As part of the energy-saving initiative, the old vacuum supply for the wide range of packaging machines underwent a critical assessment. Working with a vacuum expert, the company switched from a decentralized to a centralized vacuum supply, which now supplies the vacuum required for all of the packaging machines. The new system consists of four demand-driven MINK MV Synchro claw vacuum pumps from Busch Vacuum Solutions. As a result of this switch, the company has achieved energy savings of 70 percent.
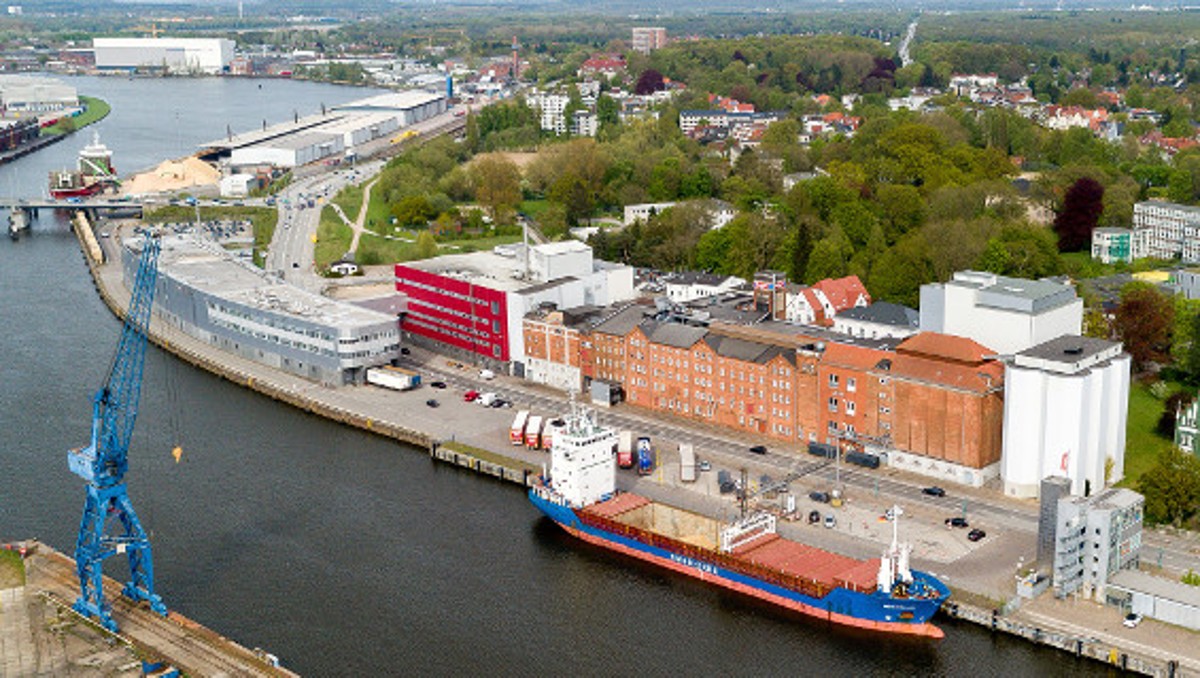
Fig. 1: The traditional company H. & J. Brüggen KG has had its headquarters at Lübeck port since 1886. Source: H. & J. Brüggen KG.
Enormous Energy Savings Thanks to Centralized Vacuum Supply for Packaging
H. & J. Brüggen KG
The production of muesli, granola bars, oatmeal flakes, and cereals is the core business of H. & J. Brüggen KG. In the ultra high-tech production facilities at its headquarters in Lübeck, Germany, the company applies a strict approach to energy management.
As part of the energy-saving initiative, the old vacuum supply for the wide range of packaging machines underwent a critical assessment. Working with a vacuum expert, the company switched from a decentralized to a centralized vacuum supply, which now supplies the vacuum required for all of the packaging machines. The new system consists of four demand-driven MINK MV Synchro claw vacuum pumps from Busch Vacuum Solutions. As a result of this switch, the company has achieved energy savings of 70 percent.
Vacuum technology in the manufacturing process
Alexander Boese is responsible for the energy management at the Lübeck-based production facilities for muesli, oatmeal flakes, and cereals. It was his decision to closely analyze the vacuum supply for the tubular bag machines, carton erectors, and tray packers. A total of 19 dry-running rotary vane vacuum pumps were installed on the respective packaging machines, consuming a total of 136,800 kilowatt hours per year. Because the company runs a three-shift operation for production and packaging, these vacuum pumps were generally in use all day and night for six days a week.
As part of the energy-saving initiative, the old vacuum supply for the wide range of packaging machines underwent a critical assessment. Working with a vacuum expert, the company switched from a decentralized to a centralized vacuum supply, which now supplies the vacuum required for all of the packaging machines. The new system consists of four demand-driven MINK MV Synchro claw vacuum pumps from Busch Vacuum Solutions. As a result of this switch, the company has achieved energy savings of 70 percent.
