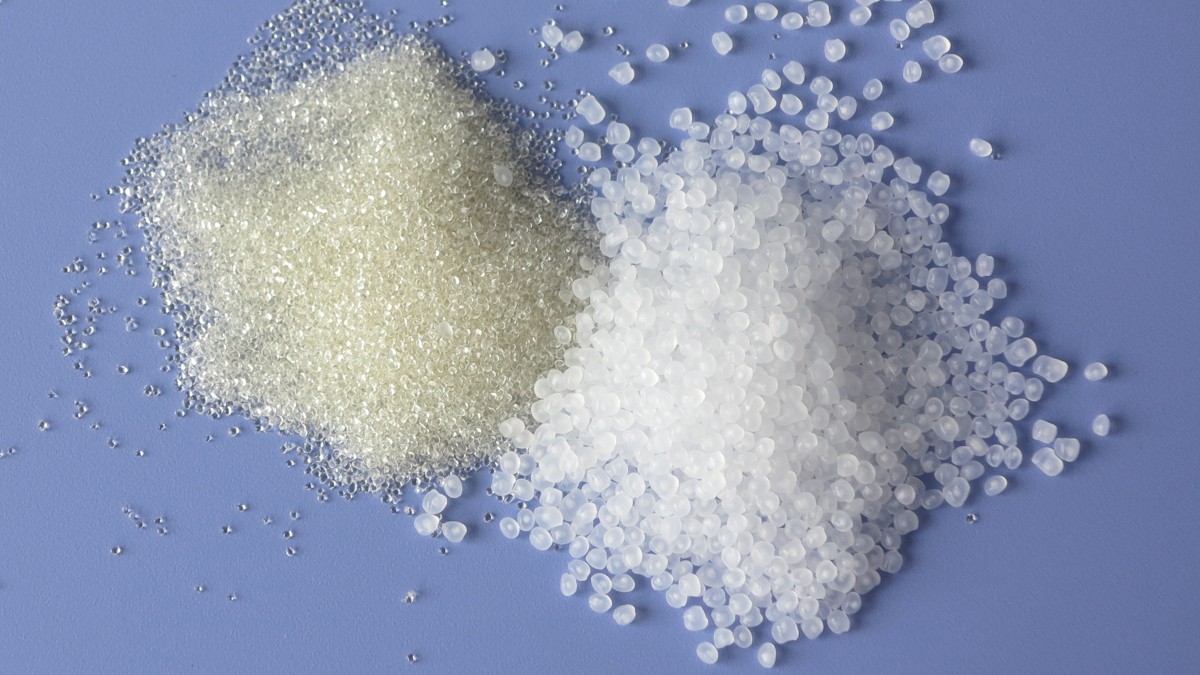
Two materials developed for clients by CompraXX: PLA microgranulate (left) and polypropylene granulate. Source: CompraXX GmbH.
Melt Degassing with Dry Vacuum Technology
CompraXX Compound Technology Centre
CompraXX GmbH operates a comprehensively equipped compound technology centre in Brehna, Germany. The activities of the centre focus on the development of innovative plastics and the design and implementation of sustainable compound strategies. The centre is equipped with the latest plant components, and works to highly advanced technical standards. At the core of the two compounding lines installed at the centre are two twin screw extruders equipped with a variety of degassing units. Maik Weber, the CompraXX managing director, relies exclusively on Busch technology for the vacuum supply. Two Busch PLASTEX degassing units are in operation at the centre.
About CompraXX GmbH
The CompraXX compound technology centre was opened in 2014 in Brehna, near Leipzig. The centre’s objectives are to develop compounds for clients and to produce test series. CompraXX provides support for the entire process: from initial idea to product trials, plant configuration with all necessary components, and final implementation.
PLASTEX degassing units from Busch in the compounding process
The length of both co-rotating twin screw extruders may be altered for maximum versatility. Screw assemblies are prepared in advance for rapid replacement, permitting direct comparison of screw configurations on the same extruder. Additional configurability is provided by the interchangeable degassing equipment, which includes three vacuum side degassing units.
If required by the material being processed, the venting domes of both compounding lines may be connected to Busch Plastex mobile degassing units. These units extract air and steam generated by moist materials in the extruder. Monomers and other decomposition products formed by chemical reactions, temperature and shear stress are also extracted.
-
PLASTEX degassing unit fitted to a twin screw extruder at the CompraXX Compound Technology Centre. Source: Busch Vacuum Solutions.
For managing director Maik Weber, only dry vacuum pumps are suitable for this application. Conventional vacuum pumps have the disadvantage of operating fluid contamination: the extracted gases and vapours mix with the operating fluids. Water ring vacuum pumps are particularly subject to operating fluid contamination, which requires costly water treatment or increased maintenance expenditure. In this environment oil lubricated vacuum pumps also have higher maintenance costs, as oil and filters must be replaced more frequently.
Busch offers the PLASTEX series of dry vacuum systems developed specifically for degassing plastic melt in extruders, a sector in which Busch has decades of experience. PLASTEX degassing units normally use MINK claw vacuum pumps, which are extremely energy efficient and are available with frequency-controlled motors. The MINK claw vacuum systems chosen by Maik Weber are equipped with this form of continuous speed control. His decision was prompted not only by the fact that Busch is the sole supplier of this vacuum technology, it was also based on his positive experience of working with Busch during his long career in the plastics industry.
-
Cross section of a dry MINK claw vacuum pump. Source: Busch Vacuum Solutions.
Busch responded to the special demands of this application by supplying two PLASTEX degassing units matched exactly to requirements. Both PLASTEX units are mounted in mobile frames, when required they are moved into place for connection to the degassing dome. The degassing unit controller is linked to the extruder controller by a simple plug connector, allowing the entire system to be operated automatically. The extruder controller sends start/stop signals and the vacuum setpoint to the PLASTEX unit. The PLASTEX controller transmits the measured vacuum level to the extruder continuously, and can also report an alarm in the event of a setpoint/measured value deviation or equipment fault. The PLASTEX unit also includes an integrated separator system to condense gases and vapours.
This modern vacuum technology has made it possible to process almost all materials in both twin screw compounding extruders, including high-temperature polyamides with melting temperatures of up to 350°C, PP, PC, PC/ABS, POM and PLA. The manufacture of microgranulate products is an additional CompraXX speciality.