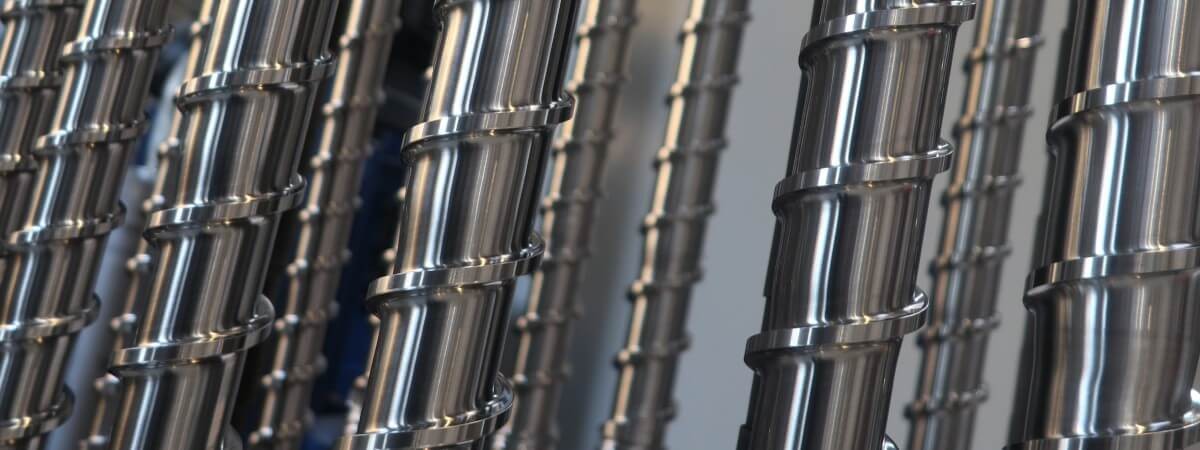
Afb. 1: Plasmagenitreerde extruderschroef klaar voor het boog-PVD-coatingproces. Bron: Busch Vacuum Solutions.
Schroefvacuümpomp voor boog-PVD-coating
Het afwerken van oppervlakken van grote metalen werktuigen en componenten is de hoofdactiviteit van Dreistegen GmbH. Het Duitse bedrijf gebruikt verschillende diffusielaagbehandelingen, zoals nitreren, nitrocarboneren of oxideren en coatingtechnieken, zoals fysieke dampafzetting (physical vapor deposition, PVD) en chemische dampafzetting (chemical vapor deposition, CVD), onder de toepassing van koud plasma.
Voor het aanbrengen van verharde, dunne lagen door middel van boogverdamping (boog-PVD) onder vacuüm vertrouwt Dreistegen op een COBRA NC schroefvacuümpomp van Busch Vacuum Solutions. Als voorpomp werkt het systeem met twee parallelle turbomoleculaire vacuümpompen om het vacuüm op te wekken in de coatingkamer.
In 2008 startte Dr. Oliver Kayser zijn eigen bedrijf in de gebouwen van een oude textielfabriek in de stad Monschau in het Duitse Eifelgebied. Het oude industriële gebouw, dat meer dan 200 jaar oud is, werd door Kayser nieuw leven ingeblazen. Zijn bedrijf concentreerde zich initieel op plasma-nitreren en PVD-coating voor werktuigen en componenten. Wat begon als een kleine onderneming in gedeeltelijk vervallen gebouwen is nu uitgegroeid tot een modern middelgroot bedrijf met 40 medewerkers, die speciale dunne lagen aanbrengen op werkstukken om deze te beschermen tegen slijtage en corrosie. Bovendien helpen deze coatings residuvorming op de oppervlakken te stoppen. Op deze manier worden parasitische reacties met andere materialen voorkomen. Veel van Dreistegen's klanten komen uit de kunststofverwerkingssector en plaatsen opdrachten bij het bedrijf voor het coaten van spuitgegoten, geëxtrudeerde of vormgeblazen werktuigen. Dr. Oliver Kayser ontwikkelde een speciale vorm van coating, die het gesmolten plastic beschermt tegen degradatie door de katalytische stimulatie van het werktuigoppervlak. Als gevolg hiervan blijft het plastic niet plakken aan de mal. Voor de operator betekent dit dat materiaal en kleur snel kunnen worden gewijzigd tijdens extrusie of spuitgieten. Bovendien kan de hoeveelheid mallosmiddel worden verminderd of kan het gebruik van een middel helemaal worden geëlimineerd.
Dreistegen verzorgt ook de coating van vormgevingswerktuigen en spuitgietmatrijzen, hoofdzakelijk voor de autosector en leveranciers daarvan. Dreistegen biedt een spectrum van verschillende nitreer-, PVD- en CVD-coatings en -afwerkingen aan.
Dr. Oliver Kayser is nauw betrokken bij moderne coatingtechnieken en experimenteert altijd met manieren om de dunne lagen te optimaliseren, om deze specifieke eigenschappen te geven die nuttig zijn voor zijn klanten in specifieke toepassingen. Dit omvat ook het optimaliseren van de technologie in zijn fabriek.
