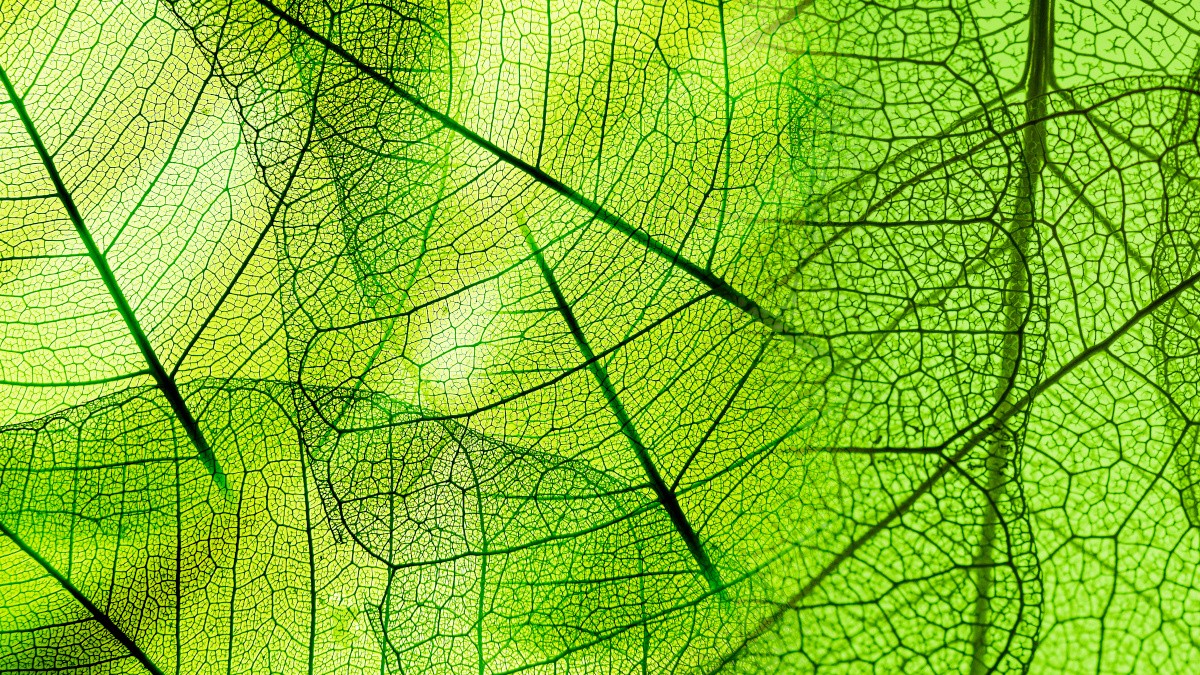
Source: Vera Kuttelvaserova – stock.adobe.com.
Green Actions at Busch Productions Worldwide
Busch Vacuum Solutions has initiated a series of sustainability measures that the company has made binding for all of its eight production sites.
Sustainability has to be lived. There must be a sustainability culture. For this, we need well-rehearsed processes.
Busch relies on making consumption quantifiable and thus continuously identifying potential savings.
Measurements are important because they enable us to review our approach and take the right action. Because everything we can measure, we can manage.
The company pays particular attention to ensuring that each implementation step is carried out correctly. All eight Busch production facilities worldwide are required to have an energy audit performed by an accredited external auditor. These can identify further potential for savings and optimization, resulting in more ways to increase energy efficiency. Furthermore, the audit can verify and transparently present the improvements that have resulted from previous changes.
Another sustainability measure is the implementation of continuous leakage audits. This is intended to detect leaks of compressed air and avoid unnecessary energy consumption. Regular inspections of the production facilities ensure that the leakage audits are carried out correctly, and also prevent systems from running unused.
A temperature is set for the buildings at Busch, which is measured and checked to ensure that the premises are neither undercooled in summer nor overheated in winter. In addition, the actual energy consumption is to be monitored.
Energy efficiency is also to become a selection criterion in the purchasing process, so that only energy-efficient purchases are made for the production sites in the future.
Furthermore, the reusability of what are known as one-way pallets is being tested in all Busch production facilities. Only damaged ones are recycled, while pallets that have remained intact are used again. In addition, cardboard packaging is being reused as filling material. New waste stations ensure transparency in waste separation and enable waste to be sorted by type. This means that it can be recycled more quickly without the need for complex processes to separate materials.
Individual production sites are also implementing various positive measures to make their sites and product testing processes more energy efficient. Photovoltaic systems are being installed on several company sites, efficiency filters reduce electrical losses in the power grid, process heat is used for heating and the use of LED lamps ensures that less energy is consumed overall.
Of course, steps to impact employee behavior are also part of the company’s sustainability concept. Awareness campaigns have been designed to sensitize and motivate, and e-charging stations are available free of charge to employees and customers at various Busch locations to charge their electric vehicles. This enables employees to make their own contribution to the company’s sustainability.