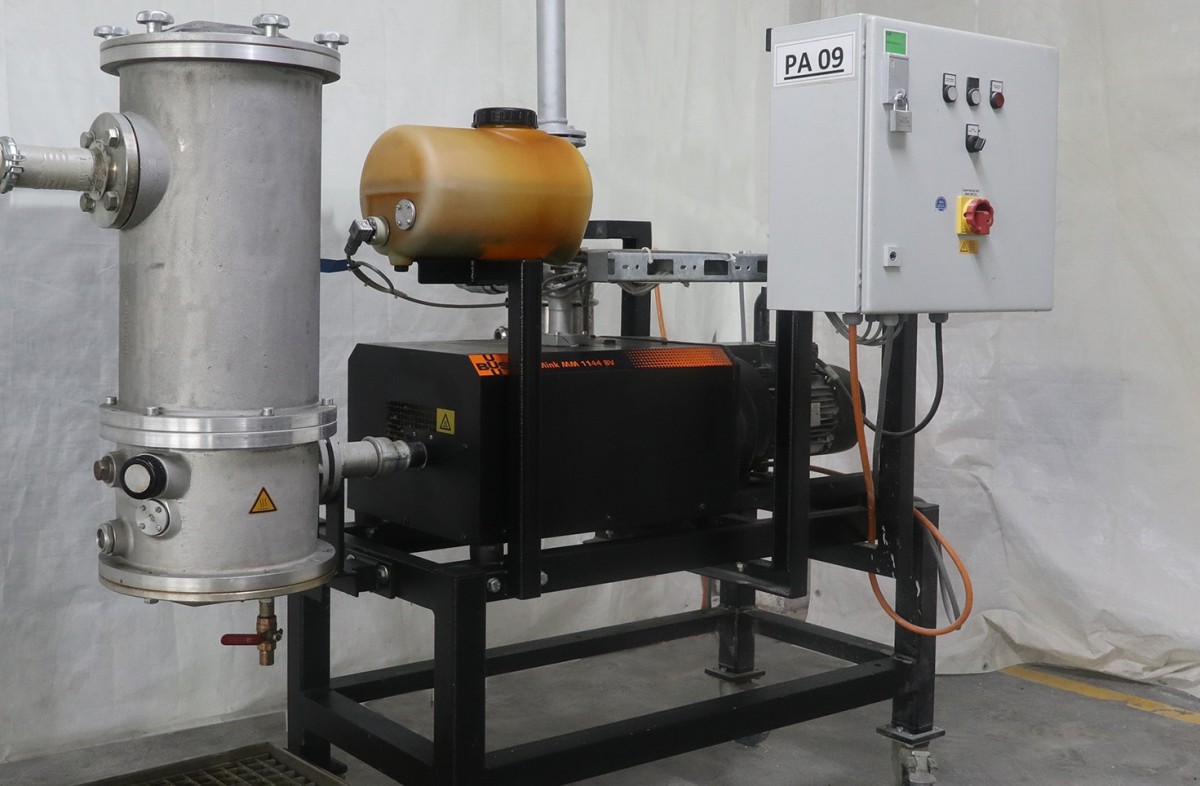
Moderne vacuümtechnologie voor ontgassing van gesmolten massa's tijdens extrusie
Als samenstellingsspecialist van kunststoffen is het bedrijf PolyComp GmbH zowel een contractuele producent als een gelicentieerde producent van complexe samengestelde kunststoffen. Haar producten variëren van uiterst sterke technische thermoplastics en kunststoffen die tegen een hoge temperatuur bestendig zijn tot zachte flexibele thermoplastische elastomeren, die op verzoek worden gecombineerd met een groot aantal verschillende additieven. Het uitgebreide productportfolio vereist flexibele productiefaciliteiten, die bestaan uit verschillende extruders en enkele speciale schroefconfiguraties.
Er is echter één constante in alle extruders: voor de afzuiging van dampen en gassen uit het gesmolten materiaal in de schroefsecties vertrouwt PolyComp uitsluitend op PLASTEX ontgassingssystemen van Busch Vacuum Solutions. Deze systemen zijn uitgerust met MINK klauwenvacuümpompen en zijn uitzonderlijk betrouwbaar en eenvoudig in het onderhoud.
