Groß-Rotorblattfertigung GmbH achieved energy savings of at least 50% for the vacuum supply for rotor blade production thanks to the use of a new centralized vacuum system.
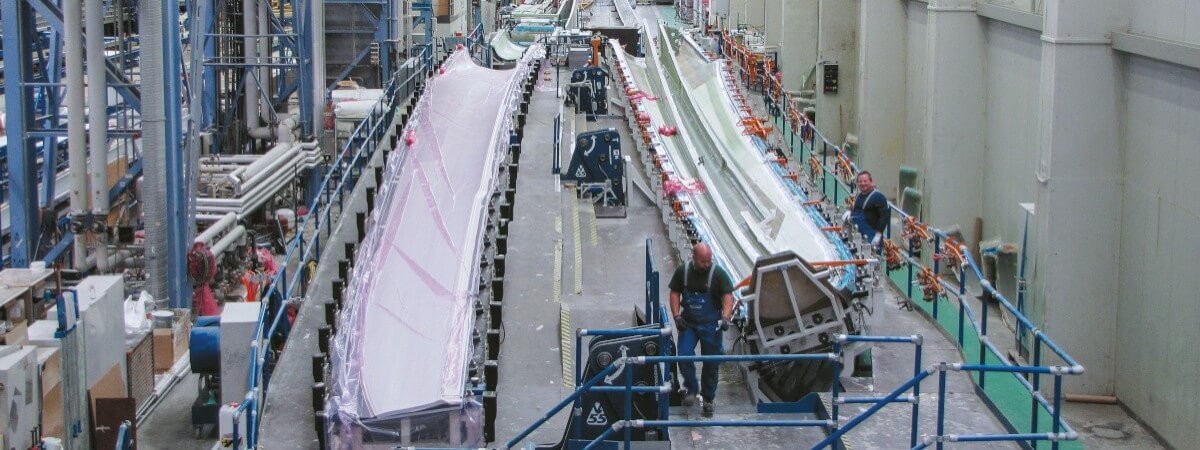
Fig. 1: Groß-Rotorblattfertigung GmbH Rotor blade construction. Source: Busch Vacuum Solutions.
Central Vacuum Supply Brings 50% Energy Savings in Rotor Blade Production
Groß-Rotorblattfertigung GmbH
Groß-Rotorblattfertigung GmbH achieved energy savings of at least 50% for the vacuum supply for rotor blade production thanks to the use of a new centralized vacuum system.
The plant, which belongs to the ENERCON Group, was also able to avoid noise and heat emissions in the production hall by centralizing vacuum generation for resin infusion. The vacuum supply, which was designed and implemented by Dr.-Ing. K. Busch GmbH, is housed in a separate room and provides the vacuum for all of Groß-Rotorblattfertigung.
About Enercon
ENERCON has been producing rotor blades for wind turbines on the site of a former steel foundry in Magdeburg-Rothensee since 2001. Today there are six different ENERCON Group companies located there with a total of around 2,500 employees that deal with building components for wind turbines. Groß-Rotorblattfertigung produces different types of rotor blades with lengths currently up to 45 metres in three-shift operation.Process of rotor blade production for wind turbines
The individual components are produced using a vacuum infusion process and assembled afterwards. Different layers of glass fibres and other materials are manually inserted in a sandwich construction. These are covered with a plastic foil that is applied in a way that creates an air-tight seal along the edges of the form. For safety reasons, a second foil is laid on top that is also applied in a manner that creates an air-tight seal. This is intended to prevent negative effects on the process or on the quality of the component to be manufactured due to leaks that may occur. Afterwards, vacuum is applied to remove/extract the air between the form and the plastic foils. After testing for leaks, resin infusion into the component begins. Due to the vacuum, the resin flows into all areas and spaces in the component and thus completely saturates it. After the resin is tempered and hardened, the form can be aerated back to atmospheric pressure and the component can be removed.In the past, decentralized vacuum units with oil-lubricated rotary vane vacuum pumps were used. These pumps were sometimes permanently installed or used as mobile units at different forms. They supplied the individual forms with vacuum using tubes. Overall, 36 rotary vane vacuum pumps were used to evacuate forms and infuse the components, which was performed in three-shift continuous operation at Groß-Rotorblattfertigung. The vacuum was controlled manually using valves.
