As a leading manufacturer of soft PVC rolls, sheets and web material, Jedi Kunststofftechnik GmbH has focused its production specifically on the processing of soft PVC. The material is fed from the delivered big bags to the extruders via a pneumatic suction conveying system.
Vacuum generation in the conveying system has now been redesigned and implemented. Since the beginning of 2018, Jedi Kunststofftechnik has had frequency-controlled MINK claw vacuum pumps in operation, which are much more energy-efficient than the side channel blowers previously used. This has enabled the energy consumption for vacuum generation to be reduced by up to 70 percent.
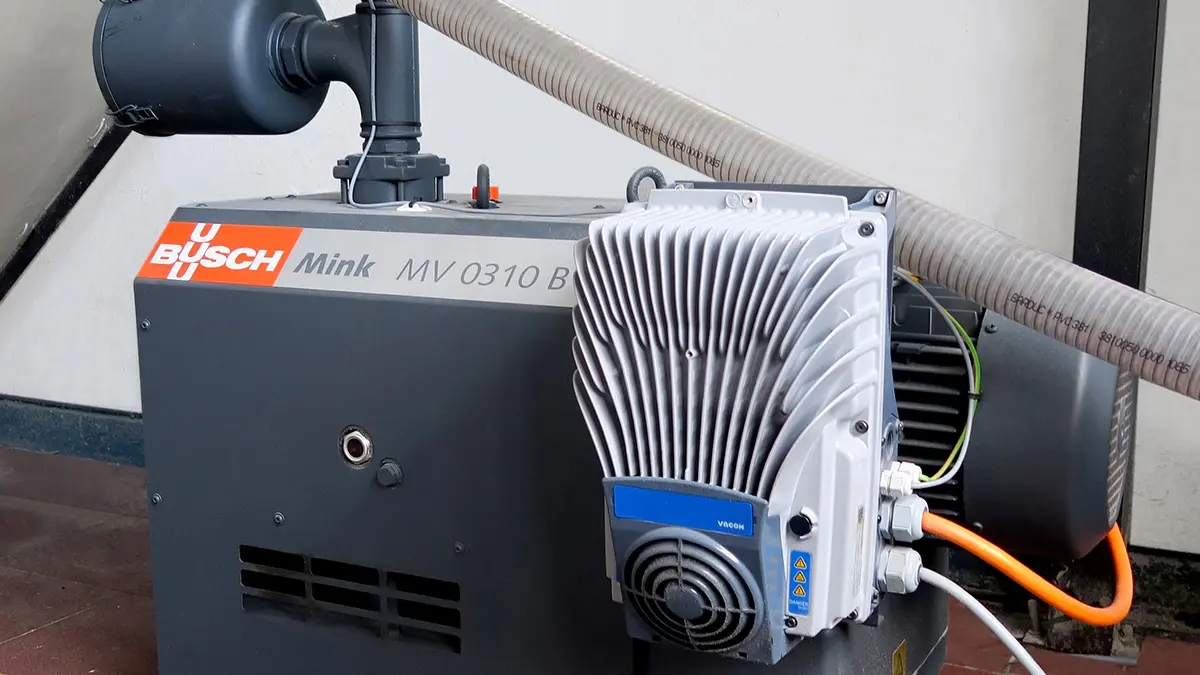
Fig. 1: One of Busch's three MINK MV 0310 B claw vacuum pumps for the vacuum supply of the conveying system at Jedi Kunststofftechnik. Source: Busch Vacuum Solutions.
