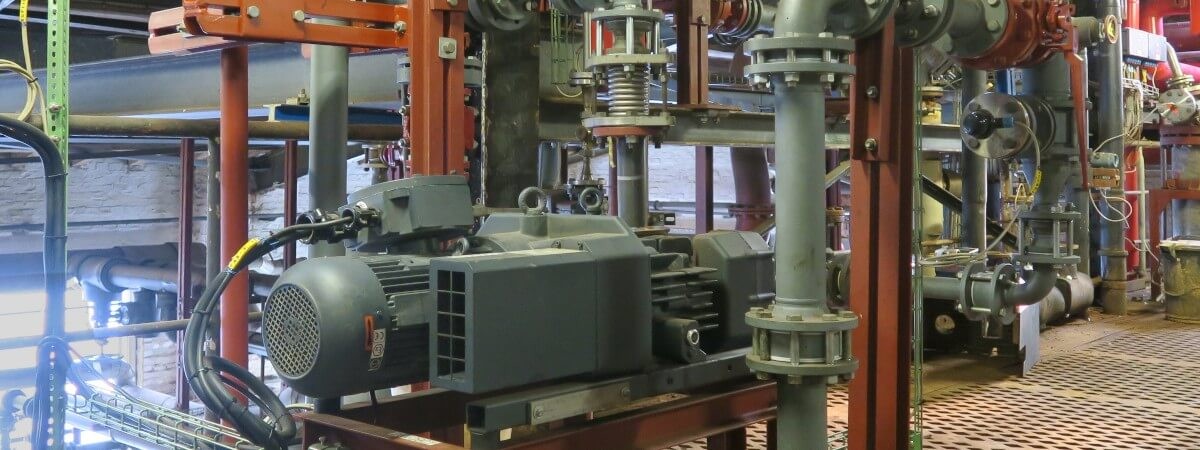
Fig. 1: MINK claw vacuum pump for conveying exhaust gases containing chlorinated hydrocarbons at Nouryon. Source: Busch Vacuum Solutions.
Safe and Efficient Exhaust Gas Cleaning Using Modern Vacuum Technology
Nouryon Akzo Nobel Industrial Chemicals GmbH
The chlorinated hydrocarbons produced by Nouryon are used as a basic chemical in many areas, for example in the manufacture of plastics and building materials, in the manufacture of paints or in pharmaceuticals. Methane chlorination produces exhaust gases containing chlorinated hydrocarbons that must be extracted and cleaned before they can be released into the ambient air. The exhaust gases generated when filling or decanting stationary or mobile tanks are also extracted and cleaned using the same system. In addition, during maintenance work on the system, it must be ensured that no chlorinated hydrocarbons are present. The exhaust gases are also extracted via the MINK claw vacuum pump, and the system or system part is then inerted with nitrogen.
In the process steps upstream of the vacuum pump, the exhaust gases are sucked in at a vacuum of -10 to -30 millibar, which corresponds to absolute pressures of 990 mbar to 970 mbar. The exhaust gases are compressed in the vacuum pump and leave it at an overpressure of around 150 mbar. This overpressure conveys the exhaust gases through the downstream coolers and the activated carbon filter.
The MINK claw vacuum pump (Fig. 1) continuously conveys the exhaust gases through the complete cleaning process with all cleaning stages switched in succession. All system parts in which exhaust gases containing chlorinated hydrocarbons are produced are connected via pipes to a collecting tank, which is under a slight vacuum due to the vacuum pump. The exhaust gases are thus sucked into this container and then flow through a packed column for neutralization washing. After neutralization, the exhaust gases are compressed in the MINK claw vacuum pump and conveyed to a cooler where they are cooled to 0°C. This causes the water vapor, which was mainly introduced during neutralization washing, to condense. In a downstream deep-freezer, the exhaust gases are cooled to -25°C and thus most of the chlorinated hydrocarbons are condensed out of the gas stream. The remaining chlorinated hydrocarbons are then filtered out by an activated carbon filter so that the purified gas can be released into the atmosphere as exhaust air. The cleaning system works in accordance with TA Luft (Technical Instructions on Air Quality Control) and is designated as Ex zone 2.
The MINK claw vacuum pump works demand-driven via a variable speed drive and is controlled via a pressure sensor in the collecting tank. This means that it adjusts its pumping speed by varying the rotational speed according to the amount of exhaust gas present.
As Sergej Diner, the operating engineer responsible at Nouryon, points out, the amount of exhaust gas can vary greatly. During the day, when all processes are running at full capacity, more exhaust gases are produced than during the night. The system is continuously in operation and is only switched off for maintenance work. Before this maintenance work, when the system must be completely free from chlorinated hydrocarbons, the highest quantities of gas are produced before inerting with nitrogen.
Situation before Busch solution
In the past, the exhaust gases were conveyed through the cleaning system by a rotary lobe blower. The blower stage corroded strongly after only a short time due to the aggressive gases containing chlorinated hydrocarbons. This corrosion and abrasion reduced the performance of the blower and the necessary pressure differential could no longer be applied. As a result, the exhaust gases could no longer be reliably extracted. In addition, the blower stage had to be replaced every two years, which resulted in downtimes and costs of around EUR 35,000.
Busch solution and its benefits for the customer
For operating engineer Sergej Diner, this was an extremely unsatisfactory situation. He therefore contacted Busch Vacuum Solutions, especially as he already had good experience with Busch vacuum pumps in another process. After an analysis of the process and the requirements, the vacuum specialists from Busch recommended the use of a MINK claw vacuum pump. It is certified according to the necessary ATEX requirements (inside and outside: II 2G IIB3 T3) and has an anti-corrosion coating in the compression stage as standard. In addition, it has a higher operating temperature than a rotary lobe blower, meaning that condensation of the exhaust gases inside the vacuum pump can be avoided as far as possible. The MINK claw vacuum pump is gas-tight and the bearings are pressurized with nitrogen so that no exhaust gases can escape through the bearings.
Thanks to the contact-free compression principle of claw vacuum technology, there is no contamination between an operating fluid and the exhaust gases.
-
Cutaway drawing of a MINK claw vacuum pump. Source: Busch Vacuum Solutions.
The MINK claw vacuum pump has been in operation since December 2017. After six months of non-stop operation, it was opened by a Busch service engineer as a precaution to check for possible signs of wear. It was found that the vacuum pump showed no signs of wear or corrosion.
Sergej Diner confirms that, even after more than a year of operation, there were no malfunctions, a drop in performance or even a vacuum pump failure – and that his cleaning process therefore runs continuously without problems.