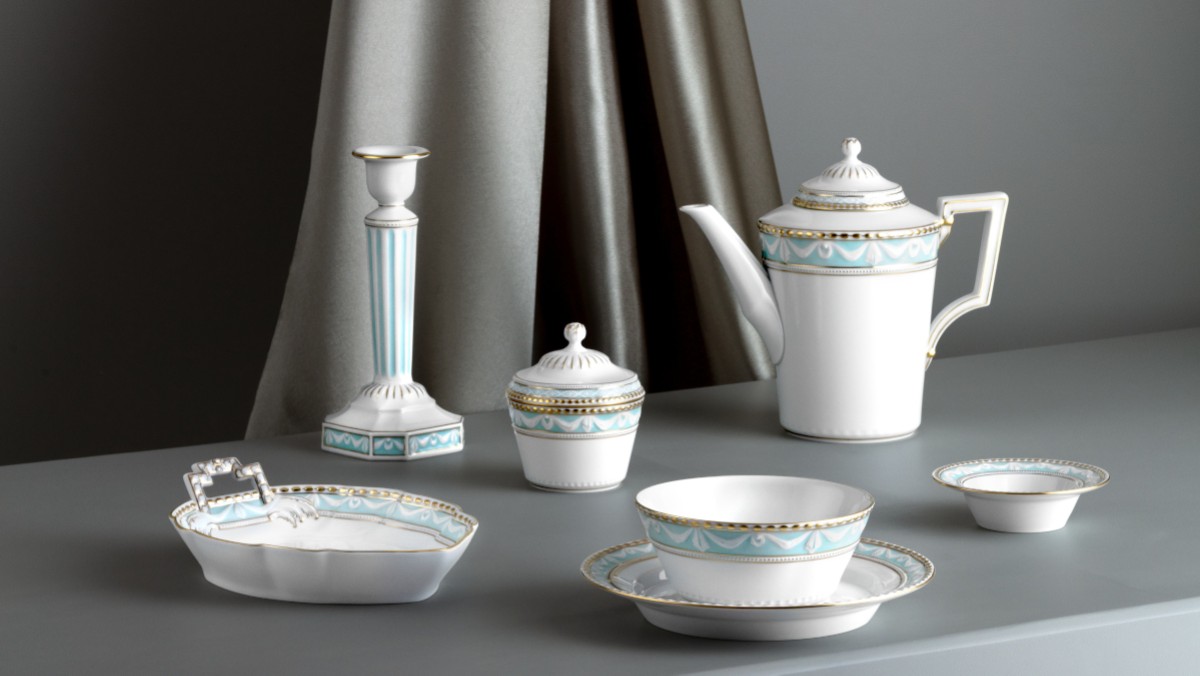
The Königliche Porzellan-Manufaktur in Berlin has been producing tableware, decorative porcelain and porcelain art since 1763. Source: KPM Berlin.
No High-Quality Porcelain Without Vacuum.
KPM Königliche Porzellan-Manufaktur Berlin GmbH | KPM Royal Porcelain Factory Berlin GmbH
Three ingredients for endless creativity
The traditional recipe for porcelain consists of half kaolin and a quarter of feldspar and quartz. These raw materials are supplied pre-ground in large white bags, mainly from mines in Bavaria and Saxony. Today, the factory's 180 employees process 150 tons of these materials into 200,000 individual products a year – from espresso cups to floor vases.
-
Two R5 rotary vane vacuum pumps from Busch ensure the correct vacuum level for degassing the porcelain before further processing. Source: Busch Vacuum Solutions.
The raw materials that make up the final product initially have nothing in common with the shiny end result. Of the three powders, kaolin is first dissolved in water. Once mixed, it has a buttermilk-like consistency that thickens slightly and absorbs the other two ingredients, feldspar and quartz. An agitator keeps everything moving and ensures a homogeneous mixture. Permanent magnets and fine sieves ensure that any unwanted particles do not cause unpleasant brown stains or pockmarks in the porcelain.
Constant vacuum for consistent quality
To further process the porcelain mixture, part of the water must now be removed. This is done in large filter presses. Here, the paths split between thrown porcelain, such as plates and cups, or slip-cast pieces, such as vases, jugs or figurines. For thrown goods, the paste is allowed to have a residual moisture content of 21-25%. The filter cake is transported to a two-stage screw extruder via a conveyor belt. Stage one presses the moist paste through punched sheet metal, creating thin, pasta-like strands – just like a meat grinder. These then fall into a vacuum chamber. Here, all air pockets are removed from the paste at a vacuum level of 20 hPa (mbar). Otherwise, when the porcelain is fired, these would expand and cause unsightly pockmarks or even cause the valuable pieces to burst.
-
One of the three screw extruders that KPM uses to degas the porcelain paste. Source: Busch Vacuum Solutions.
In the more fluid porcelain paste for slip-cast pieces, the air bubbles can escape with slight movements alone, something that is no longer possible with the more solid paste used for throwing. Vacuum from Busch has to provide support. The deaerated strands are pressed by a second screw through a conical mouthpiece into an endless strand. Its diameter depends on the size of the piece to be thrown – the smallest is used for an espresso cup, the largest for a dinner plate. A third vacuum pump on a separate extruder degasses special pastes for hand-thrown products such as large baskets.
No air bubbles in the kiln
The strands from the extruder are cut into 40 cm long slabs and stored in a damp room under tarpaulins. Just like in a greenhouse, a warm humid mist hangs in the air. They remain here for a few days until an employee picks them up and turns them into beautiful plates, cups, or bowls using traditional craftsmanship on a pottery wheel or with machine assistance.
-
The porcelain slabs are stored in a “maukraum” (mauk-room) or aging room before being thrown by hand to create plates, cups and bowls. Source: Busch Vacuum Solutions.
-
Bowls with the Kurland design wait for glazing and firing after they are thrown. Source: Busch Vacuum Solutions.