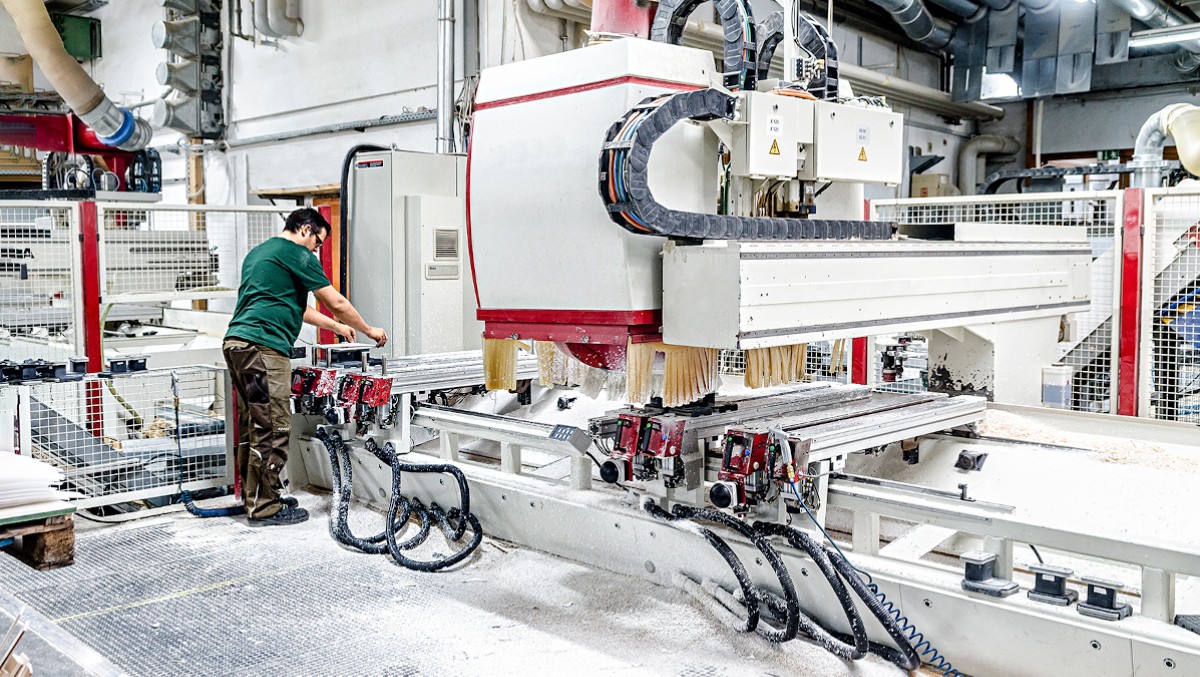
Fig. 1: One of 14 CNC routers at Holzbearbeitung Kraus. Source: Holzbearbeitung Kraus GmbH.
Energy Savings Thanks to the Right Choice of Vacuum Supply
Holzbearbeitung Kraus GmbH
To produce components for caravans and motor homes, as well as facility furnishings, the woodworking company Holzbearbeitung Kraus GmbH uses a total of 14 different CNC routers. Each of the routers was equipped with two rotary vane vacuum pumps which, all together, generated annual energy consumption of over 300,000 kilowatt hours. CEO Karl Fritz Kraus found this to be an unnecessary waste of energy. So, he sought alternative vacuum generation for clamping. He found it in a central vacuum supply from Busch Vacuum Solutions.
About Holzbearbeitung Kraus
With its 120 employees, Holzbearbeitung Kraus produces components for many caravan and motor home manufacturers, as well as countertops for kitchen units, washbasin covers, tabletops and much more. The company also focuses on facility furnishings, for which it manufactures complete systems for retirement homes, doctors' offices, office buildings, banks, and kindergartens. Kraus offers services from interior design and planning to construction, manufacturing, and installation – all from a single source.
Vacuum clamping of workpieces on CNC routers
At the plant in Zusamzell near Augsburg, Germany, 14 different CNC routers are busy with production. All of the machines work with consoles and vacuum blocks for clamping (fig. 1). CEO Karl Fritz Kraus thought it was horrible to see all these machines equipped with two dry-running rotary vane vacuum pumps, each running practically constantly during operation, even when nothing was being clamped. With two vacuum pumps per CNC router and average power consumption of 3 kilowatts during two-shift operation, the resulting energy requirement was over 300,000 kilowatt hours per year. Furthermore, the rotary vane vacuum pumps required quite extensive maintenance. For example, the graphite lamellae needed to be exchanged in one of the vacuum pumps every two weeks, on average. This led to downtime and generated high costs.
Energy-efficient Busch solution to generate vacuum for clamping
For this reason, Karl Fritz Kraus began searching for a more energy-efficient solution to generate vacuum for clamping, which led him to contact Busch Vacuum Solutions in 2018. The company offered him a demand-driven central vacuum supply consisting of several MINK claw vacuum pumps. Thanks to cascade control, only the vacuum pumps needed to maintain vacuum for clamping at all CNC routers are in operation. In the beginning, Kraus was skeptical as to whether this could work. The team feared that all 14 routers would be affected if the central vacuum system failed. So they chose a vacuum supply with three MINK claw vacuum pumps to supply five routers with vacuum. These three claw vacuum pumps replaced a total of ten of the previously used rotary vane vacuum pumps. The three MINK vacuum pumps were each equipped with 5.5 kW motors. They therefore require 16.5 kW at full output. Compared with the previously used ten rotary vane vacuum pumps with 3 kW each or a total of 30 kilowatts, this provided energy savings of 45 percent in purely mathematical terms.Thanks to the demand-driven control system, all three vacuum pumps were rarely in operation, which also led to significant energy savings. The initial skepticism regarding the operational reliability quickly dissipated. If one vacuum pump had failed due to a malfunction, both of the remaining pumps would have been able to supply sufficient output to maintain the vacuum level at each CNC machine. They were so convinced that they expanded the central vacuum supply, in two subsequent stages, to connect all 14 CNC routers. Now a total of eight MINK claw vacuum pumps are installed in the plant. Four to six of them are running during normal operation. This means there is enough redundancy and even reserves to connect an additional CNC router. If we assume that six MINK claw vacuum pumps operate constantly, the energy savings would be equivalent to over 60 percent (fig. 2).
-
Fig. 2: Comparison of energy consumption before and after switching to a central vacuum supply. Source: Busch Vacuum Solutions.
The central vacuum supply consists of racks, each with three or two MINK claw vacuum pumps (fig. 3).
-
Fig. 3: Rack with three MINK claw vacuum pumps. Source: Busch Vacuum Solutions.
It is installed in the production facility and completely enclosed (fig. 4).
-
Fig. 4: Completely enclosed central vacuum supply at Holzbearbeitung Kraus. Source: Busch Vacuum Solutions.
This eliminated both heat and noise emissions to the greatest extent possible. The staff found the noise level of the previously used rotary vane vacuum pumps particularly strenuous. CEO Karl Fritz Kraus is convinced that he found the ideal solution for his operations through centralization of vacuum supply and using MINK claw vacuum technology. Because in addition to the huge energy savings, the maintenance costs have also been reduced. Maintaining the new vacuum system is limited to an annual inspection and an oil change performed by a Busch service technician. This maintenance work can be performed during operation. Because MINK claw vacuum pumps use IE3 energy-saving motors, the company was also able to receive financial support from the German Federal Office of Economics and Export Control (BAFA).