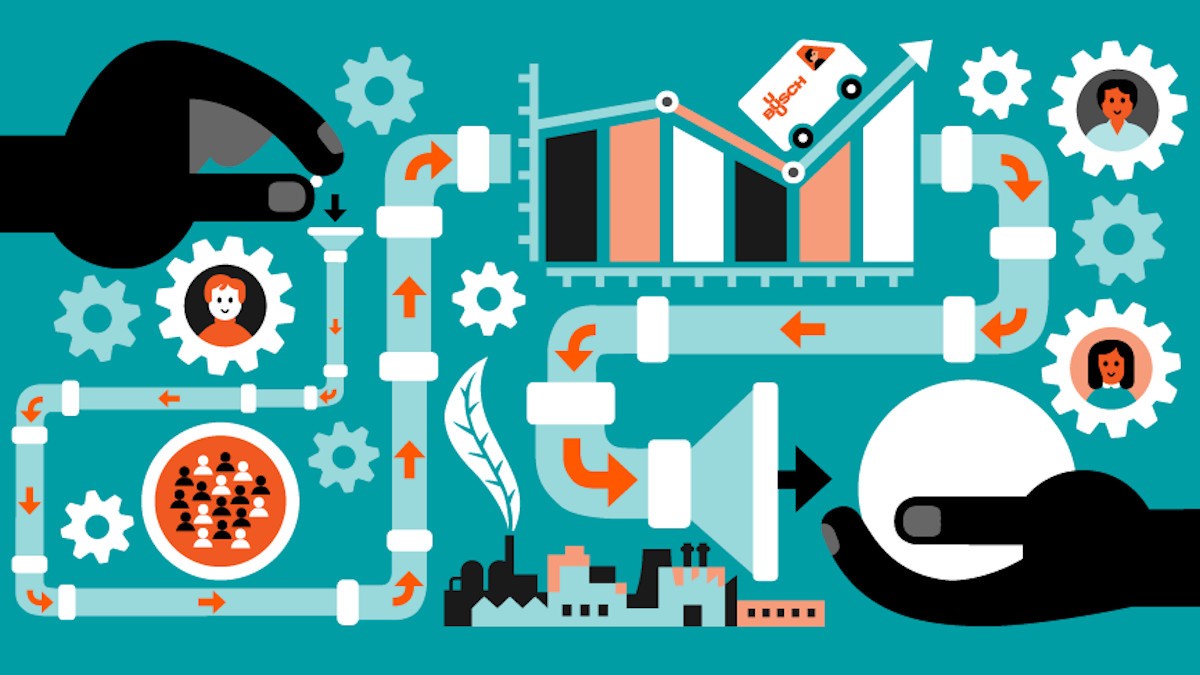
Source: Busch Vacuum Solutions.
10 Considerations for Optimum Use of Vacuum Technology
Vacuum technology plays a huge role in the packaging of foodstuffs and other products. Vacuum is needed for everything from vacuum packaging to tubular bag, blister, and thermoformed packaging. Without vacuum, it would also be impossible to handle and transport cartons or automate palletizing and order picking systems. Various filling machines also use vacuum to feed in the product or handle packaging (pick & place).
In contrast to compressed air technology, many users find vacuum technology quite tricky to understand. This is why vacuum pumps are often used incorrectly or their output is unnecessarily excessive. This results in unsatisfactory results, disruption-prone processes or excessive energy or operating costs. The 10 considerations below have been put together to help you use vacuum technology as effectively and efficiently as possible so that you can optimize processes and cut operating costs.
1. Understanding the physics of vacuum
The main purpose of vacuum pumps and vacuum systems is to suck air out of a closed system in order to generate vacuum. This means they generate a level of pressure that is lower than the atmospheric or ambient pressure.-
Fig. 1: Illustration of vacuum in millibar and percent. Source: Busch Vacuum Solutions.
In packaging technology, you can use vacuum to suction, evacuate, shape, press, hold, move, fill, and transport. The level of vacuum used depends on the application, but always ranges from between 1 and 900 millibars [mbar] (absolute). Assuming atmospheric pressure (air pressure) of 1,000 mbar, this vacuum level would be between 10 and 99.9 percent (fig. 1).
