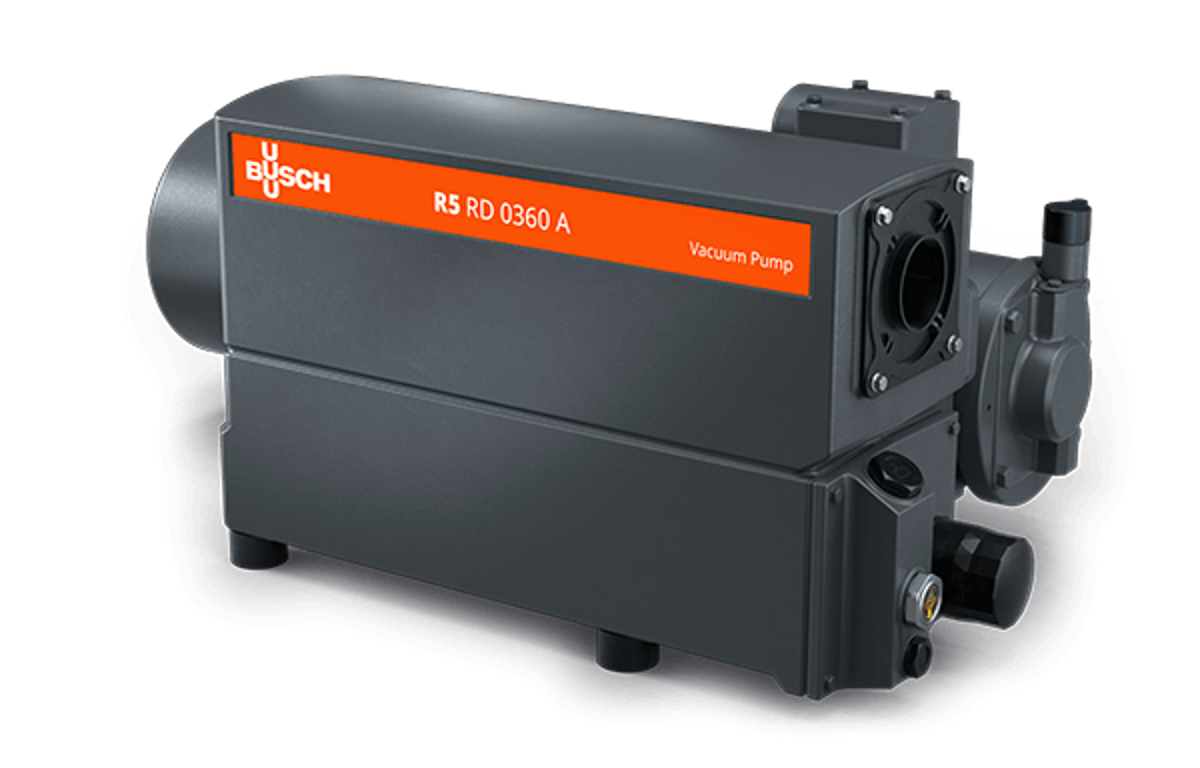
Fig. 1: The R5 RD 0360 A rotary vane vacuum pump is one size of the newest generation of vacuum pumps for packaging. Source: Busch Vacuum Solutions.
Energy-Efficient Vacuum Supply for Meat-Processing Plants
Hygienic packaging of meat and sausage products
An integrated packaging concept that guarantees that finished products are packaged hygienically, reliably, swiftly and efficiently is an important component in modern production of meat and sausage products.
This is why innovative meat-processing plants are continuously working to optimize their production processes and integrate their packaging lines into the overall process in the best possible manner. The correct selection of vacuum generation systems substantially influences the operational reliability and economic efficiency of the packaging process. Depending on the size of the plant and the production quantities involved, there are a number of vacuum supply options. These alternatives are explained below and food for thought given in order to find the best possible solution as regards technology and cost-effectiveness.
The correct selection of vacuum generation systems substantially influences the operational reliability and economic efficiency of the packaging process.
Vacuum packaging of meat and sausage products offers a fundamental advantage: the elimination of the air in the packaging drastically reduces the oxygen content, slows down the activity of bacteria requiring oxygen and thus significantly increases shelf life.
