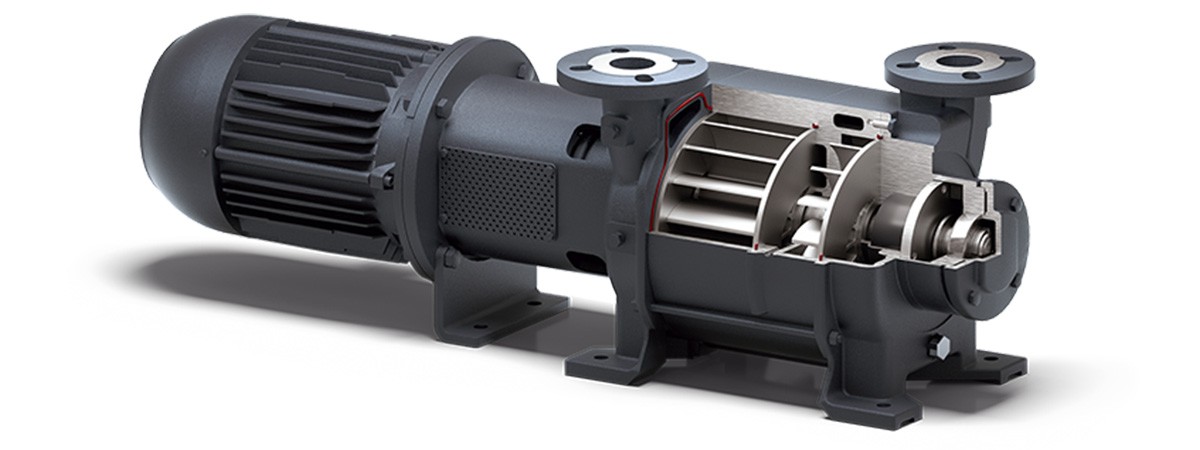
Source: Busch Vacuum Solutions.
Liquid Ring Vacuum Pumps - Classic Vacuum Technology and yet Still State of the Art
Operating principle
As an operating fluid, liquid ring vacuum pumps use water or a liquid compatible with the gas or vapour to be evacuated. Ethylene glycol, mineral oils or organic solvents are also used, as are other liquids that are already part of the process. The basic principle is the same in all sizes and versions.
-
Fig. 2: Cross-sectional view of a DOLPHIN liquid ring vacuum pump compression chamber. Source: Busch Vacuum Solutions.
Mechanism
Due to the operating fluid used, this mechanism can only be used in the rough vacuum range. The reason for this is that the achievable vacuum level depends on the vapour pressure and the viscosity of the operating fluid, which is constantly pumped through the vacuum pump. This allows a liquid ring vacuum pump to be operated at relatively low temperatures. It also predominantly operates isothermally. That means that the medium to be pumped hardly heats up during the compression process. This is why liquid ring vacuum pumps are virtually predestined for pumping vapours and gases with a high moisture proportion. The low temperatures in the vacuum pump are favourable for condensation of damp vapours and gases. To an extent, this means that the vacuum pump additionally functions as a capacitor. Because condensation already takes place when the gas enters the vacuum pump, the volume of the gas is drastically reduced. In addition to the condensation effect, this also achieves an increase in the nominal pumping speed. The operating fluid diverts the compression heat, a process that supports condensation and an increase in pumping speed. One significant advantage of liquid ring vacuum pumps is that the operating fluid and the materials used for the components can be adapted to fit the pumping medium. This also makes it possible to pump explosive gases and vapours. Due to the low operating temperatures, pumping explosive materials can, in any case, be considered much less problematic than with other mechanical vacuum pumps.
Construction
Basic differentiation is made between one- and two-stage liquid ring vacuum pumps. In the one-stage version, the compression process described above is performed in one compression stage. In the two-stage vacuum pump (fig. 3), the pre-compressed pumping medium from the first stage is conveyed to a second compression stage and compressed again. Ultimate pressures of 130 hPa (mbar) can be realized with one-stage liquid ring vacuum pump versions, while two-stage versions can achieve up to 33 hPa (mbar).
-
Fig. 3: Gas flow through a two-stage liquid ring vacuum pump. Source: Busch Vacuum Solutions.
Variants
Supply and removal of operating fluid can happen in three ways:1. Non-recirculating operation
This is the simplest variant for operating a liquid ring vacuum pump and is used any time there is sufficient operating fluid available. The compression stage is constantly supplied with operating fluid. The fluid is then discharged together with the gas and the condensate.
2. Open fluid circuit
In an open circuit (fig. 4), the operating fluid is diverted into a liquid separator together with the gas after it exits the vacuum pump. Liquid and gas are separated there. The gas is discharged or transferred while fresh operating fluid is supplied in the liquid separator. This guarantees that there is enough liquid in the circuit and that the temperature does not rise. This type of open circuit can save up to 50 percent of the fluid when compared to non-recirculating operation.
-
Fig. 4: DOLPHIN liquid ring vacuum pump with an open operating fluid circuit. Source: Busch Vacuum Solutions.
There is also a liquid separator downstream from the pump in a closed circuit (fig. 5). Gas is discharged from it while the operating fluid is diverted using a heat exchanger before it enters the vacuum pump again. The operating fluid is thus constantly cooled. This configuration saves up to 95 percent of the operating fluid. This means that only small amounts of fresh fluid need to be added via the liquid separator. We therefore recommend the closed circuit any time that sufficient operating fluid is not available or when as much operating fluid as possible should be conserved.
-
Fig. 5: DOLPHIN liquid ring vacuum pump with a closed operating fluid circuit. Source: Busch Vacuum Solutions.
Tailored vacuum systems
Liquid ring vacuum pumps are exceptionally well suited for use as modules in vacuum systems and installations. Lower ultimate pressures can be realized in combination with steam jets. Technically and economically optimum solutions can be found for vacuum systems that are directly tailored to the individual application. Busch Vacuum Solutions has decades of experience in designing, configuring and building these types of systems, which are used in economical and safe operation worldwide in chemical processing technology, petroleum production and processing, power generation and many other areas. The individual DOLPHIN liquid ring vacuum pump sizes from Busch are available in different ATEX-certified versions.
-
Fig. 6: Vacuum system with five one-stage DOLPHIN liquid ring vacuum pumps for degassing process fluid. Source: Busch Vacuum Solutions.