In mechanical engineering, cleaning machined components has become an indispensable step in the part manufacturing process. Various cleaning methods are used, depending on the degree of soiling and the geometry of the parts. The choice of cleaning method has no bearing on the subsequent drying process.
In addition to convection drying, which uses the intrinsic heat of the parts heated up by the cleaning process, or circulating air drying using hot air, vacuum drying is an efficient and rapid method for drying parts.
In this article, we would like to take a look at vacuum drying and the vacuum pumps used for this purpose.
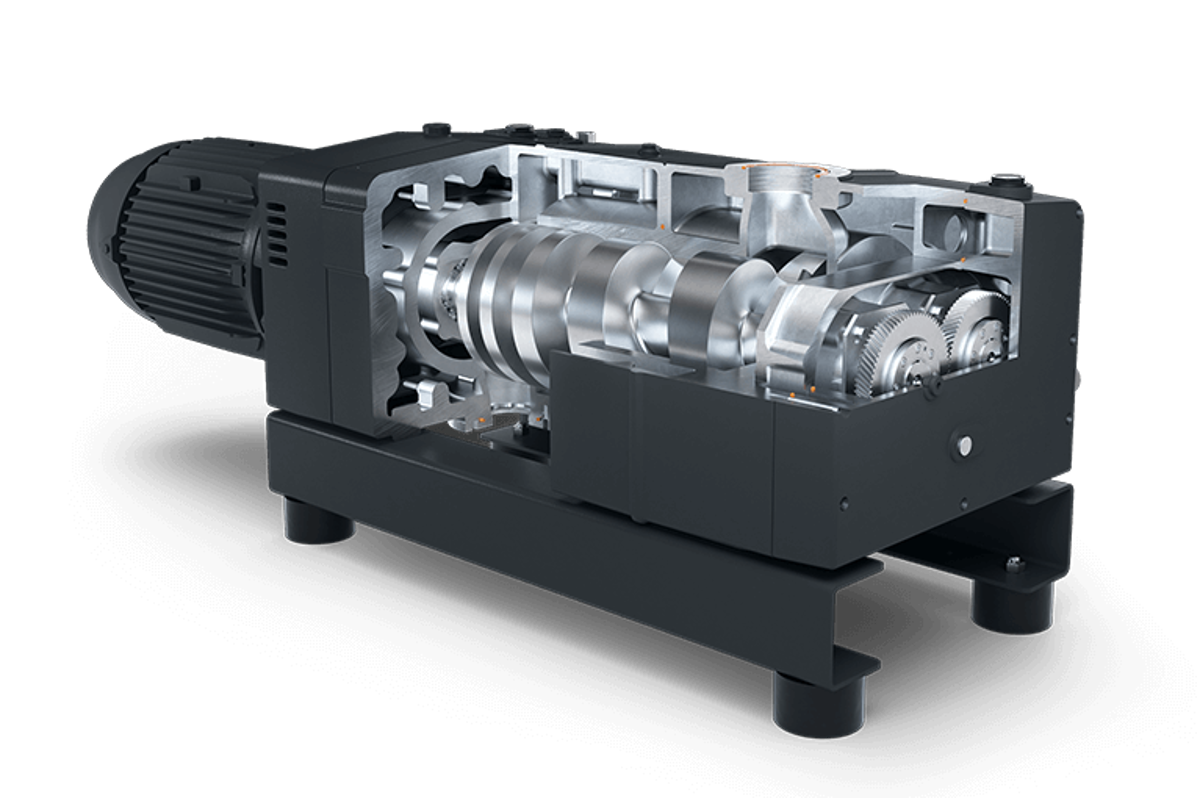
Source: Busch Vacuum Solutions.
Vacuum for Cleaning and Drying Industrial Parts
Cleaning methods
Components are usually cleaned following machining or reshaping work, or following heat treatment.Cleaning methods can basically be divided into two categories: cleaning with aqueous solutions and cleaning with solvents. There are also a number of special processes.
