Les batteries lithium-ion sont au cœur de l'électromobilité. Les processus clés de leur fabrication sont réalisés sous vide. BUSCH dispose des pompes à vide appropriées pour diverses contraintes.
Le lithium (Li) est le plus léger des éléments solides et ses ions chargés électriquement se déplacent extrêmement facilement. Les batteries Li-ion - celles des voitures étant rechargeables - peuvent stocker plus de charge par unité de masse que les autres types de batteries. Cela en fait non seulement la source d'énergie idéale pour les smartphones et les tablettes, mais aussi pour les voitures électriques. Ce sont actuellement les seules batteries qui permettent des autonomies raisonnables.
Pâte sans poches d'air
L'intérieur des batteries est constitué de feuilles d'électrodes recouvertes d'une pâte de lithium (slurry). Les matières premières du mélange sont brassées dans un mélangeur. Le résultat doit être une masse homogène sans poches d'air. Pour éliminer les éventuelles poches d'air, du vide est appliqué dans le mélangeur.
Après avoir répandu le mélange, les électrodes enduites doivent sécher. De l'humidité dans les cellules de la batterie entraînerait une perte de performance et un vieillissement prématuré. Le séchage sous vide garantit que toute humidité résiduelle est réduite au minimum de manière très efficace.
Remplissage et formation de l'électrolyte
Les ions se déplacent entre les électrodes grâce à un matériau conducteur : les électrolytes. Les électrolytes liquides sont appliqués à l'aide d'une lance d'injection. Au cours de ce processus, un profil de pression défini est utilisé pour alterner entre l'évacuation et le rinçage avec un gaz de protection inerte de manière à répartir uniformément la masse dans toute la cellule. L'humidification des électrodes pour améliorer le flux de courant est également amélioré par cette méthode.
Pendant le processus de formation, les cellules de la batterie sont chargées électriquement pour la première fois. Cela libère des gaz qui peuvent être à la fois toxiques et explosifs. Ils sont donc aspirés à l'aide de pompes à vide.
Enfin, le processus de contrôle qualité permet de vérifier l'étanchéité des cellules. S'il y a une fuite, la solution d'électrolyte qui s'évapore sous vide s'échappe et peut être facilement détectée. BUSCH identifie la solution idéale pour les diverses exigences de la technologie du vide auxquelles chaque application individuelle doit répondre.
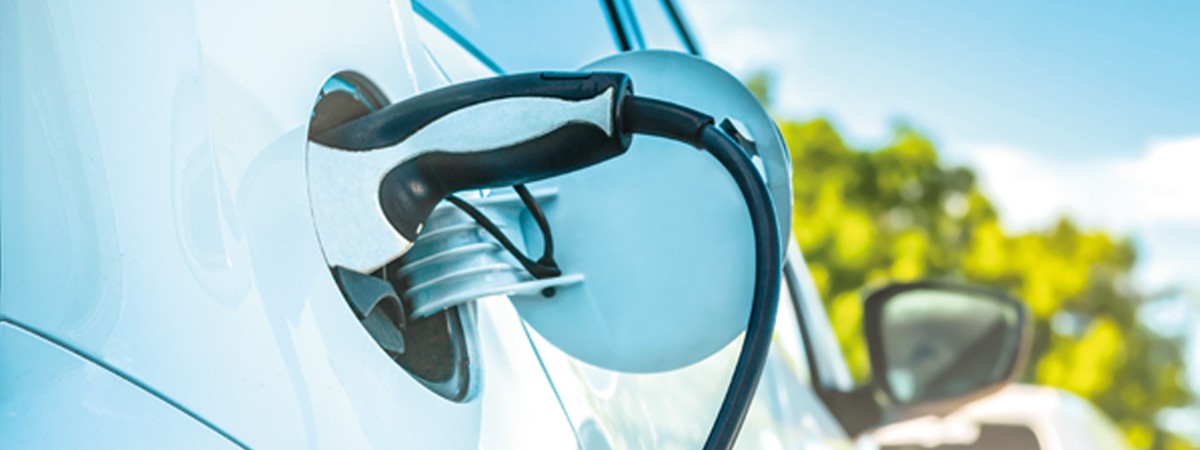
Le vide est essentiel à l'électromobilité
Nombreuses applications dans la production de batteries
Plus fine qu'un cheveu
Les électrodes d'une batterie Li-ion sont constituées de films extrêmement fins. Dans les batteries, le lithium est utilisé comme anode et les batteries rechargeables utilisent l'oxyde métallique de lithium comme cathode. L'oxyde est mélangé à un agent liant et à d'autres matériaux supplémentaires pour former une pâte homogène (slurry). Cette dernière est appliquée uniformément sur la feuille d'aluminium dans la machine à enduire. Ce processus est similaire à une impression avec une imprimante à jet d'encre. L'aluminium est le substrat et sert de conducteur absorbant le courant de charge et émettant à nouveau l'électricité stockée. Après le processus de revêtement, un système de rouleaux transporte le film tout en le pressant à plat jusqu'à ce que les feuilles individuelles deviennent plus fines qu'un cheveu. Plus le revêtement est épais et plus le film d'électrode est fin, plus la capacité de la batterie est élevée.
Les électrodes d'une batterie Li-ion sont constituées de films extrêmement fins. Dans les batteries, le lithium est utilisé comme anode et les batteries rechargeables utilisent l'oxyde métallique de lithium comme cathode. L'oxyde est mélangé à un agent liant et à d'autres matériaux supplémentaires pour former une pâte homogène (slurry). Cette dernière est appliquée uniformément sur la feuille d'aluminium dans la machine à enduire. Ce processus est similaire à une impression avec une imprimante à jet d'encre. L'aluminium est le substrat et sert de conducteur absorbant le courant de charge et émettant à nouveau l'électricité stockée. Après le processus de revêtement, un système de rouleaux transporte le film tout en le pressant à plat jusqu'à ce que les feuilles individuelles deviennent plus fines qu'un cheveu. Plus le revêtement est épais et plus le film d'électrode est fin, plus la capacité de la batterie est élevée.