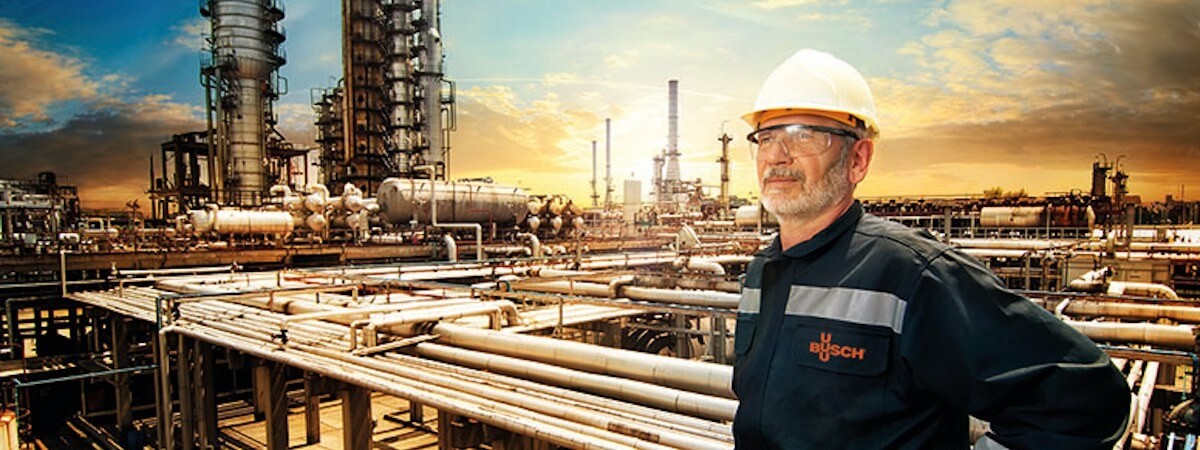
Source: © www.istockphoto.com - paparazzit.
Dry Vacuum Technology for Chemical and Pharmaceutical Processes
Vacuum plays an essential role in chemical and pharmaceutical processes. Whether in vacuum conveying, inertization, distilling or drying processes, vacuum is used everywhere to make processes safer, faster and more economical or to make them possible in the first place.
The various technologies for generating vacuum are versatile. Liquid ring vacuum pumps and steam ejectors have been the robust workhorses for many decades when it comes to generating vacuum.
However, like rotary vane vacuum pumps with recirculating oil lubrication, they have one disadvantage: they require an operating fluid that comes into contact with the process gas.
However, like rotary vane vacuum pumps with recirculating oil lubrication, they have one disadvantage: they require an operating fluid that comes into contact with the process gas.
Innovative: Dry screw vacuum pumps
In the mid-1990s, Busch Vacuum Solutions launched the first screw vacuum pump on the market, the COBRA. The major difference to the vacuum pumps known at that time was that screw vacuum pumps did not require any operating fluid to compress the process gas. This is why they are called "dry" screw vacuum pumps (fig. 1). Dry screw vacuum technology is now also widely used in the chemical and pharmaceutical industries.-
Fig. 1: Dry screw vacuum pump for chemical and pharmaceutical processes. Source: Busch Vacuum Solutions.
Operating principle
In a screw vacuum pump, two interlocking screw-shaped rotors rotate in opposite directions (fig. 2). The process gases are drawn in, trapped between the cylinder and screw chambers, compressed and transported to the gas discharge. During the compression process, the screw rotors do not come into contact with each other or the cylinder. Precise manufacturing and minimal clearances between the moving parts enable this operating principle and, in addition, ensure a low ultimate pressure of up to 0.01 millibar (absolute).-
Fig. 2: Modern screw vacuum pumps have variable pitch screws, which allow an even temperature distribution inside the vacuum pump. Source: Busch Vacuum Solutions.
COBRA screw vacuum pumps operate with a cooling system which ensures even heat distribution, greater thermal efficiency and stability throughout the pump body. This allows the temperature to be selected so that it is high enough not to condense the process gas but low enough to avoid potential temperature-related problems such as gas deposition or spontaneous ignition.
The absence of operating fluid allows a compression in the process chamber without contamination or reaction.