The final choice of method depends on various factors. The most suitable cleaning method must be selected depending on:
- the material of the components
- the type of soiling
(different types of oil, grease, emulsion, dust etc.) - or the geometry of the components
(surface structure, holes, undercuts etc.).
Consideration must also be given to the level of purity required of the components.
Drying methods
The subsequent drying of the cleaned components is an absolute must. In the case of aqueous media, even minimum residual moisture can cause corrosion damage to the finished product, which can lead to high follow-up costs. Inadequately dried solvents can result in decomposition products on the work piece.Convection drying
Convection drying is the simplest drying method. The components, which are heated to a temperature of between 70 and 80°C during the cleaning process, cause the adherent moisture to evaporate.
Circulating air drying
With circulating air drying, a flow of hot air is directed over the components, resulting in evaporation of the moisture.
Both of these methods are suitable for use with geometrically simple components.
Vacuum drying
Vacuum drying is extremely reliable and efficient. It even guarantees the rapid drying of parts that are geometrically complex and can be used for both cleaning methods involving aqueous solutions and solvent cleaning.
The active principle of vacuum drying
Vacuum drying makes use of the physical property whereby the boiling temperature of liquids drops under vacuum, meaning that liquids evaporate even at low temperatures. With vacuum drying, liquid that is still present after the cleaning process, e.g. in pocket holes, and that proves difficult to remove with other methods, evaporates just as quickly as the residual liquid on the other surfaces of the component.Functional description of a cleaning system with aqueous solutions
Once the working chamber has been loaded with the parts to be cleaned and then sealed, it is then evacuated by means of the vacuum pump to a pressure of around 100 millibars.The cleaning medium is then pumped into the working chamber by means of a flood pump. The vacuum in the chamber ensures that the cleaning solution penetrates into the smallest of cavities and that, for example, pocket holes are not omitted due to the trapping of air.
The subsequent cleaning process can vary greatly. It generally involves a combination of immersion and spray cleaning, sometimes supported by ultrasonic cleaning. This is generally followed by one or more rinsing cycles.
Once the cleaning solution has been pumped away, the actual vacuum drying process takes place. For this process, the chamber pressure is lowered further by the vacuum pump. The vapours produced by this are sucked out by the vacuum pump and transferred to an air evacuation duct.
Functional description of a cleaning system with solvents
In principle, the cleaning process with solvents is similar to the cleaning process with aqueous solutions. However, the vacuum pump is generally required to perform additional tasks.Firstly, it is important to comply with explosion protection requirements and two different approaches are possible here.
Either a vacuum pump with an ATEX-compliant design can be used, or the cleaning system can be operated at a permanent system pressure of less than 100 mbar, which means that explosion protection is not required. This system pressure can be generated by the same vacuum pump, although a second, smaller vacuum pump is sometimes used for this purpose.
Secondly, the solvents evaporated during the drying process are recovered using a vacuum distiller in which the solvent is distilled back out of the contaminated medium. The solvent distillate is returned to the cleaning process via the reservoirs, while the oil/soiling concentrate is collected in barrels.
Vacuum generators used
Oil-lubricated rotary vane vacuum pumpsOil-lubricated rotary vane vacuum pumps are frequently used in cleaning systems.
Experience has shown that this type of vacuum pump is ideally suited to this application and it has therefore become the standard pump for the drying process in cleaning systems.
Rotary vane vacuum pumps are robust vacuum generators with a long service life and a high vacuum level. However, when it comes to cleaning processes with a very high occurrence of vapours, in the case of rotary vane vacuum pumps it is not always possible to prevent condensation of the vapours removed by suction in the vacuum pump.
In such cases, the condensate emulsifies with the vacuum pump oil. This can result in the rolling bearings and rotary vanes being insufficiently lubricated, which in turn can lead to premature or increased wear of these parts.
The suction performance and the achievable vacuum may also be adversely affected. These effects can be countered by changing the oil and filters more frequently, but this leads to higher maintenance costs and, therefore, to higher overall operating costs.
