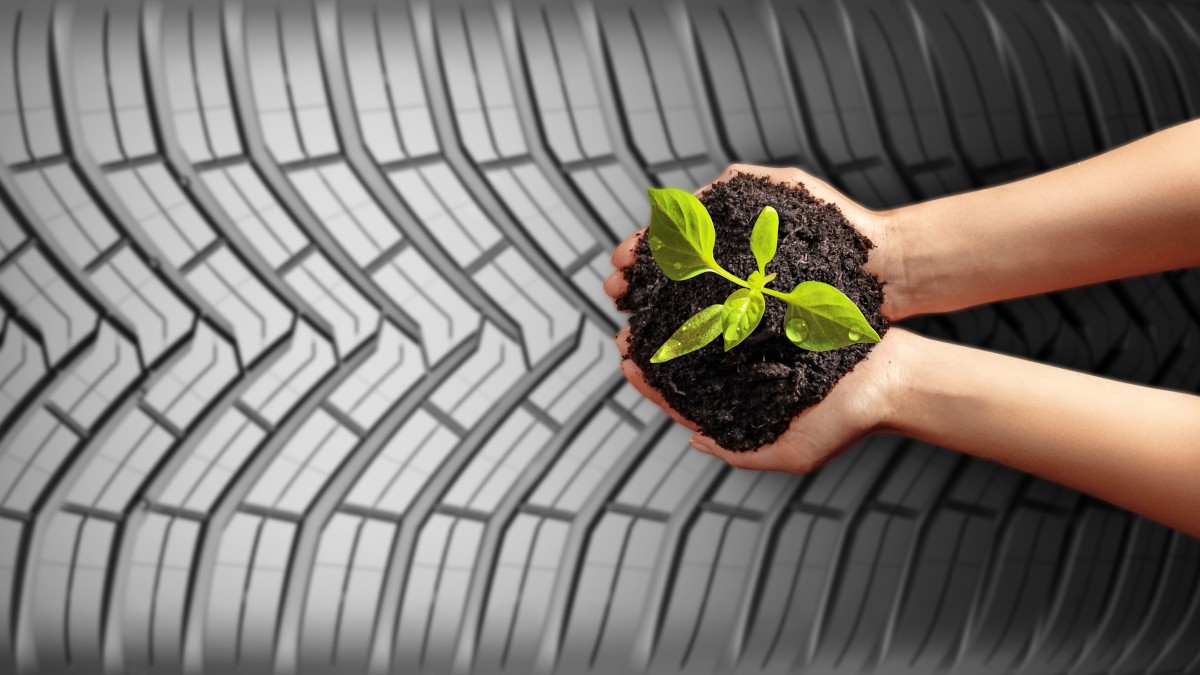
Fig. 1: Continental tires are manufactured using state-of-the-art vacuum technology from Busch. Photo: Continental Reifen GmbH.
New Vacuum Solution Ensures Safe and Sustainable Tires at Continental
Continental Reifen Deutschland GmbH
Continental Reifen Deutschland GmbH produces high-quality tires for cars and vans at its production plant in Aachen, Germany. In its tire manufacturing process, Continental uses an extremely effective and, above all, efficient method of vacuum generation, in which a central vacuum supply from Busch Vacuum Solutions supplies the necessary vacuum to ensure secure handling on three textile cutting machines. In addition to significantly reducing noise in the production room, this vacuum solution also leads to a high level of savings when it comes to the tire manufacturer’s energy and maintenance costs.
Nearly every third vehicle in Europe drives on tires made by Continental, which mixes the natural rubber raw material itself, then extrudes it and, after several intermediate steps, processes it into ready-to-mount tires. A single tire consists essentially of three main components: textile cord, steel wire and a natural rubber mixture. These three basic materials are combined in a specific way in the individual components of the tire, then assembled as carcass and belt, formed into a tire and hardened.
The textile cord consists of a large number of textile threads and is inserted into a calender using a large uncoil device. This is where the textile cord is coated with natural rubber, and a rubberized web is created in the form of a continuous long strip that is less than one millimeter thick. This web is cut to the desired width perpendicular to the thread pattern and rolled into a textile roll again for further processing. The textile material is later directly attached to the innermost layer of rubber. It functions as a reinforcing element on the inside of the tire. The radial orientation of the threads ensures additional stability. This layer primarily influences the carrying capacity of the tire as well as the suspension behavior and handling characteristics.