Central vacuum solution and its benefits for the customer
Thomas Giesecke was responsible for the process planning department and was searching for a technically optimized solution in 2016. The disadvantages of the existing vacuum supply were due to the fact that waste heat from the rotary vane vacuum pumps was emitted directly into the production hall. Noise emission in the workplace was also very high due to the number of vacuum pumps. In addition, Thomas Giesecke was looking for a vacuum supply that would work without oil as an operating fluid because oils or oil fumes have a separating effect on the glass fibre and core materials and can therefore negatively affect the production process. His vision was also to have a certain vacuum level continually available that would make manual regulation unnecessary and thus make the process stable, safe and transparent. After precisely analysing the current state, the vacuum specialists from Dr.-Ing. K. Busch GmbH designed a vacuum supply system consisting of individual dry, oil-free COBRA NX screw vacuum pump (Fig.: 2) vacuum modules. This system was constructed in such a way that its dimensions fit into an already existing separate engineering room. The control cabinet with the control system is also located in this room.-
Fig. 2: COBRA NX screw vacuum pump cross-sectional view. Source: Busch Vacuum Solutions.
The system is set up so that four screw vacuum pumps are connected to a ring main that runs through the entire Groß-Rotorblattfertigung hall. The prescribed vacuum level in this line is continually and precisely maintained. This is used for fast initial evacuation of the forms. Two further COBRA NX vacuum pumps are connected to a second ring main that is independent from the first one. After initial evacuation, this vacuum circuit serves to infuse the resin into the rotor blade components with the same vacuum level. Together with Thomas Giesecke and his team, Marcus Kempf as programmer and Dirk Sztuck as project coordinator, the vacuum specialists from Busch optimized the vacuum supply so that the so-called vacuum control panels are interposed between the individual forms and both of the vacuum circuits. Inside are valves that automatically switch from one vacuum circuit to the other when initial evacuation is finished and resin infusion begins.
The two-circuit solution and intelligent vacuum control technology in the vacuum control panels directly at the rotor-blade forms enable reliable and safe implementation of the resin infusion process. This control system also enables all process data to be recorded and saved. The level of vacuum required varies widely because the processes at all connected forms are performed at different times. The demand-based control system continually recognizes the required pumping speed and appropriately switches the vacuum modules on or off in a cascade. One of the COBRA NX screw vacuum pumps is frequency-controlled. It usually goes into operation first. Once it has achieved full capacity, the next vacuum pump is turned on and the frequency-controlled vacuum pump reduces its capacity if needed. If the pumping speed requirements increase, further vacuum pumps automatically switch on. This system works on a rolling basis. This means that the control system takes the operating hours of each individual vacuum pump into account and puts them into operation on an alternating basis so that all the pumps have the same number of operating hours. Because the centralized vacuum system (Fig.: 3) is installed in a separate room, there are no more adverse effects whatsoever in the workplace due to noise or heat emissions.
The intelligent vacuum control technology in the vacuum control panels directly at the rotor-blade forms enable reliable and safe implementation of the resin infusion process.
-
Fig. 3: Central vacuum supply with COBRA NX screw vacuum pumps as individual vacuum modules. Source: Busch Vacuum Solutions.
The vacuum system from Busch has been in operation since November 2016 and Thomas Giesecke and his team are very satisfied because all requirements for the new vacuum supply have been completely fulfilled. A further positive effect arose that no one necessarily had focused on when planning began: energy efficiency was increased considerably. Thomas Giesecke confirms that at least 50 percent energy savings were possible with the new vacuum system.
This becomes apparent simply when one considers the total number of 36 rotary vane vacuum pumps that were previously in operation, as opposed to the six COBRA NX screw vacuum pumps in the new system. A seventh COBRA NX serves purely as a stand-by vacuum pump. The forms for the smaller rotor blade components are still evacuated with existing rotary vane vacuum pumps. But now, these will be gradually connected to the new system, which is already designed for this in terms of capacity. Reducing the number of vacuum generators is not the only aspect that enabled a drastic reduction in energy consumption; demand-based control also played a role. Previously, vacuum pumps were often operating 24 hours a day. Now, each individual screw vacuum pump has significantly shorter operating times. This in turn reduces the maintenance required, which is already significantly less for screw vacuum pumps than for rotary vane vacuum pumps, minimizing maintenance costs. Maintenance can be performed during operation by disengaging the individual COBRA NX vacuum pumps and operating the stand-by vacuum pump in their places. Groß-Rotorblattfertigung has already signed an all-inclusive maintenance agreement with Busch. This guarantees that Busch will perform all maintenance work for an annual fixed amount and takes full responsibility for the function and operational readiness of the vacuum supply.
Thomas Giesecke confirms that at least 50 percent energy savings were possible with the new vacuum system.