Vacuum technology in the manufacturing process
Alexander Boese is responsible for the energy management at the Lübeck-based production facilities for muesli, oatmeal flakes, and cereals. It was his decision to closely analyze the vacuum supply for the tubular bag machines, carton erectors, and tray packers. A total of 19 dry-running rotary vane vacuum pumps were installed on the respective packaging machines, consuming a total of 136,800 kilowatt hours per year. Because the company runs a three-shift operation for production and packaging, these vacuum pumps were generally in use all day and night for six days a week.-
Fig. 2: Partial view of the centralized vacuum supply at H. & J. Brüggen KG. Source: Busch Vacuum Solutions.
As soon as they were started up, these vacuum pumps began to exhibit additional benefits alongside significantly lower energy costs.
Alexander Boese explains that the drop in heat radiation and the MINK vacuum system's central setup meant that the air conditioning output could be reduced.
All of the packaging technology on the muesli production line was switched to MINK claw vacuum technology (Fig. 2) in early 2019. This means that the old setup of 19 decentralized rotary vane vacuum pumps was replaced by four MINK MV Synchro claw vacuum pumps. Alexander Boese measured and documented energy consumption continuously throughout the first half of the year. He then projected these figures to give him an annual consumption level. According to the calculations, the four vacuum pumps require a total of 38,580 kilowatt hours per year, generating an annual saving of 98,580 kilowatt hours (Fig. 3) compared to the power consumption of the old rotary vane vacuum pumps.
- First of all, the company was very impressed that noise levels had dropped a great deal compared to the old rotary vane vacuum pumps.
- What's more, the operating temperature is lower, decreasing heat radiation. This in turn has an impact on total energy consumption.
Alexander Boese explains that the drop in heat radiation and the MINK vacuum system's central setup meant that the air conditioning output could be reduced.
All of the packaging technology on the muesli production line was switched to MINK claw vacuum technology (Fig. 2) in early 2019. This means that the old setup of 19 decentralized rotary vane vacuum pumps was replaced by four MINK MV Synchro claw vacuum pumps. Alexander Boese measured and documented energy consumption continuously throughout the first half of the year. He then projected these figures to give him an annual consumption level. According to the calculations, the four vacuum pumps require a total of 38,580 kilowatt hours per year, generating an annual saving of 98,580 kilowatt hours (Fig. 3) compared to the power consumption of the old rotary vane vacuum pumps.
-
Fig. 3: Comparison of energy consumption before and after centralizing the vacuum supply. Source: Busch Vacuum Solutions.
The reason why the energy savings are so high is that the number of vacuum pumps was reduced significantly, that the vacuum pumps have been consolidated to create one vacuum system for the entire packaging area, and, last but not least, that the vacuum pumps are controlled based on demand. The old rotary vane vacuum pumps ran practically non-stop at full power on every machine, even if a packaging machine was switched off temporarily.
Consolidating the vacuum pumps to create a central vacuum system has resulted in an overall pumping speed that can vary. The reason behind this is that not all of the packaging machines always need the same pumping speed at the same time. In the case of the carton erectors, for instance, lots of "leak air" is generally sucked in when air is sucked through the cardboard or if one of the suction cups is not completely tight. The vacuum system immediately responds by increasing the rotational speed of one of the vacuum pumps or by activating an additional vacuum pump. As a result, the vacuum system's pumping speed increases. If one or more of the packaging machines come to a standstill, the vacuum system automatically reduces its pumping speed. As such, the system only consumes as much energy as is actually needed for the output.
In the old rotary vane vacuum pumps, the carbon blades had to be checked on a regular basis and replaced when worn, a process that could only take place if the packaging machine was switched off. MINK claw vacuum pumps have a contact-free operating principle, which means that the moving parts inside the vacuum pump (Fig. 4) do not come in contact with each other. This means that there is no wear or friction, which for models with carbon blades causes fine dust to collect around the vacuum pump.
Experience with the Mink MV Synchro vacuum pumps
Following their first few months of use, Jan Brakow also noticed that the four MINK MV Synchro vacuum pumps required "practically zero maintenance." The only regular jobs are therefore removing dust from the inlet filters or replacing them if they are very dirty. Otherwise, maintenance is limited to the annual change of gear oil. This can be performed while production is running – by temporarily disconnecting one of the four vacuum pumps from the supply network, which automatically increases the output of the three remaining vacuum pumps.In the old rotary vane vacuum pumps, the carbon blades had to be checked on a regular basis and replaced when worn, a process that could only take place if the packaging machine was switched off. MINK claw vacuum pumps have a contact-free operating principle, which means that the moving parts inside the vacuum pump (Fig. 4) do not come in contact with each other. This means that there is no wear or friction, which for models with carbon blades causes fine dust to collect around the vacuum pump.
Alexander Boese and Jan Brakow are very pleased after over a year's worth of experience with the MINK claw vacuum pumps, which has resulted in energy savings, minimized maintenance work and costs, and very importantly an increase in reliability. The plans to expand production and to purchase more packaging machines now also involve plans to expand the vacuum supply with MINK claw vacuum pumps.
-
Fig. 4: Cutaway drawing of a dry and contact-free compressing MINK claw vacuum pump from Busch Vacuum Solutions. Source: Busch Vacuum Solutions.