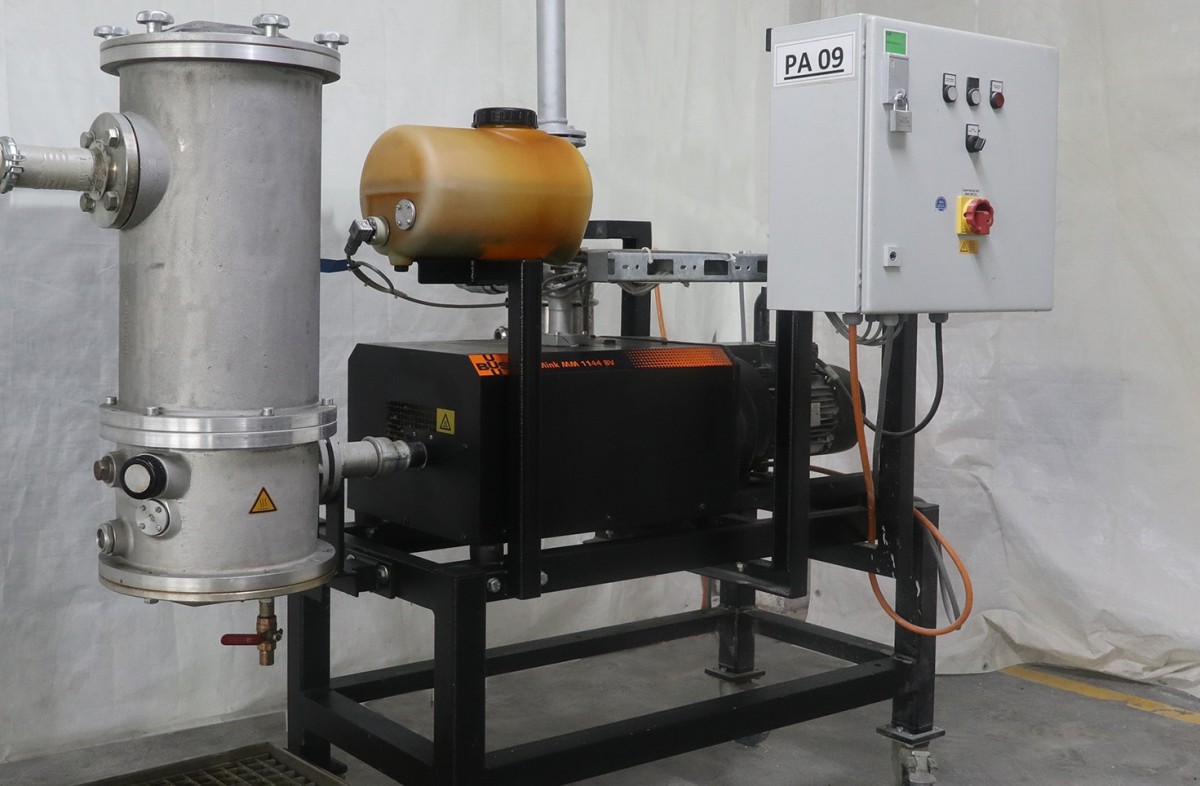
Fig. 1: One of a total of seven PLASTEX degassing systems at PolyComp. They are installed one floor above the extruders. Source: Busch Vacuum Solutions.
Modern Vacuum Technology for Melt Degassing During Extrusion
PolyComp GmbH
As a compounding specialist, the company PolyComp GmbH is both a contract manufacturer and licensed producer of complex engineering plastics. Its products range from high-temperature plastics and high-strength engineering thermoplastics to soft, flexible thermoplastic elastomers, which are combined with a wide range of additives on request. The extensive product portfolio calls for flexible production facilities made up of various extruders and some special screw configurations.
However, there is one constant in all of the extruders: for the extraction of vapors and gases from the molten material in the screw sections, PolyComp relies exclusively on PLASTEX degassing systems from Busch Vacuum Solutions. Equipped with MINK claw vacuum pumps, these systems are exceptionally reliable and easy to maintain.
However, there is one constant in all of the extruders: for the extraction of vapors and gases from the molten material in the screw sections, PolyComp relies exclusively on PLASTEX degassing systems from Busch Vacuum Solutions. Equipped with MINK claw vacuum pumps, these systems are exceptionally reliable and easy to maintain.
About PolyComp
PolyComp was founded as a management buy-out in 2000, and its headquarters are based in Norderstedt on the outskirts of Hamburg, Germany. In 2013, PolyComp was taken over by the Hamburg-based Feddersen Group, which focuses on the global trade of chemical and technical products.PolyComp's core business includes the compounding of polyolefins (PP/PE), as well as EVA, PA, PBT, PC, ABS, EVOH, POM and PMMA. These compounds are mixed with various additives ranging from carbon or natural fibers, simple fillers to glass beads, color additives or waxes.
