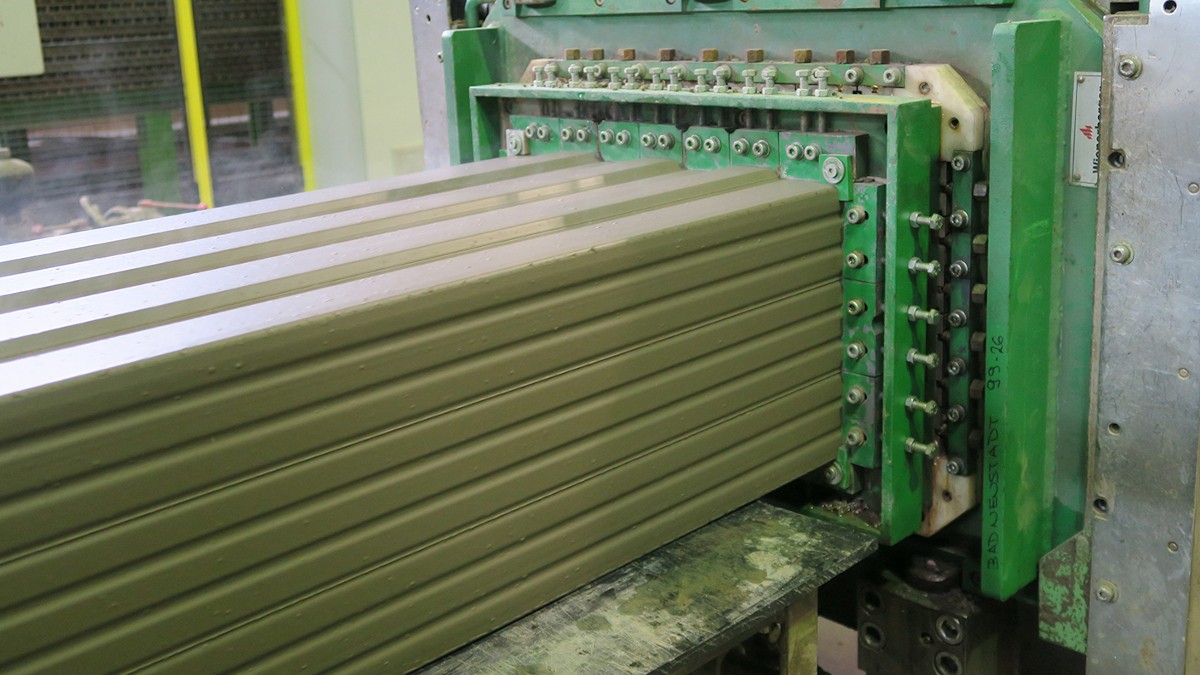
Fig. 1: Poroton backing bricks are manufactured at the Wienerberger brick factory in Bad Neustadt, Germany. Source: Busch Vacuum Solutions.
High-Quality Bricks Thanks to State-of-the-Art Vacuum Technology
Wienerberger GmbH
At the Wienerberger GmbH brick factory in Bad Neustadt, vacuum technology is used for degassing the clay mixture in the extrusion press. A vacuum system with a dry COBRA NX screw vacuum pump as the core element is being used for generating the necessary vacuum. This vacuum pump generates the vacuum needed without any oil and completely contact-free. The variable speed drive enables demand-driven control and ensures that the desired vacuum can be precisely maintained independent of how much moisture the material contains. The modern vacuum system has provided Wienerberger with significant benefits when it comes to efficiency, quality and operational safety.