Additionally, vacuum packaging is hygienic and enables the products to be presented in an attractive manner. A wide range of vacuum packaging machinery is available on the market, which means a suitable packaging machine can be found for all packaging requirements. Regardless of their design or size, these packaging machines have one thing in common: for all machines, vacuum must be generated to meet the requirements for vacuum packaging. This can be achieved by either an integrated or a separate vacuum pump. Other alternatives include central vacuum supply systems to which several packaging machines are connected.
A wide range of vacuum packaging machinery is available on the market, which means a suitable packaging machine can be found for all packaging requirements.
Integrated vacuum pump
Normally, the vacuum pump is integrated or set up separately in the immediate vicinity for any vacuum packaging machine – whether it be a vacuum chamber packaging machine, tray sealer or thermoforming packaging machine. Oil-lubricated rotary vane vacuum pumps are almost exclusively used for this purpose (Fig. 1).
Continuous further development ensures that the vacuum pumps of Dr.-Ing. K. Busch GmbH are always state-of-the-art, with millions in operation across the globe.
The vacuum pump, either integrated or set up separately at the packaging machine, is the simplest and most common way of generating the vacuum for packaging. Short pipes between the vacuum chamber, sealing station and the vacuum pump guarantee that the air is rapidly removed from the packaging. Larger-scale thermoforming packaging machines with high packaging volumes may also be fitted with a vacuum booster.
Higher speeds can be achieved by combining rotary vane vacuum pumps with vacuum boosters, thus reducing pump-down time.
Partial centralization
With partial centralization (Fig. 2), the rotary vane vacuum pumps are removed from the actual packaging room and integrated into a central pre-vacuum system for all packaging machines in a separate room. Dry, oil-free vacuum boosters are installed directly in the packaging machines and connected to the central pre-vacuum technology system with a system of pipes. A partially centralized system always makes sense when two to a maximum of five thermoforming packaging machines operate close to one another in one area. If more packaging machines are used, the investment costs are too high due to the vacuum boosters in the individual machines; thus it is recommended to fully centralize the vacuum supply.
-
Fig. 2: Partial centralisation of the vacuum supply. Source: Busch Vacuum Solutions.
Central vacuum supply
- Economic efficiency
Usually, fewer vacuum pumps are required for a central vacuum supply.
-
Fig. 3: Full centralisation of the vacuum supply. Source: Busch Vacuum Solutions.
-
Fig. 4: Centralised vacuum system for 30 packaging lines with thermoforming packaging machines. Source: Busch Vacuum Solutions.
- Hygiene
- Operation method
This requires a rough vacuum pump unit for the initial evacuation and a medium vacuum pump unit for the evacuation to packaging pressure. The reversing valves with the corresponding control units are attached to the packaging machines. They control the transition from a rough to a medium vacuum.
For thermoforming packaging machines, the moulding station is supplied using a separate thermoforming vacuum pump unit. This ensures that the previously heated base foils are sucked into the tray mould and take the desired shape.
On the one hand, this separation into various vacuum stations is necessary as the moulding and sealing functions run at different vacuums and, on the other, as a substantially lower pumping speed is required for the two-stage evacuation of the sealing chamber. The pipework serves as a vacuum buffer. This buffer is necessary to keep the packaging pressure at a constant level, even when all the packaging machines are running with the same number of cycles.
The central vacuum system is fully automatic: it activates individual vacuum modules if a greater vacuum is required and/or switches off individual vacuum modules if a smaller vacuum is required. If a vacuum pump fails in the rough, medium or thermoforming pump units, then the reserve pump is automatically activated. This ensures maximum operational reliability for the vacuum supply to the packaging machines.
- Maintenance
- Integration into the process control system
Summary
In systems using two or more vacuum packaging machines, the operator or responsible head of operations should consider how the vacuum is generated. They should not forget that production, e.g., with sausage fillers or tumblers, also requires vacuum that can likewise be supplied from a central vacuum supply.
Dr.-Ing. K. Busch GmbH is the world's largest manufacturer of vacuum pumps for packaging.