In addition to the vacuum level achieved by a vacuum pump (known as the ultimate pressure), a vacuum pump's pumping speed is another key variable. The pumping speed indicates how much air a vacuum pump is able to extract within a certain period of time. Pumping speed is normally specified in cubic meters per hour [m3/h]. Both technical parameters are related to one another. This relationship is depicted in the so-called pumping speed curve (fig. 2).
-
Fig: 2: Typical pumping speed curve: as the pressure drops, the pumping speed decreases. Source: Busch Vacuum Solutions.
2. Choosing the ideal vacuum generator
There is an array of different types of vacuum technology. The following mechanical vacuum pumps or blowers are mainly used in the field of packaging technology (fig. 3):-
Fig: 3: Comparison of different vacuum pumps and their potential use in packaging. Source: Busch Vacuum Solutions.
1. Dry-running rotary vane vacuum pumps
Dry-running rotary vane vacuum pumps are ideal for a variety of packaging processes. These pumps are able to reach a maximum vacuum level of 100 mbar. However, the pumping speed should not exceed 40 m3/h as the vanes in larger vacuum pumps of this type wear more and thus result in excessive increases in maintenance effort and the related costs.
Dry-running rotary vane vacuum pumps are ideal for a variety of packaging processes. These pumps are able to reach a maximum vacuum level of 100 mbar. However, the pumping speed should not exceed 40 m3/h as the vanes in larger vacuum pumps of this type wear more and thus result in excessive increases in maintenance effort and the related costs.
2. Oil-lubricated rotary vane vacuum pumps
Oil-lubricated rotary vane vacuum pumps achieve a vacuum level of 0.1 mbar. They are the standard in vacuum packaging but may also be used in many other applications throughout industry. Rotary vane vacuum pumps are able to cover pumping speeds from 3 to 1,600 m3/h. The operating fluid oil is transported in an internal circuit.
Oil-lubricated rotary vane vacuum pumps achieve a vacuum level of 0.1 mbar. They are the standard in vacuum packaging but may also be used in many other applications throughout industry. Rotary vane vacuum pumps are able to cover pumping speeds from 3 to 1,600 m3/h. The operating fluid oil is transported in an internal circuit.
3. Dry claw vacuum pumps
Dry claw vacuum pumps do not require any operating fluids in the compression chamber. They have a contact-free operating principle and are therefore nearly maintenance-free. They achieve ultimate pressures of up to 40 mbar and can be regulated from 20 to 80 Hertz rotational speed, which makes them suitable for processes in which changing output requirements should be met on a demand-driven basis. Common pumping speeds are between 40 and 1,000 m3/h.
Dry claw vacuum pumps do not require any operating fluids in the compression chamber. They have a contact-free operating principle and are therefore nearly maintenance-free. They achieve ultimate pressures of up to 40 mbar and can be regulated from 20 to 80 Hertz rotational speed, which makes them suitable for processes in which changing output requirements should be met on a demand-driven basis. Common pumping speeds are between 40 and 1,000 m3/h.
4. Dry screw vacuum pumps
Dry screw vacuum pumps also do not require operating fluids to compress the extracted air. They achieve a vacuum level of 0.1 mbar and below. Since most applications operate at much higher pressures, screw vacuum pumps are generally only used in larger vacuum packaging machines as an alternative to a rotary vane vacuum pump with an additional vacuum booster.
Dry screw vacuum pumps also do not require operating fluids to compress the extracted air. They achieve a vacuum level of 0.1 mbar and below. Since most applications operate at much higher pressures, screw vacuum pumps are generally only used in larger vacuum packaging machines as an alternative to a rotary vane vacuum pump with an additional vacuum booster.
5. Side channel blowers
One of the distinguishing features of side channel blowers is their high pumping speed. Because they only achieve low differential pressures, they are only able to achieve a maximum vacuum level of 500 mbar. They are therefore ideally suited to applications that require a high pumping speed in combination with a low vacuum level. While side channel blowers are maintenance-free, they are less energy-efficient if they are used close to their performance limits.
One of the distinguishing features of side channel blowers is their high pumping speed. Because they only achieve low differential pressures, they are only able to achieve a maximum vacuum level of 500 mbar. They are therefore ideally suited to applications that require a high pumping speed in combination with a low vacuum level. While side channel blowers are maintenance-free, they are less energy-efficient if they are used close to their performance limits.