Up to 70 Percent Energy Savings Thanks to Modern Vacuum Technology for Material Feed
Jedi Kunststofftechnik GmbH
Jedi Kunststofftechnik GmbH
Marco Di Martino founded Jedi Kunststofftechnik in Eitdorf, North Rhine-Westphalia, in the mid-1990s and specialized in transparent soft PVC semi-finished products. Today, his company employs 40 people and is one of the leading international manufacturers of soft PVC rolls, sheets and webs. These are processed by his customers into strip curtains or floor protection mats and flexible viewing windows on roller shutters or tents. Products manufactured in three-shift operation are supplied to customers throughout Europe in material thicknesses of one to twelve millimeters and a maximum roll width of 2200 millimeters.Pneumatic suction conveying process
Production takes place on five extrusion lines with single-screw extruders. The material is fed from the big bags via volumetric dosing systems and dryers to the extruders via suction conveying systems. In the past, four side channel blowers were installed on the four extrusion lines to generate the necessary vacuum on the conveying system. High failure rates due to bearing and engine damage as well as tarnished blade wheels made the side channel blowers unreliable vacuum generators.The four side channel blowers had a power requirement of between 12.5 and 15 kilowatts, depending on their size. Their operation was unregulated, i.e. the blowers ran continuously in three-shift operation. In terms of energy consumption and reliability, this was an extremely unsatisfactory solution for owner Marco Di Martino. The high noise level emanating from the blowers in the production hall also caused considerable disturbance.
Process optimization
After establishing contact with Busch Vacuum Solutions, a Busch vacuum specialist carried out measurements on the conveying system. He realized that the side channel blowers were constantly operating at their performance limits, at an absolute pressure of 700 millibar. At this pressure, a side channel blower only reaches about 30 percent of the nominal pumping speed. In order to eliminate this disadvantage, correspondingly large blowers with high nominal pumping speeds were used – which in turn resulted in higher energy requirements. The high pressure differential and the resulting low pumping speed were the reasons for the excessive heating of the blowers and the associated failures. As a result of this analysis of the actual state of the vacuum supply, Busch suggested the use of the new MINK MV 0310 B claw vacuum pump. At an absolute operating pressure of 700 millibar, these vacuum pumps have no loss of pumping speed. Their standard frequency-controlled drive allows them to automatically adjust their pumping speed to the demand by varying rotational speed. MINK MV claw vacuum pumps can also generate much lower pressures than side channel blowers, reaching up to 150 millibar (absolute).Marco Di Martino has now had two MINK MV 0310 B claw vacuum pumps (Fig. 1) in operation since the beginning of 2018, replacing the four side channel blowers previously installed. While the four side channel blowers consumed a total of 55 kilowatts, the MINK claw vacuum pumps only require 8 kilowatts each at 50-Hertz operation. Jedi Kunststofftechnik has installed another MINK MV 0310 B with the start-up of a fifth extrusion line. All three vacuum pumps are operated via a cascade control system. A total buffer volume of 1000 liters is stored in the two upstream containers. One of the three MINK MV claw vacuum pumps automatically starts when the absolute pressure in the containers rises above 500 millibar. The other two vacuum pumps switch on when 700 millibar absolute pressure is reached and support the first vacuum pump. Minor adjustments to the pressure or pumping speed are compensated by the variable speed drives.
In practice, one to two MINK vacuum pumps are sufficient to maintain the flow rate. The third vacuum pump is only used at peak demand. After six months of operating time, owner Marco Di Martino is extremely satisfied. On the one hand, it was possible to reduce the nominal power requirement of the vacuum supply (Fig. 2) from 55 to 24 kilowatts, although five extrusion lines are now in operation instead of the previous four. On the other hand, due to the frequency control of the new MINK MV 0310 B, none of the vacuum pumps runs in continuous operation, instead only when its power is actually required. The electricity bill for 2018 clearly demonstrated the energy cost savings: compared to the previous year, 160,000 kilowatt hours less were consumed. This was despite the fact that side channel blowers were still in use at the beginning of the year and the fifth extrusion line was added later.
-
Fig. 2: Cutaway drawing of a MINK MV claw vacuum pump. Source: Busch Vacuum Solutions.
While failures and repairs of blowers were frequent in the past, Busch's new claw vacuum pumps did not cause any problems at all. In addition to the costs for down times and repairs, this also has a positive effect on the throughput on the individual extrusion lines. The noise level of the new vacuum pumps is considerably lower than that of the side channel blowers before. Marco Di Martino says they really cannot be heard at all in the production room, which is right next to the extrusion lines. Maintenance of the MINK MV claw vacuum pumps is reduced to a minimum. Manufacturer Busch recommends changing the gear oil only after an operating time of up to 20,000 hours.