The company exclusively uses Busch R5 rotary vane vacuum pumps for its superb sailing boats.
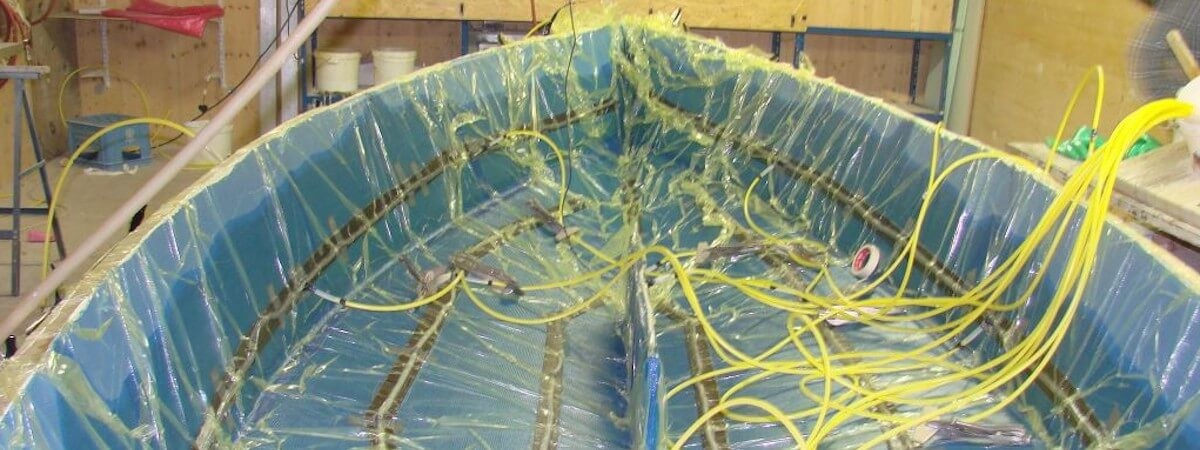
Fig. 1: Boat hull mould during resin infusion. Source: Mader shipyard.
Quality Resin Infusion Processes in Boatbuilding with R5 Rotary Vane Vacuum Pumps
Mader shipyard
Over 100 world championship titles, numerous Olympic medals and countless national championships have been won with their regatta boats:
For Leonhard Mader junior and his son Andreas from the Mader shipyard in Waging am See, it’s completely normal for their customers to regularly make it to the top of the winners’ podium with sailing boats from their own shipyard. This is because the Waging Olympic, international and national regatta boats mean excellent quality and customized fittings for each regatta racer. When generating the vacuum for resin infusion in the production of GRP parts for the boats, Mader itself also focuses on quality: The company exclusively uses Busch R5 rotary vane vacuum pumps for its superb sailing boats.
About Mader shipyard
Mader was founded as a joinery by Leonhard Mader senior in 1952. Two years later, the first wooden boats were produced. In 1956 Leonhard Mader used vacuum for form-gluing wooden parts for the first time, and these were used to create his first “Flying Dutchman”. Mader built his first boat completely out of synthetic material in 1962; this was also a “Flying Dutchman”, made of glass fabric and epoxy resin. The Mader shipyard made its major breakthrough with the 1972 Olympic Games in Munich, or more specifically the sailing competitions in the Kiel Fjord – the boats for all participants in the Finn Dinghy class were made and supplied by Mader. The 1976 Olympic sailing competitions in Kingston, Canada, caused a major stir: All participants in the Tempest class sailed on Mader boats, and only the British favourites used a different vessel. Out of frustration from only coming in 14th, the two Britons set their boat on fire in the middle of the lake, and sank it. Today, Mader focuses only on building international- and national-class boats, and produces around 15 to 20 regatta boats per year on request from sailors all over the world. The company caters to its customers’ individual preferences whilst always complying with the strict regulations. The shipyard’s other mainstays are building motorboats and providing boat repairs. The shipyard has been run by Leonhard Mader junior and his son Andreas since 2003.Resin infusion in sailing boat manufacture
All the boats feature a hull and inner shell made of fibreglass-reinforced plastic, and the resins used are predominantly vinyl ester or epoxy resin.
For Mader, it was essential that only a Busch R5 rotary vane vacuum pump would be used for vacuum generation.
-
Fig. 2: R5 rotary vane vacuum pump to evacuate the mould and infuse the resin. Source: Busch Vacuum Solutions.
Vacuum solution and its benefits for resin infusion in sailing boat production
R5 rotary vane vacuum pumps are used in a wide range of industrial applications. In resin infusion processes, it is not only important that they reach a vacuum level of 0.1 millibars on an ongoing basis, corresponding to a vacuum of 99.99 percent, but also that sufficiently high pumping speed is still generated with high vacuum performance. After all, even when very precisely sealing the synthetic core using foil, a leak may result in the permeation of small quantities of air, which then need to be immediately extracted again using the vacuum pump.
High vacuum performance ensures fast, bubble-free and complete resin infusion.
Mader has been using Busch R5 vacuum pumps for decades. There has not yet been a single fault, or any downtime.
Maintenance is limited to an annual oil change. At the Mader shipyard, this is organized by phone and carried out by a Busch service technician. As a result, a safe vacuum supply is also guaranteed at the shipyard for the future, and Leonhard Mader junior and Andreas Mader are sure to build many more sailing boats for future international and national champions.