Nearly every third vehicle in Europe drives on tires made by Continental, which mixes the natural rubber raw material itself, then extrudes it and, after several intermediate steps, processes it into ready-to-mount tires. A single tire consists essentially of three main components: textile cord, steel wire and a natural rubber mixture. These three basic materials are combined in a specific way in the individual components of the tire, then assembled as carcass and belt, formed into a tire and hardened.
The textile cord consists of a large number of textile threads and is inserted into a calender using a large uncoil device. This is where the textile cord is coated with natural rubber, and a rubberized web is created in the form of a continuous long strip that is less than one millimeter thick. This web is cut to the desired width perpendicular to the thread pattern and rolled into a textile roll again for further processing. The textile material is later directly attached to the innermost layer of rubber. It functions as a reinforcing element on the inside of the tire. The radial orientation of the threads ensures additional stability. This layer primarily influences the carrying capacity of the tire as well as the suspension behavior and handling characteristics.
Use of vacuum on textile cutting machines
Vacuum technology is used for handling tasks at the textile cutting machine. The rubberized web is cut to the desired length and then directly applied to another strip using pick-and-place. Here, precise positioning is the most critical aspect when it comes to the quality of the finished textile web. The individual layers need to lay exactly on top of one another. One side channel blower used to be installed in each of three textile cutting machines. These provided the necessary vacuum for handling the strips of textile. The blowers ran constantly at full power and thus consumed enormous amounts of energy. In addition, they created significant noise pollution for the production staff.
Sustainable Busch vacuum supply for textile cutting machines
An employee from Continental Reifen suggested via the internal Idea Management that someone should take a closer look at the vacuum supply of the textile cutting machines. Their primary concern was the acute noise pollution due to the previously used side channel blowers. Because Continental is always searching for potential ways to improve, they decided to look for a more ergonomic and efficient solution. The vacuum experts at Busch Vacuum Solutions recommended using a MINK claw vacuum pump to generate vacuum and initially provided a test system. It only took a couple of days for Ingmar Heinze, Head of Utilities and Sustainable Infrastructure, to become convinced that he had found the right solution for generating vacuum. After the test run, a vacuum system with two MINK MV Synchro vacuum pumps was installed at Continental. This system replaced the previous three side channel blowers and now centrally supplies the necessary vacuum for several textile cutting machines via stainless steel pipes. MINK MV Synchro vacuum pumps are fitted with a frequency converter and demand-driven control unit as standard. The vacuum pumps detect the pumping speed they need to provide in an ongoing process to securely hold the rubberized textile cord and precisely place it.
-
Fig. 2: Vacuum supply with two MINK MV claw vacuum pumps for handling textile cords. Source: Busch Vacuum Solutions.
Benefits of Busch vacuum supply in textile cutting
Fortunately, using this new vacuum system did more than just solve the main problem of noise pollution. The previous side channel blowers reached noise levels of 94 dB. This meant high levels of noise pollution for the staff in the production hall. With the new vacuum system from Busch, the noise level of the vacuum unit cannot even be detected because it is drowned out by normal ambient noise – meaning it is below 72 dB.In addition to the significant noise reduction, the new vacuum system also led to significant energy savings. Thanks to the demand-driven control, full performance is not always used, meaning that the vacuum system often operates with lower rotational speed and power consumption. The system also automatically shuts off when no textile strips need to be held. The power consumption of the previously used blowers was generally 15 kWh. When measurements were taken with the new vacuum system, an average energy consumption of only 800 watts per hour was determined.
That equals energy cost savings of over 90 percent. So the investment promptly paid for itself and, due to the energy aspect, it is eligible for funding from the German Federal Office of Economics and Export Control (BAFA).
The new solution also saves close to 90 percent of the annual maintenance costs. The side channel blowers required intensive repairs and were therefore a source of high costs. MINK MV claw vacuum pumps provide completely dry compression of intake air and thus work without operating fluids such as oil or water. This makes the vacuum pumps virtually maintenance-free. Downtimes for servicing also used to present a problem. For the new vacuum system with two MINK claw vacuum pumps, the few necessary servicing operations can be performed on one of the two vacuum pumps while the other one continues to supply the system with vacuum. This means no more interruptions and higher availability of the textile cutting machines.
The new vacuum system has now been running since January – to Ingmar Heinze’s complete satisfaction.
We are very satisfied with our new vacuum supply for handling textile strips during tire manufacturing. We were not only able to significantly reduce noise pollution for our employees, but were also able to significantly reduce energy consumption and maintenance effort, and increase the productivity of the system. That is a prime example of sustainable improvement!
-
Fig. 3: Pipelines for the vacuum supply of the textile cutting machines at Continental Reifen Deutschland GmbH. Source: Busch Vacuum Solutions.