About Wienerberger GmbH
The brick and tile factory in Bad Neustadt was founded in 1951 and was sold by the family company Gessner to Wienerberger Ziegelindustrie GmbH in 2001 to ensure the long-term success of the enterprise. In addition to Poroton backing bricks, the factory also produces highly efficient thermal insulation bricks in line with the requirements of new energy saving regulations. Wienerberger Ziegelindustrie GmbH, headquartered in Hanover, Germany, is part of Wienerberger AG, an internationally active group with its head office in Vienna, Austria.An extrusion press is used to manufacture various Poroton backing bricks. The material is degassed as it passes through the vacuum chamber between the twin-shaft mixer and the extrusion press. This prevents air pockets during extrusion and thus guarantees pore-free castings. This also significantly increases their stability, preventing them from deforming before they dry and ensuring dimensional accuracy of the finished brick. The porosity necessary for good thermal insulation properties after they are fired is ensured using supplemental materials such as saw dust, paper pulp, and polystyrene. These burn away during the firing process, leaving pores in the material.
Previously used vacuum supply required high maintenance effort
In earlier years, the Wienerberger brick factory in Bad Neustadt used a once-through oil-lubricated rotary vane vacuum pump. When the previously used vacuum pump needed a general overhaul, plant manager Wolfram Tittel began to search for ways to optimize his vacuum supply. His primary goal was to minimize oil consumption, the acuumulation of oil emulsion and maintenance effort. So he spoke with the vacuum specialists from Busch Vacuum Solutions, who performed a detailed analysis of this application and then suggested a completely new overall solution for vacuum generation.
Busch clay degassing system for highest level of operational safety
Busch developed a clay degassing system specifically for this purpose. At its core is a COBRA NX screw vacuum pump, which is used to extract air and water vapor, and to compress and expel them again completely dry, i.e. without the use of oil or any other operating fluids. The standing filter upstream of the vacuum pump has been optimized for dust and particles from clay and loam masses. The frequency-controlled motor of the vacuum pump and the integrated demand-driven control unit make it possible to precisely maintain the defined vacuum level in the vacuum chamber. Due to its design, this vacuum pump is able to constantly maintain all the prescribed vacuum levels between one millibar and atmospheric pressure throughout the whole process.Depending on the level of moisture in the clay mixture, there are varying levels of water vapor that need to be extracted from the vacuum chamber. This means that the pumping speed of the vacuum pump has to be increased via a higher motor frequency for very moist material because, in addition to the actual evacuation of air, higher amounts of water vapor also need to be suctioned out. If the material contains less moisture, the pumping speed can be reduced again. As a result, the vacuum level in the vacuum chamber remains constant at all times. In addition, the desired moisture level between 19.5% and 21.5% can be precisely maintained when the material is pressed into the nose piece during extrusion. This ensures a high level of operational safety during the clay degassing process while maintaining flexible process conditions.
The vacuum specialists from Busch dismantled the COBRA vacuum pump used after one year of running time in the manufacturing plant and examined it thoroughly. They did not find any damage or signs of wear and tear from dust or particles penetrating the vacuum pump. The maintenance work is significantly less than that required for an oil-lubricated vacuum pump. Thanks to the contact-free operating principle of the COBRA screw vacuum pump, there is no wear, thus no wearing parts need to be replaced. Oil-free operation also eliminates the previous necessary oil filter changes. In addition, all work and costs for procuring the oil and disposing of the oil emulsion have also become unnecessary.
-
Fig. 2: COBRA NX vacuum system for degassing clay bricks at Wienerberger. Source: Busch Vacuum Solutions.
Enormous energy and water savings
As a brick factory whose energy management complies with the DIN 50001 standard, the possibility of reducing energy consumption for vacuum generation was of great significance. The newly deployed vacuum pump usually operates in a range from 30 to 35 Hertz and only operates at full load when the water vapor level is very high.Further measures to optimize the vacuum system at the beginning of 2021 have now made it possible for Wienerberger to save additional water and wastewater costs. A closed water circuit is now used for cooling, eliminating the need for adding fresh water and disposing of wastewater. Together with the vacuum experts from Busch, Wienerberger was able to set up an even more efficient vacuum generation for manufacturing clay bricks.
-
Fig. 3: Operating principle of a COBRA NX screw vacuum pump. Source: Busch Vacuum Solutions.