Film Compounds
One of PolyComp's specialties are film compounds, which require extremely low quantities of gel. The production process involves an extrusion stage using specific screw configurations and the application of a screen changer with a high degree of filtration precision. The company uses a total of eight single or twin screw extruders. The molten material is degassed in six of the extruders. Up to 2009, the company used liquid ring vacuum pumps for this process.Disposing of the used water was becoming increasingly problematic as gases and vapors were mixing with the water and condensing. The cost of treating or disposing of the water was rising all the time.
Henning von Brühl, assistant to the production manager, adds: "We were never able to accurately predict what type of substances would collect in the water. It was not just gases, vapors, and polymers from the base substances; parts of the additives would also deposit in the vacuum pumps' operating fluid." This was due to the frequent change in product. Even if the base substances remained the same, the various additives used could change the composition of substances in the water. Since PolyComp runs a three-shift operation, five days a week, huge quantities of water were collected for treatment.
Our Solution
Searching for an environmentally friendly solution in 2009, the company came into contact with Busch, which offered a PASTEX degassing system (fig. 1) that required no operating fluids. The system consists mainly of a MINK claw vacuum pump (fig. 2) and an upstream standing filter and fine filter. The filters are used to separate out condensates and solids. MINK claw vacuum pumps do not require any operating fluids such as water or oil. This means that the pumped vapors and gases do not come into contact with any operating fluids, with which they could mix or react. However, even the most careful separator technology cannot always prevent residual monomers from getting into the pumps' interiors and cracking there. For this reason, the MINK claw vacuum pump is equipped with a flushing device. This enables a precisely dosed quantity of flushing liquid to be fed into the vacuum pump after defined intervals, helping to dissolve any cracks. Maintenance manager Stefan Stolp defined the quantity of flushing liquid and flushing intervals for each of the materials extruded. The flushing process can take place during periods of downtime or even while production is running.-
Fig. 2: MINK claw vacuum pumps form the heart of PLASTEX degassing systems. Thanks to their contact-free operating principle, they do not require any operating fluids such as water or oil. Source: Busch Vacuum Solutions.
After purchasing its first PLASTEX degassing systems, PolyComp gradually replaced all of its liquid ring vacuum pumps. Stefan Stolp is very happy with the solution. Firstly, it solved his problem with waste water; secondly, the PLASTEX degassing systems are completely reliable and require little maintenance effort. The filters have to be cleaned regularly and the flushing agent has to be refilled as needed. The intervals between refills vary depending on the material being processed. This work is carried out directly by members of the production team. The maintenance team dismantles and cleans every vacuum pump after 10 months on average. "All in all, the amount of work is very manageable compared to what we had to do with the old liquid ring vacuum pumps," says Henning von Brühl.
Engineer Simone Patermann has identified another benefit of using PLASTEX degassing systems. As head of the production, she always has her eye on energy consumption, not least because PolyComp is certified under ISO 50001 for energy management systems.
This is due to two main factors. First of all, the elimination of all operating fluids removes the need for power to transport them. Second of all, MINK claw vacuum pumps are completely contact-free. As a result, there are no components rubbing against each other and no force is needed to overcome this friction.
In 2018, PolyComp launched a new extrusion line, whose heart is a twin screw extruder with an output of up to 1,500 kilograms per hour. The two side dispensing units (fig. 3) allow different types of powder-based fillers to be added at the same time and compounded with a high output capacity. One side dispensing unit can be connected to a PLASTEX degassing system. This reduces the volume of the fillers and enables the bulk density to be tripled compared to a side dispensing unit without degassing. This significantly increases the total output rate.
Engineer Simone Patermann has identified another benefit of using PLASTEX degassing systems. As head of the production, she always has her eye on energy consumption, not least because PolyComp is certified under ISO 50001 for energy management systems.
MINK claw vacuum pumps have the highest efficiency factor among all mechanical vacuum technologies. This means that their power consumption is always lower compared to other mechanical vacuum pumps with the same performance.
In 2018, PolyComp launched a new extrusion line, whose heart is a twin screw extruder with an output of up to 1,500 kilograms per hour. The two side dispensing units (fig. 3) allow different types of powder-based fillers to be added at the same time and compounded with a high output capacity. One side dispensing unit can be connected to a PLASTEX degassing system. This reduces the volume of the fillers and enables the bulk density to be tripled compared to a side dispensing unit without degassing. This significantly increases the total output rate.
-
Fig. 3: The two side dispensing units on the twin screw extruder. A PLASTEX degassing system helps to reduce the volume when adding filler material. Source: PolyComp.
The management team at PolyComp agrees that – when it comes to reliability, maintenance effort and economic efficiency – they made the right choice opting for the PLASTEX degassing system from Busch. The high degree of reliability has a positive impact on production. Downtimes caused by breakdowns or last-minute repairs or cleaning work – as used to be the case with the liquid ring vacuum pumps – are now a thing of the past.