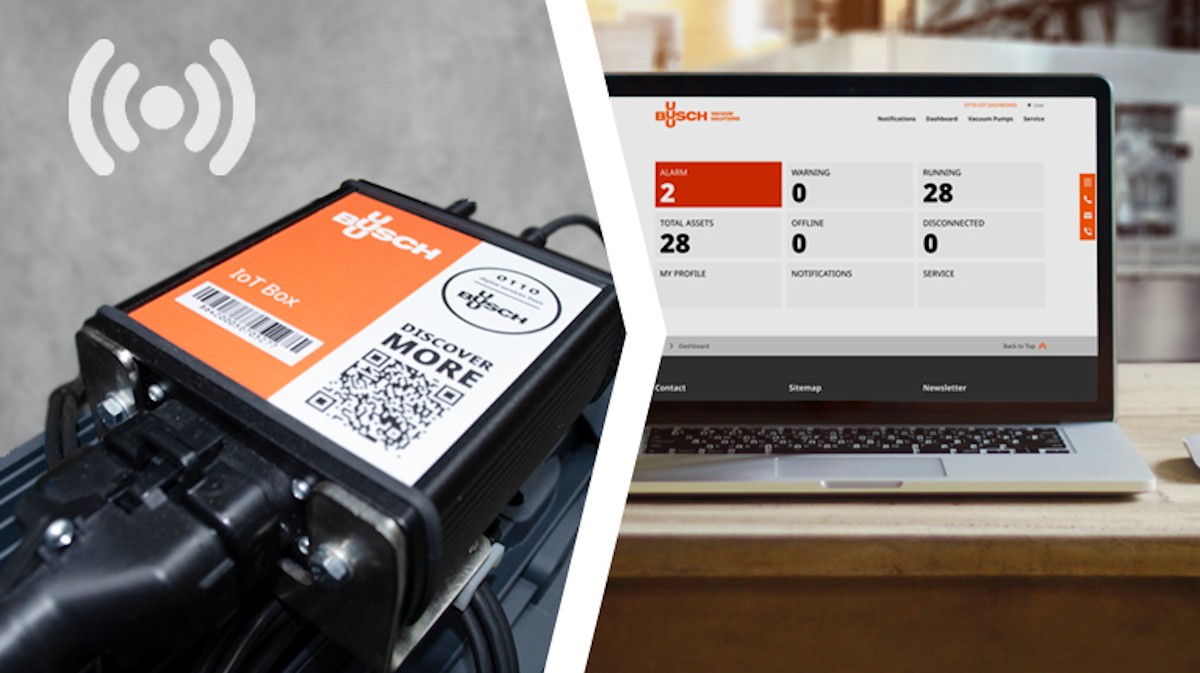
Fuente: Busch Vacuum Solutions.
7 formas de reducir su tiempo de inactividad en la fabricación
El tiempo de inactividad de la producción es uno de los mayores riesgos en la industria de la fabricación. Desde fallos en los equipos hasta escasez de materias primas, cualquier tiempo de inactividad en la fabricación puede provocar importantes pérdidas de beneficios y cuota de mercado.
El tiempo de inactividad planificado es una parada programada de los equipos o procesos de fabricación para realizar el mantenimiento, las inspecciones, las reparaciones, las mejoras o las configuraciones de fabricación. Es esencial planificar el tiempo de inactividad para el mantenimiento con el fin de mantener su equipo en condiciones óptimas y evitar tiempos de inactividad no planificados. Aunque el tiempo de inactividad planificado interrumpe su proceso de fabricación, usted sigue teniendo el control de los procesos de productividad.
El tiempo de inactividad no planificado se produce cuando se produce una parada imprevista o un fallo en su equipo o proceso de fabricación. Esto provoca que los alimentos y bebidas se estropeen si no están envasados, así como costosos retrasos en los plazos de fabricación y entrega. Además, cuando las operaciones son inestables, es más difícil cumplir con las normativas ambientales y las medidas de sostenibilidad. Esto podría provocar un aumento de los incidentes medioambientales.
Por lo tanto, evitar el tiempo de inactividad en la fabricación es clave para garantizar la productividad.
Siga nuestros siete consejos para reducir el tiempo de inactividad de la máquina en su línea de fabricación.
1. Desarrollar un sistema para la identificación y resolución rápida de problemas de fabricación
-
Fuente: Busch Vacuum Solutions.