Het boog-PVD-coatingsysteem dat hij heeft aangeschaft, met een bruikbare draaidiameter van 1.200 millimeter en een bruikbare hoogte van 1.500 millimeter, was oorspronkelijk geïnstalleerd met een vacuümsysteem dat bestond uit een oliegesmeerde draaischuifvacuümpomp als voorpomp en twee vacuümboosters. Dit systeem zorgde voor de vacuümopwekking die nodig was voor de twee turbomoleculaire vacuümpompen die parallel werkten. Kayser verving deze volledige voorpompvacuümunit door een COBRA NC 400 B van Busch. Deze schroefvacuümpomp bereikt een einddruk van 0,05 millibar (hPa) in een enkele trap. Hierdoor is het in staat om de oude drietraps vacuümunit van een andere fabrikant te verbeteren wat betreft einddruk en pompsnelheid, terwijl tegelijkertijd een veel betere energie-efficiëntie wordt bereikt.
Kayser stelt de stabiele en betrouwbare prestaties en de stille werking van de COBRA NC op prijs. Bovendien neemt de COBRA veel minder ruimte in dan het eerdere vacuümsysteem.
-
Afb. 2: Systeem voor boog-PVC-coating met behulp van een COBRA NC schroefvacuümpomp als voorpomp voor twee turbomoleculaire vacuümpompen. Bron: Busch Vacuum Solutions.
Kayser deed ook zorgvuldig onderzoek naar schroefvacuümpompen van een andere fabrikant. Deze had een eenzijdig lagersysteem dat werd aangedreven door een speciale motor die moeilijk te vervangen was.
Kayser was onder de indruk van het modulaire, functionele ontwerp van de COBRA, met een dubbelzijdig lagersysteem op de twee schroevenrotoren en de aangeflensde standaardmotor, die op elk willekeurig moment kunnen worden vervangen.
Van het laden van de coatingkamer tot het verwijderen van de werkstukken duurt het werkelijke boog-PVD-proces tussen de 14 en 18 uur. De COBRA NC vacuümpomp blijft in bedrijf tijdens de korte onderbrekingen tussen twee processen voor het samenstellen en verwijderen van de werkstukken. Dit betekent dat de COBRA NC het hele jaar door werkt. Voor Kayser is de huidige opstelling voor het opwekken van het procesvacuüm in zijn coatingsysteem – bestaande uit de combinatie van een COBRA NC schroefvacuümpomp en twee parallelle downstream turbomoleculaire vacuümpompen – de ideale oplossing.
Het basismateriaal van het werkstuk moet een bepaalde oppervlaktehardheid hebben voordat het een boog-PVD-coating kan krijgen. Om deze reden bereidt Dreistegen de werkstukken over het algemeen voor op coating door middel van een plasma-nitreerproces.
De met plasma genitreerde werkstukken worden vervolgens gezandstraald met glaskorrels of licht gepolijst als dit nodig is. Zodra de werkstukken zijn gereinigd, worden ze bevestigd op houders en in de coatingkamer geladen. De gesloten kamer wordt vervolgens leeggezogen tot een vacuümniveau van 10-5 mbar (hPa). De werkstukken in de kamer worden vervolgens verhit tot maximaal 450 °C.
Zodra de procestemperatuur is bereikt, worden de natuurlijke oxiden geërodeerd in een argon gloeiontladingsplasma. De boogverdampers worden vervolgens ontbrand en kunnen zich hierdoor verplaatsen. Ze blijven echter verbonden met de donormaterialen titanium, chroom of legeringen ervan, dankzij de permanente magneten die aan de achterzijde zijn bevestigd. Er kunnen ook aluminiumlegeringen of andere metalen voor worden gebruikt.
In de boog wordt het donormateriaal verdampt in een explosieachtig proces en de individuele dampdeeltjes worden vrijwel geheel geïoniseerd. Elektrisch primen (BIAS) wordt gebruikt om de ionen op de werkstukken te schieten. Reactieve gassen zoals stikstof, acetyleen, methaan, zuurstof en waterstof worden ook toegevoegd. De toevoeging van deze gassen veroorzaakt een drukstijging in de coatingkamer tot 10-2 mbar (hPa). De reactieve gassen die zijn vrijgekomen uit het plasma binden zich aan de metaalionen op het oppervlak van het werkstuk om de harde coatinglaag te vormen. Typische samenstellingen omvatten titaniumnitride (TiN), titaniumcarbonitride (TiCN), chroomnitride (CrN), aluminiumtitaniumnitride (AlTiN) en chroomoxide (Cr2O3). Dankzij de hoge energie van de deeltjes en de straalkracht is de gecreëerde coating uitzonderlijk adhesief en uniform, zelfs op werkstukken met complexe vormen. De dunne lagen die worden gemaakt door Dreistegen met behulp van boogverdamping bereiken hardheidsniveaus van meer dan 2.000 HV (hardheid van Vickers).
Vergeleken met de oorspronkelijke vacuümunit is de hoeveelheid onderhoudswerk dat nodig is aan het vacuümsysteem aanzienlijk lager, dankzij het gebruik van de COBRA NC schroefvacuümpomp.
Het enige werk dat nodig is aan de schroefvacuümpomp is een jaarlijkse vervanging van de tandwielolie.
Dr. Oliver Kayser onderstreept dat de absolute bedrijfsveiligheid van de schroefvacuümpomp erg belangrijk voor hem is. Uitval van de vacuümpomp tijdens het proces zou enorme schade veroorzaken, aangezien het de dure werkstukken onbruikbaar zou maken.
Na twee jaar ononderbroken bedrijf van de COBRA NC zegt Dr. Oliver Kayser het volgende:
Wij bij Dreistegen zijn tevreden Busch klanten en zijn onder de indruk van de kwaliteit van de machines.