Er is echter één constante in alle extruders: voor de afzuiging van dampen en gassen uit het gesmolten materiaal in de schroefsecties vertrouwt PolyComp uitsluitend op PLASTEX ontgassingssystemen van Busch Vacuum Solutions. Deze systemen zijn uitgerust met MINK klauwenvacuümpompen en zijn uitzonderlijk betrouwbaar en eenvoudig in het onderhoud.
-
Afb. 1: Eén van in totaal zeven PLASTEX ontgassingssystemen bij PolyComp. Ze zijn een verdieping hoger boven de extruders geïnstalleerd.
Over PolyComp
PolyComp werd opgericht als een managementbuy-out in 2000 en het hoofdkantoor bevindt zich in Norderstedt, in het randgebied van Hamburg, Duitsland. In 2013 werd PolyComp overgenomen door de in Hamburg gevestigde Feddersen Group, die zich richt op de wereldwijde handel van chemische en technische producten.De hoofdactiviteiten van PolyComp bestaan uit het samenstellen van polyolefinen (PP/PE), alsook EVA, PA, PBT, PC, ABS, EVOH, POM en PMMA. Deze verbindingen worden gemengd met verschillende additieven, die uiteenlopen van koolstof- of natuurlijke vezels en eenvoudige vullers tot glaskorrels, kleuradditieven of wassoorten.
Foliesamenstellingen
Een van de specialiteiten van PolyComp is foliesamenstellingen, waarvoor uiterst kleine hoeveelheden gel nodig zijn. Het productieproces omvat een extrusiefase, waarin specifieke schroefconfiguraties worden gebruikt en een schermfilter wordt toegepast met een hoge filterprecisie. Het bedrijf gebruikt in totaal acht enkele of dubbele schroefextruders. Het gesmolten materiaal wordt ontgast in zes van de extruders. Tot 2009 gebruikte het bedrijf vloeistofringvacuümpompen voor dit proces.De verwijdering van het gebruikte water werd steeds problematischer, omdat gassen en dampen werden vermengd met het water en condensaat. De kosten van behandeling of afvoer van het water werden alsmaar hoger.
Henning von Brühl, assistent-productiemanager, voegt hier aan toe: "We konden nooit nauwkeurig voorspellen welke soort stoffen in het water terechtkwamen. Het ging niet alleen om gassen, dampen en polymeren van de basisingrediënten, ook delen van de additieven kwamen terecht in de bedrijfsvloeistof van de vacuümpompen." Dit was het gevolg van de frequente productwijzigingen. Zelfs als de basisingrediënten hetzelfde bleven, konden de verschillende gebruikte additieven de samenstelling van chemische stoffen in het water wijzigen. Aangezien PolyComp vijf dagen per week draait met een drieploegendienst, werden er grote hoeveelheden water verzameld voor behandeling.
Onze oplossing
Tijdens de zoektocht naar een milieuvriendelijke oplossing in 2009 kwam het bedrijf in contact met Busch, die een PASTEX ontgassingssysteem voorstelde (afb. 1), waarvoor geen bedrijfsvloeistoffen nodig zijn. Het systeem bestaat voornamelijk uit een MINK klauwenvacuümpomp (afb. 2) en een upstream standfilter en fijn filter. De filters worden gebruikt om condensaten en vaste deeltjes te scheiden. MINK klauwenvacuümpompen hebben geen bedrijfsvloeistoffen nodig, zoals water of olie. Dit betekent dat de verpompte dampen en gassen niet in contact komen met bedrijfsvloeistoffen, waarmee ze zouden kunnen mengen of reageren. Zelfs de veiligste afscheidertechniek kan echter niet altijd voorkomen dat achtergebleven monomeren in de pompen terechtkomen en daar breken. Om deze reden is de MINK klauwenvacuümpomp voorzien van een spoelinrichting. Hiermee kan een nauwkeurig gedoseerde hoeveelheid spoelvloeistof in de vacuümpomp gevoerd worden op gedefinieerde intervallen, wat helpt bij het oplossen van restdeeltjes. Onderhoudsmanager Stefan Stolp heeft de hoeveelheid spoelvloeistof en de spoelintervallen voor alle materialen bepaald die geëxtruseerd worden. Het spoelproces kan plaatsvinden tijdens perioden van stilstand of zelfs bij lopende productie.-
Afb. 2: MINK klauwenvacuümpompen vormen het hart van PLASTEX ontgassingssystemen. Dankzij hun contactvrije werkingsprincipe hebben ze geen bedrijfsvloeistoffen nodig, zoals water of olie.