Protecting the vacuum system
Depending on the process gas, the vacuum pump can be exposed to certain risks. It is therefore important that the process gases are sufficiently known to minimize these risks. Different components are often required, which can be installed on the inlet or pressure side, in order to convey the process gas without damaging the vacuum pump. This is called a vacuum system, which can also consist of several vacuum pumps (fig. 3).-
Fig. 3: Vacuum system with four screw vacuum pumps as backing pumps. Source: Busch Vacuum Solutions.
For safe operation of the vacuum system, it is important to protect it from corrosion and deposits caused by crystallization or polymerization, and to increase the material resistance.
Protection against corrosion
Various measures can be effective in protecting the vacuum system or the individual vacuum pumps against corrosion:- The first possibility is to prevent corrosive substances from entering the interior of the vacuum pump. This can be implemented by upstream condensers or gas scrubbers.
- The second possibility to avoid corrosion is to keep the process stream in the gas phase. In a screw vacuum pump this can be implemented by setting a certain operating temperature. In addition, the process gas can be diluted by a supplied ballast gas to reduce the partial pressure of the condensable gases. So, the following simple logic applies: suction in gaseous form and ejection in gaseous form. The minimum temperature must therefore be selected so that it is high enough to prevent gases from condensing out. The maximum temperature must be selected so that the vacuum pump is not damaged or so that the maximum permissible temperature according to ATEX classification is not exceeded.
- A third possibility is to use compatible materials for the vacuum pump. In COBRA screw vacuum pumps from Busch Vacuum Solutions, for example, all parts in contact with the process are made of ductile cast iron by default and have a special coating that is resistant to almost all chemicals.
Protection from particles entering the system
Screw vacuum pumps should always be operated with an inlet screen or an inlet filter. This is to prevent particles from entering the inside of the vacuum pump. Due to the precise manufacturing of screw vacuum pumps with the associated small clearances and tolerances, there is a certain sensitivity to entrained particles.Dry screw vacuum pumps are frequently used with particulate dryers, especially in the pharmaceutical industry. A certain number of such particles can easily pass through the vacuum pump together with the process gas or be flushed out at the end of the process.
Nevertheless, it is advisable to take appropriate precautions in order to prevent particles from being sucked in on a regular basis. For example, Busch offers a large number of different particle filters for every application.
Leak-tightness of the vacuum pump/vacuum system
Vacuum pumps and vacuum systems in a chemical environment must be so tight that no or still a minimum of ambient air can enter and create a potentially explosive atmosphere, or toxic or explosive gases can escape.Polymer o-rings are generally used to prevent leaks between two stationary parts. The resistance depends on the selected polymer. The seal material therefore also needs to be adapted to possible process gases.
Busch Vacuum Solutions has had a dynamic sealing concept for rotating shaft feedthroughs certified by TÜV SÜD in accordance with the Technical Instructions on Air Quality Control (TA Luft). These seals are considered technically leak-tight.
Tips for operation
For most applications it is recommended that the vacuum pump is warmed up for a certain lead time before process operation. This allows the specified temperature to be set.
After the end of the process, it is recommended to purge the vacuum pump with non-condensable inert gas to completely remove the process gas from the vacuum pump before switching it off. Nitrogen is normally used for this flushing process.
Flushing the vacuum pump with a cleaning liquid at the end of the process is also possible and recommended if there is a risk of deposits forming inside the vacuum pump during cooling.
For most applications it is recommended that the vacuum pump is warmed up for a certain lead time before process operation. This allows the specified temperature to be set.
After the end of the process, it is recommended to purge the vacuum pump with non-condensable inert gas to completely remove the process gas from the vacuum pump before switching it off. Nitrogen is normally used for this flushing process.
Flushing the vacuum pump with a cleaning liquid at the end of the process is also possible and recommended if there is a risk of deposits forming inside the vacuum pump during cooling.
Explosion protection
With different sealing systems, various coatings and appropriate accessories, COBRA screw vacuum pumps from Busch can be configured to be compatible with virtually any chemical.In addition, various ATEX versions are available for COBRA screw vacuum pumps in accordance with EU Directive 2014/34/EU.
Also, any other national regulation can be adapted for these vacuum pumps like EX-proof in US or KOSHA in South Korea. This means that these vacuum pumps can also be used worldwide in potentially explosive areas and for conveying explosive gases and vapors.
Flame arresters may also be integrated if necessary.