
- Unusual noises: Grinding, squealing, or banging could indicate mechanical problems within the vacuum pump.
- Increased energy consumption: A failing vacuum pump may require more energy to operate, leading to higher energy bills.
- Leaks: Any leaks, whether oil or air, could indicate a problem with the pump’s seals or valves.
- Excessive heat: If the vacuum pump is unusually hot to the touch, it could indicate that it is working harder than usual, which may be a sign of impending failure.
- Frequent cycling: If the pump, equipped with a VSD,turns on and off more frequently than usual, it could indicate pressure or flow issues, which could lead to pump failure.[
- Error messages or alarms: Modern CNC machines, or the vacuum pump itself, often have monitoring systems that detect vacuum pump issues and trigger error messages or alarms.
If you notice any of these signs, it’s important to address them promptly to avoid costly downtime and potential damage to your CNC router. Don’t hesitate to ask for assistance from professional vacuum pump service providers and specialist factory-trained service technicians to diagnose and troubleshoot these issues. It is also worth considering investing in an intelligent monitoring system, such as OO digital services. Sensors will continuously monitor each vacuum pump’s performance data and flag any anomalies.
Some relevant vacuum pump performance indicators include:
Some relevant vacuum pump performance indicators include:
- Oil tempertature
- Exhaust pressure
- Energy consumption
- Vibration level
- Exhaust backpressure
- Oil level
- Exhaust temperature
-
Source: Kvist Industries
Success Story: Economical and reliable vacuum clamping for furniture production
Kvist Industries, a Danish furniture manufacturer, uses vacuum for clamping and nesting on CNC routers. Vacuum clamps securely fasten wooden workpieces and prevent movement during the cutting process and ensure precise cuts. A strong and reliable vacuum supply is essential to achieve the desired results when creating high-quality wooden furniture.
However, the dry-running rotary vane vacuum pump in one CNC router began exhibiting signs of increased noise and decreased holding power, resulting in production delays. During a thorough examination, the technician from Busch Vacuum Solutions noted several factors regarding the vacuum pump. Not only was it less energy-efficient compared to other types of vacuum technology, but the current repair costs, along with ongoing maintenance expenses, also raised concerns. Consequently, he proposed replacing it with a dry claw vacuum pump from Busch.
The advantages of the dry claw vacuum pump (Fig. 1) became apparent upon closer inspection. Thanks to its contact-free claw technology, its energy efficiency surpassed that of similar-sized vacuum pumps. Unlike dry-running rotary vane vacuum pumps, where pumping speed and vacuum level diminish over time due to vane wear, the dry claw vacuum pump maintains consistent performance throughout its lifespan. Moreover, its compact design often allows a smaller claw vacuum pump to outperform larger dry-running rotary vane vacuum pumps, resulting in reduced motor requirements for a comparable pumping speed. The absence of vanes eliminates the need for frequent replacements or maintenance, further streamlining operational costs.
Kvist Industries, a Danish furniture manufacturer, uses vacuum for clamping and nesting on CNC routers. Vacuum clamps securely fasten wooden workpieces and prevent movement during the cutting process and ensure precise cuts. A strong and reliable vacuum supply is essential to achieve the desired results when creating high-quality wooden furniture.
However, the dry-running rotary vane vacuum pump in one CNC router began exhibiting signs of increased noise and decreased holding power, resulting in production delays. During a thorough examination, the technician from Busch Vacuum Solutions noted several factors regarding the vacuum pump. Not only was it less energy-efficient compared to other types of vacuum technology, but the current repair costs, along with ongoing maintenance expenses, also raised concerns. Consequently, he proposed replacing it with a dry claw vacuum pump from Busch.
The advantages of the dry claw vacuum pump (Fig. 1) became apparent upon closer inspection. Thanks to its contact-free claw technology, its energy efficiency surpassed that of similar-sized vacuum pumps. Unlike dry-running rotary vane vacuum pumps, where pumping speed and vacuum level diminish over time due to vane wear, the dry claw vacuum pump maintains consistent performance throughout its lifespan. Moreover, its compact design often allows a smaller claw vacuum pump to outperform larger dry-running rotary vane vacuum pumps, resulting in reduced motor requirements for a comparable pumping speed. The absence of vanes eliminates the need for frequent replacements or maintenance, further streamlining operational costs.
-
Figure 1: MINK dry claw vacuum pump. Source: Busch Vacuum Solutions
After evaluating the total cost of ownership for both vacuum pumps, Kvist Industries decided that investing in a new dry claw vacuum pump from Busch was the best and most cost-effective choice for long-term efficiency.
Conclusion
When your vacuum pump isn’t running as it should be, carefully weigh your options. Consult the experts from a vacuum pump repair service provider and have them conduct a proper inspection and diagnosis. You should also assess efficiency, performance, and the cost of repairs – both now and in the future – versus the cost of a new vacuum pump. This will help you determine the best course of action. Ultimately, your decision should be based on what is most cost-effective and beneficial for your production process.
These criteria can be tricky to assess by yourself, so Busch will be happy to assist. Our specialists will visit you on-site, evaluate your current equipment and give you a recommendation on how to move forward. Whatever you decide, we will be there to carry out any necessary repairs or provide you with a suitable replacement.
For even more peace of mind, let Busch take care of your maintenance with service contracts, and intelligent IoT solutions. With 60 years of experience in the world of vacuum, you can be sure your vacuum supply is in good hands.
Contact us to discuss the details and restore your vacuum equipment to its optimum performance.
These criteria can be tricky to assess by yourself, so Busch will be happy to assist. Our specialists will visit you on-site, evaluate your current equipment and give you a recommendation on how to move forward. Whatever you decide, we will be there to carry out any necessary repairs or provide you with a suitable replacement.
For even more peace of mind, let Busch take care of your maintenance with service contracts, and intelligent IoT solutions. With 60 years of experience in the world of vacuum, you can be sure your vacuum supply is in good hands.
Contact us to discuss the details and restore your vacuum equipment to its optimum performance.