Dry-running screw vacuum pumps
Dry-running screw vacuum pumps manufactured by Dr.-Ing. K. Busch GmbH have a long and successful history in a wide range of technical processes. Vacuum pumps that have been specially adapted to meet specific requirements have been successfully used in industrial cleaning and drying technology since 2005, and are noticeably becoming prevalent in this sector as a new standard for vacuum technology.
The COBRA screw vacuum pump does not require oil as an operating fluid. For the drying processes, this offers the advantage that condensate which forms during the compression process does not come into contact with oil, thereby ruling out any possibility of the problems associated with the oil-lubricated rotary vane vacuum pumps.
With the COBRA screw vacuum pump, two screw rotors rotate in opposite directions inside a cylinder and do not come into contact either with one another or with the inner wall of the cylinder. Equally, sealing takes place by means of a non-contact and, therefore, wear-free labyrinth. If vapours condense in the COBRA screw vacuum pump during the compression process, the condensate is forced though the compression chamber with the gas flow and discharged on the exhaust air side.
Liquid volumes of several litres per hour can therefore pass through the pump without any problem. The discharge outlet is designed in such a way that condensate can easily drain off, even when the vacuum pump is at a standstill.
Unlike rotary vane vacuum pumps, COBRA screw vacuum pumps are water-cooled. The elaborate cooling principle ensures a highly homogeneous and stable temperature across the entire pump unit.
The amount of coolant can be regulated by means of a thermostatic valve, thereby allowing ideal temperature control of the vacuum pump for the process and preventing unnecessary water costs. Alternatively, vacuum pumps with a sealed cooling system (heat exchanger) can also be supplied for installations where there is no coolant available on site.
Dry-running screw vacuum pumps manufactured by Dr.-Ing. K. Busch GmbH have a long and successful history in a wide range of technical processes. Vacuum pumps that have been specially adapted to meet specific requirements have been successfully used in industrial cleaning and drying technology since 2005, and are noticeably becoming prevalent in this sector as a new standard for vacuum technology.
The COBRA screw vacuum pump does not require oil as an operating fluid. For the drying processes, this offers the advantage that condensate which forms during the compression process does not come into contact with oil, thereby ruling out any possibility of the problems associated with the oil-lubricated rotary vane vacuum pumps.
With the COBRA screw vacuum pump, two screw rotors rotate in opposite directions inside a cylinder and do not come into contact either with one another or with the inner wall of the cylinder. Equally, sealing takes place by means of a non-contact and, therefore, wear-free labyrinth. If vapours condense in the COBRA screw vacuum pump during the compression process, the condensate is forced though the compression chamber with the gas flow and discharged on the exhaust air side.
Liquid volumes of several litres per hour can therefore pass through the pump without any problem. The discharge outlet is designed in such a way that condensate can easily drain off, even when the vacuum pump is at a standstill.
Unlike rotary vane vacuum pumps, COBRA screw vacuum pumps are water-cooled. The elaborate cooling principle ensures a highly homogeneous and stable temperature across the entire pump unit.
The amount of coolant can be regulated by means of a thermostatic valve, thereby allowing ideal temperature control of the vacuum pump for the process and preventing unnecessary water costs. Alternatively, vacuum pumps with a sealed cooling system (heat exchanger) can also be supplied for installations where there is no coolant available on site.
Vacuum pump comparison
It is not easy to say whether the oil-lubricated rotary vane vacuum pump or the dry-running screw vacuum pump is the better choice for cleaning systems.In technical terms, both pump principles are possible.
For cleaning systems with a relatively low risk of condensation, the rotary vane vacuum pump is the more obvious choice in view of the lower procurement costs. However, if the effects of condensation lead to increased service and maintenance costs, the screw vacuum pump may very quickly offer more favourable overall operating costs.
Before making a decision about the purchase of a vacuum generator, it is therefore very important to seek advice from a vacuum specialist.