2. Utilizar análisis preventivos para detectar posibles problemas antes de que se produzcan
-
Fuente: Busch Vacuum Solutions.
3. Implementar un programa de mantenimiento preventivo
De forma rutinaria, puede recopilar información de gran valor sobre su equipo para un mantenimiento sistemático. Con el mantenimiento adecuado, puede reaccionar a fallos o accidentes previstos del equipo antes de que se produzcan. Al reducir la posibilidad de tiempos de inactividad inesperados, su personal puede centrarse en tareas más rentables.
-
Fuente: Piman Khrutmuang - stock.adobe.com.
4. Crear un sistema para hacer frente a fallos y dificultades a medida que surgen
-
Fuente: Busch Vacuum Solutions.
5. Automatizar tantos procesos como sea posible para reducir los errores humanos
Esto dará a su personal más tiempo para centrarse en tareas rentables y desarrollar sus habilidades, lo que se traducirá en mayores beneficios para su empresa y mostrará a su plantilla que son su recurso más valioso.
-
Fuente: Gorodenkoff - stock.adobe.com.
6. Formar a los operarios sobre cómo usar correctamente el equipo
-
Fuente: Busch Vacuum Solutions.
7. Utilizar soluciones de IoT inteligentes
Las soluciones de IoT ayudan a reducir el tiempo de inactividad proporcionándole un sistema que detecta y resuelve rápidamente los problemas de fabricación (consejo 1). Realizan un seguimiento y supervisan su equipo y sus procesos con análisis preventivos, lo que le permite crear un plan de mantenimiento y pedir las piezas de repuesto necesarias con antelación (consejo 2). Los sensores y el análisis de datos permiten que el IoT realice un seguimiento y una monitorización continuos de los datos de optimización del rendimiento y los procesos de su equipo. Esto le permite aplicar el mantenimiento preventivo (consejo 3) y predecir posibles problemas a medida que surgen (consejo 4), reduciendo de forma eficaz la frecuencia de los tiempos de inactividad planificados o no planificados. El IoT también permite la automatización de tareas, reduciendo el tiempo necesario para realizarlas y, en última instancia, aumentando la productividad y reduciendo los errores humanos (consejo 5). Gracias a sus herramientas fáciles de usar, aprender a utilizar el IoT es muy sencillo. Su personal podrá utilizarlo correctamente en muy poco tiempo (consejo 6). ¿Le gustaría optimizar su proceso instalando un sistema IoT? Descubra cómo el panel de IoT de Busch y la Busch Vacuum App pueden ayudarle con la monitorización de su proceso de vacío. Busch también le proporciona un mantenimiento preventivo mediante el envío automático de un especialista de servicio basado en el análisis de los datos recopilados cuando sea necesario.
Preguntas frecuentes
¿Qué es el tiempo de inactividad de la fabricación?
- El tiempo de inactividad es el tiempo durante el cual se detiene un proceso de fabricación. Existen dos tipos de tiempo de inactividad: el planificado y el no planificado.
- El tiempo de inactividad planificado es una parada programada de los equipos de fabricación para realizar el mantenimiento, las inspecciones, las reparaciones y las mejoras.
- El tiempo de inactividad no planificado es una parada imprevista o un fallo de su equipo o proceso de fabricación.
¿Cómo calcula el tiempo de inactividad de la fabricación?
Calcule los costes del tiempo de inactividad de la fabricación mediante la siguiente fórmula:
% de tiempo de inactividad = (cantidad de tiempo de inactividad/tiempo de funcionamiento planificado) * 100
¿Cuál es el tiempo de inactividad medio de la fabricación?
Los fabricantes pierden una media de 800 horas al año, o más de 15 horas semanales, del tiempo de fabricación debido al tiempo de inactividad del equipo.
Consideremos un escenario común para una fábrica de queso parmesano:
un bloque de queso parmesano pesa una media de 42 kg. El precio estimado es de 9 euros por kilo, lo que equivale a un bloque de parmesano con un valor total de 378 euros. Se pueden producir tres bloques de queso por minuto, lo que da como resultado 68 040 euros por hora.
Si la fábrica de parmesano sufriera 15 horas de tiempo de inactividad no planificado debido a fallos en los equipos en una semana, perderían 1 020 600 euros.