Na aankoop van haar eerste PLASTEX ontgassingssystemen heeft PolyComp geleidelijk al haar vloeistofringvacuümpompen vervangen. Stefan Stolp is zeer tevreden met de oplossing. Ten eerste heeft het zijn probleem met afvalwater opgelost en ten tweede zijn de PLASTEX ontgassingssystemen volledig betrouwbaar en vereisen ze weinig onderhoudsinspanning. De filters moeten regelmatig worden gereinigd en het spoelmiddel moet naar behoefte worden aangevuld. De intervallen tussen aanvullingen variëren afhankelijk van het verwerkte materiaal. Deze werkzaamheden worden rechtstreeks uitgevoerd door leden van het productieteam. Het onderhoudsteam ontmantelt en reinigt elke vacuümpomp na gemiddeld 10 maanden. "Al met al is de hoeveelheid werk goed te doen, vergeleken met wat we moesten doen met de oude vloeistofringvacuümpompen", zegt Henning von Brühl.
Ingenieur Simone Patermann heeft nog een voordeel van de toepassing van PLASTEX ontgassingssystemen geïdentificeerd. Als hoofd van productie let zij altijd op energieverbruik, niet op zijn minst omdat PolyComp is gecertificeerd onder ISO 50001 voor energiebeheersystemen.
Dit komt door twee factoren. Allereerst is er door het feit dat er geen bedrijfsvloeistoffen worden gebruikt, geen behoefte meer aan energie om deze vloeistoffen te verplaatsen. Ten tweede zijn MINK klauwenvacuümpompen volledig contactvrij. Als gevolg hiervan zijn er geen componenten die tegen elkaar wrijven en er is geen kracht nodig om deze wrijving te overwinnen.
In 2018 startte PolyComp een nieuwe extrusielijn, met als middenpunt een dubbele schroefextruder met een uitvoer tot 1.500 kilo per uur. Door de twee zijdoseerunits (afb. 3) kunnen verschillende soorten poedervormige vulmaterialen tegelijkertijd worden toegevoegd en worden gemengd met een hoge uitvoercapaciteit. Eén zijdoseerunit kan op een PLASTEX ontgassingssysteem worden aangesloten. Dit vermindert het volume van het vulmateriaal en kan de bulkdichtheid verdrievoudigen vergeleken met een zijdoseerunit zonder ontgassing. Dit zorgt voor een aanzienlijke toename van het totale uitvoervermogen.
Ingenieur Simone Patermann heeft nog een voordeel van de toepassing van PLASTEX ontgassingssystemen geïdentificeerd. Als hoofd van productie let zij altijd op energieverbruik, niet op zijn minst omdat PolyComp is gecertificeerd onder ISO 50001 voor energiebeheersystemen.
MINK klauwenvacuümpompen hebben de hoogste efficiëntiefactor van alle mechanische vacuümpompen. Dit betekent dat hun energieverbruik altijd lager is vergeleken met andere mechanische vacuümpompen met dezelfde prestaties.
In 2018 startte PolyComp een nieuwe extrusielijn, met als middenpunt een dubbele schroefextruder met een uitvoer tot 1.500 kilo per uur. Door de twee zijdoseerunits (afb. 3) kunnen verschillende soorten poedervormige vulmaterialen tegelijkertijd worden toegevoegd en worden gemengd met een hoge uitvoercapaciteit. Eén zijdoseerunit kan op een PLASTEX ontgassingssysteem worden aangesloten. Dit vermindert het volume van het vulmateriaal en kan de bulkdichtheid verdrievoudigen vergeleken met een zijdoseerunit zonder ontgassing. Dit zorgt voor een aanzienlijke toename van het totale uitvoervermogen.
-
Afb. 3: De twee zijdoseerunits op de dubbele schroefextruder. Een PLASTEX ontgassingssysteem helpt het volume te verminderen bij het toevoegen van vulmateriaal. Bron: PolyComp
Het managementteam van PolyComp bevestigt dat ze – als het gaat om betrouwbaarheid, onderhoudsinspanning en economisch rendement – de juiste keuze hebben gemaakt met het PLASTEX ontgassingssysteem van Busch. De hoge mate van betrouwbaarheid heeft een positief effect op de productie. Downtime door storingen of last-minute reparatie- of reinigingswerkzaamheden – zoals vaak het geval was met de vloeistofringvacuümpompen – is nu verleden tijd.