With two production facilities, Drobimex Sp. z o.o. is one of the largest producers of poultry products in Poland. Among other products, various types of poultry sausage are produced at the processing plant in Goleniow.
The various poultry goods are packaged on three packaging lines with thermoforming packaging machines that are connected to a central vacuum supply from Busch. This enables safe and highly economical packaging in a protective atmosphere.
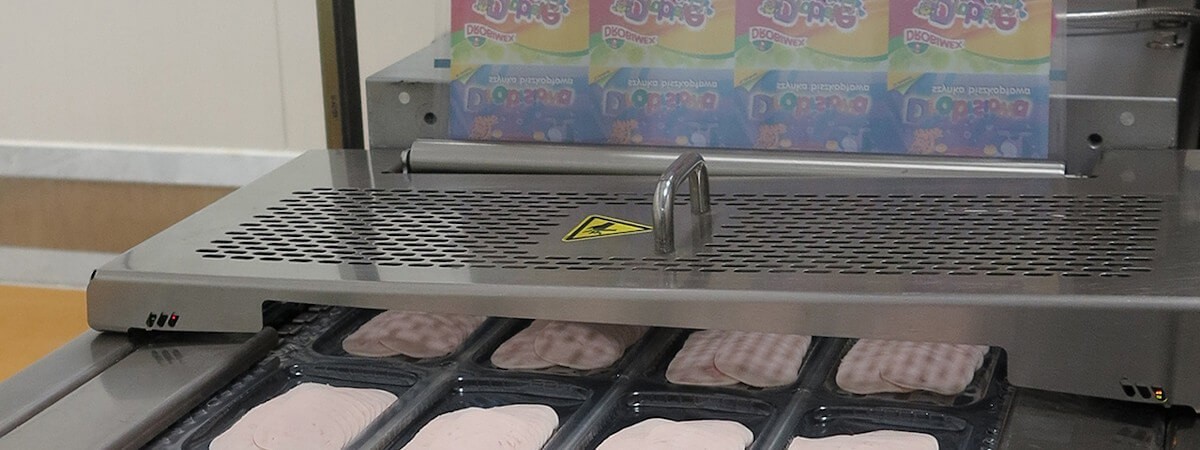
Fig. 1: Packaging poultry sausages on a thermoforming packaging machine. Source: Busch Vacuum Solutions.
Greater Efficiency and Reduced Cycle Times in Packaging Poultry Sausage with R5
Drobimex
At Drobimex in Goleniow, the meat from the freshly slaughtered chickens is processed into various sausage types after it is deboned. Sliced and portioned sausage specialities packaged in trays in a protective atmosphere make up a large part of production. The sausage products are packaged on a total of three packaging lines (fig. 1). These are located in a production building that was newly built in 2015. With the new construction project, Drobimex decided to acquire a central vacuum system (fig. 2) from Busch Vacuum Solutions and abandon the previous solution of attaching vacuum pumps directly to or in the packaging machine. One reason for this decision was the recommendation from colleagues from Wiesenhof, a German poultry producer in Rietberg, Germany, which also belongs to the PHW Group. They were already operating a central vacuum system with Busch vacuum pumps and had positive experience in the areas of energy savings and reliability. As a result, Maintenance Manager Andrzej Kaźmirski directly contacted Busch's Polish sales company, which ultimately designed and implemented a customized central vacuum system for Drobimex together with the main Busch plant in Germany. The challenge during this process was to design the system in such a way that it would fit into a narrow space outside the production and packaging rooms. For Andrzej Kaźmirski, it was extremely important that the vacuum supply be set up outside the cooled production spaces, because waste heat from the vacuum pumps would require increased cooling power for the rooms, which would inevitably lead to higher energy consumption. A further advantage of installing the vacuum supply outside of the production rooms is that maintenance personnel do not need to enter the hygienically sensitive areas and maintenance can be performed during normal working hours.
-
Fig. 2: Partial view of the central vacuum system. Source: Busch Vacuum Solutions.
Busch designed the system so that maximum cycle frequencies can be run on the packaging lines with thermoforming machines. In the process, the packaging chambers are evacuated in two stages. This utilizes the critical pressure gradient and thus achieves the shortest possible cycle times. This means that part of the central vacuum system is made up of rough vacuum pump stations that pre-evacuate the packaging to 50 millibars before fine vacuum pump stations are switched on with reversing valves to further reduce the vacuum in the packaging chamber to five millibars. Afterwards, the packaging is flooded with protective atmosphere, a gas mixture of carbon dioxide and nitrogen, and sealed. This is not only the fastest way to reach the desired vacuum level in the packaging; it is also the most efficient.
The high efficiency can be achieved because R5 rotary vane vacuum pumps with relatively low pumping speed are used to achieve the rough vacuum. In the fine vacuum pump stations, frequency controlled Panda vacuum boosters are used as booster pumps that only turn on after the rough vacuum has been achieved.
A thermoforming vacuum pump station supplies the vacuum of 180 millibars to the thermoforming machine moulding station. This vacuum forms the base foil of the packaging and thus forms the packaging tray.
An additional increase in efficiency is provided by a demand-based control system that ensures that the only vacuum pumps in operation are the ones that are actually needed. In practice, this usually means that all vacuum pumps are never simultaneously in operation and thus do not constantly consume electricity. With an average operating time of approximately ten hours per work day in a five- to six-day week, this benefit should not be underestimated.
Maintenance of the central vacuum system is performed by experienced Busch service technicians and regulated with a maintenance contract with Busch. Maintenance includes a semi-annual inspection of the entire system, including controls, as well as oil and filter changes for all vacuum pumps. After one year of operation, Andrzej Kaźmirski is highly satisfied with his central vacuum supply. During this time there have not been any malfunctions whatsoever, let alone a failure of individual vacuum pumps.