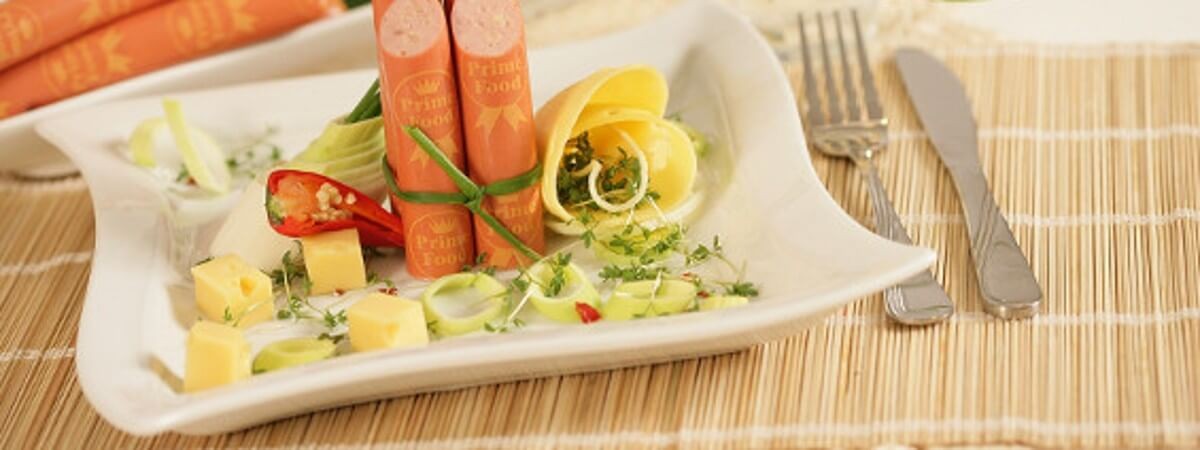
Fig. 1: Various sausage and meat products are Goodvalley Polka's speciality. Source: Goodvalley Polska.
Efficiency and Energy Savings Achieved in Food Packaging with a Central Vacuum Supply
Goodvalley Polska
As one of the largest pork processors in Poland, Goodvalley Polska manufactures various types of sausages, ham and fresh meat products. All sausage goods are packed in a user-friendly manner using modified atmosphere packaging (MAP).
The vacuum used to evacuate the air from the packaging is provided by a central vacuum system from Busch. It supplies all packaging lines with the required vacuum before the packaging is flooded with protective atmosphere. Using this central vacuum supply unit, Goodvalley Polska was able to achieve optimum economic efficiency and effectiveness.
The vacuum used to evacuate the air from the packaging is provided by a central vacuum system from Busch. It supplies all packaging lines with the required vacuum before the packaging is flooded with protective atmosphere. Using this central vacuum supply unit, Goodvalley Polska was able to achieve optimum economic efficiency and effectiveness.
Product packaging
Goodvalley Polska uses protective atmosphere, a gas mixture of carbon dioxide and nitrogen, to package its products. This generates an equalizing atmosphere in packaging, which dramatically increases the shelf life of products and ensures that the colour, consistency and freshness of the products is maintained throughout the entire storage period.Goodvalley Polska
Goodvalley Polska combines all process steps at their site in Przechlewo, from slaughter to shipping the finished products. Every day, 1,000 pigs are slaughtered. All of the animals come from the company's own pig breeding farm, Poldanor SA, just a few kilometres away. They can thus influence the quality of the meat during the breeding process. Both Goodvalley Polska and Poldanor SA belong to the international Axzon Group.Goodvalley Polska employs 900 shift workers for processing operations. Production runs 20 hours per day. Afterwards, the processing machines and systems are cleaned.
-
Fig. 2: Packaging ground meat with a tray sealer packaging machine. Source: Busch Vacuum Solutions.
Packing process
Protective atmosphere is used for the packaging process on a total of four packaging lines, which are each equipped with tray sealer packaging machines. Individual R5 rotary vane vacuum pumps from Busch were originally installed for each packaging machine, one floor directly above each machine. According to the Technical Director of Goodvalley Polska, Tomasz Paciorek, this decision was made to keep waste heat from the vacuum pumps from entering the processing and packaging rooms.Vacuum system from Busch
At the end of 2015, Busch Vacuum Solutions made Goodvalley Polska an offer to centralize the vacuum supply for all four packaging lines.This would provide the following benefits:
- Energy savings
- Absolute vacuum supply reliability
- Ability to perform maintenance work while the system is in operation
In the end, Tomasz Paciorek decided to use one such vacuum system from Busch. It was installed at the beginning of 2016 and has since been running in cycles of 20 hours, five or six days per week.
The system is made up of a total of four R5 rotary vane vacuum pumps. They are connected to a vacuum container, where they maintain a constant vacuum of 150 millibars. A maximum of three of the four vacuum pumps are needed to do this. One of the vacuum pumps functions purely as a stand-by. Even under full load, the system only uses three instead of the previously required four vacuum pumps, which is equivalent to annual energy savings of approximately 3,750 kilowatt hours.
The vacuum system operates according to demand, meaning that the only R5 rotary vane vacuum pumps in operation are the ones that are actually needed for operation.
-
Fig. 3: Centralized vacuum system from Busch for generating the vacuum in packaging trays before flooding them with protective gas. Source: Busch Vacuum Solutions.
R5 rotary vane vacuum pump
R5 rotary vane vacuum pumps from Busch are extremely robust so there has never been a failure, whether with the previous individual set-up or the new centralized vacuum system. Even if one of the vacuum pumps were to fail, there would be no interruption of operations whatsoever thanks to redundant operation of the four vacuum pumps. The upstream vacuum vessel provides a permanent vacuum of 150 millibars. This guarantees the fastest evacuation times and thus fastest clock cycles during packaging.Maintenance
The central vacuum supply unit's design also makes it possible to perform maintenance work during operation. Maintenance personnel do not have to enter the hygienically sensitive area to do this. Instead, they go to the engineering room on the upper floor where the system is located. During maintenance work, each individual R5 rotary vane vacuum pump can be switched off without affecting the vacuum level or the pumping speed.Packaging process with oxygen
All installed vacuum pumps are specially designed to handle oxygen and can safely compress oxygen contents in excess of 21 percent. This makes it possible to add gas mixtures with an oxygen content of approximately 70 percent to MAP packaging using the vacuum chamber. This high concentration of oxygen makes the gas mixtures explosive.During the normal packaging process, the packaging chamber is ventilated after being flooded with the gas mixture so that only normal air is removed during the next packaging cycle, thus preventing danger of an explosion. Only the improbable case of a defective valve or other damage could lead to an increased concentration of oxygen entering the vacuum pumps when it is pumped out.
This is why the versions of the installed R5 rotary vane vacuum pumps meet the highest safety requirements, so that they can also safely remove even increased concentrations of oxygen.
Future benefits
Technical Director Tomasz Paciorek is very satisfied with this solution.A further benefit of centralizing the vacuum supply will be demonstrated in 2017, when a fifth packaging line will begin operation. It can be connected to the central vacuum supply unit without requiring expansion of the unit. The vacuum specialists from Busch have already calculated that the current system performance is sufficient to safely supply an additional packaging line with vacuum.
This increases the energy savings even further when compared to the original individual supply of the packaging machines.