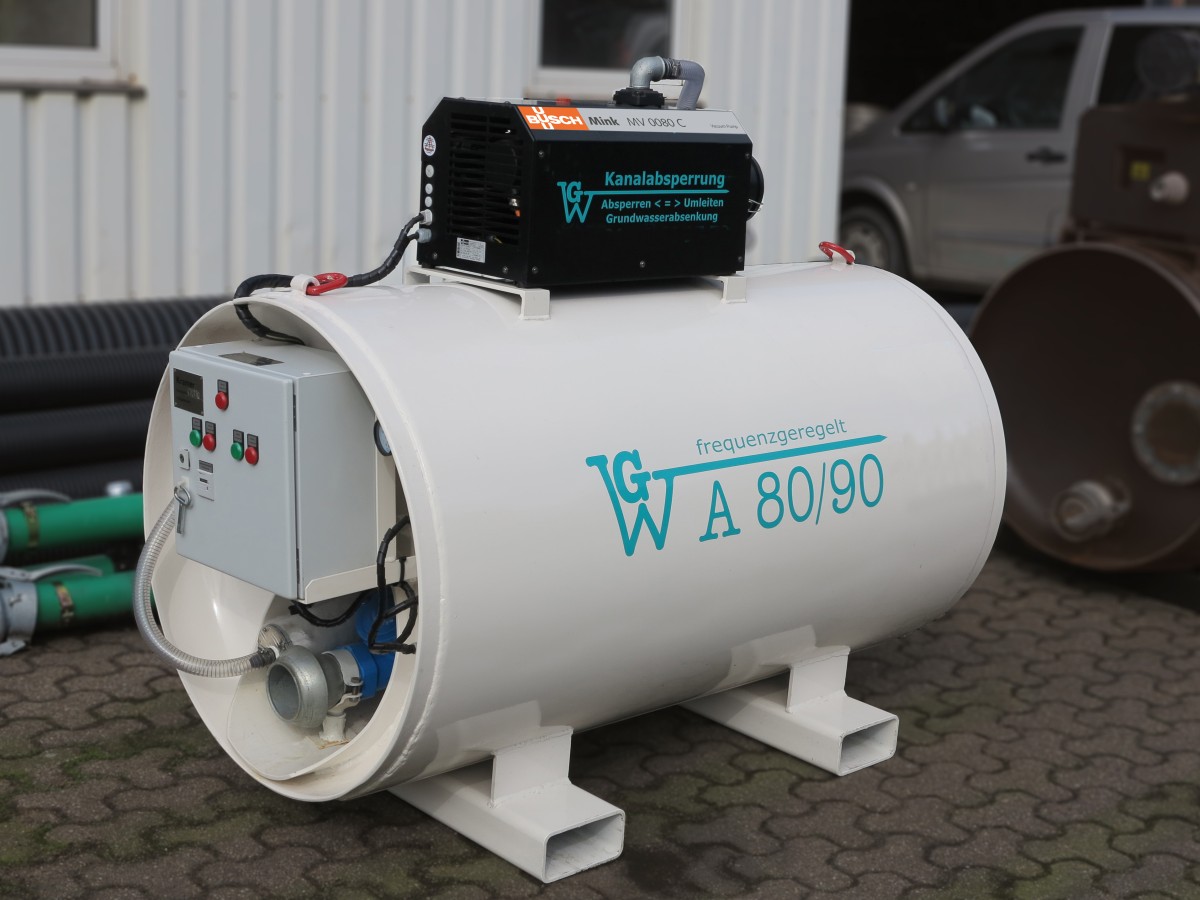
Fig. 1: The GWA 80/90 groundwater lowering system with a frequency-controlled Mink MV 0080 C claw vacuum pump from Busch. Source: Busch Vacuum Solutions.
Claw Vacuum Technology Brings Energy and Maintenance Savings in Lowering Groundwater
GW Kanalabsperrung
New vacuum methods are being used by GW Kanalabsperrung to reduce the level of groundwater. MINK claw vacuum pumps from Busch are being employed exclusively in the newly developed GWA series groundwater lowering systems. When compared to conventional vacuum generators for lowering groundwater, Mink claw vacuum pumps offer significant advantages in the areas of maintenance, efficiency and reliability.
GW Kanalabsperrung always has a selection of these systems stored at its company headquarters in Wesel, Germany. These systems are rented to companies and municipalities having problems with water tables that are too high and need to be lowered during the construction phase for underground construction, pipeline construction or sewerage construction.
In the process, GW Kanalabsperrung offers its customers customized service that includes installation of the system with all filters and hose lines through to daily monitoring of functionality and correct operation. This has enabled GW Kanalabsperrung to build up a customer base throughout the entire state of North Rhine-Westphalia.
Until now, systems from different manufacturers were sold. In 2015, Managing Director Gerhard Wagner himself developed a new system and, after many years of experience with different vacuum pumps, he decided to use the MINK claw vacuum technology from Busch.
Whilst the first systems were delivered to customers last year, GW Kanalabsperrung unveiled this new system approach to a larger audience of specialists for the first time at Bauma 2016 in Munich.
In the process, GW Kanalabsperrung offers its customers customized service that includes installation of the system with all filters and hose lines through to daily monitoring of functionality and correct operation. This has enabled GW Kanalabsperrung to build up a customer base throughout the entire state of North Rhine-Westphalia.
Until now, systems from different manufacturers were sold. In 2015, Managing Director Gerhard Wagner himself developed a new system and, after many years of experience with different vacuum pumps, he decided to use the MINK claw vacuum technology from Busch.
Whilst the first systems were delivered to customers last year, GW Kanalabsperrung unveiled this new system approach to a larger audience of specialists for the first time at Bauma 2016 in Munich.
Gerhard Wagner had been involved in the topic of groundwater lowering long before the company was founded. Working with vacuum methods basically follows the same principle (Fig. 1).
To prevent groundwater from penetrating an excavation pit or, alternatively, to prevent an excavation pit from having to be drained, suction pipes with filters are placed around the pit one to two metres apart from each other. These can be up to six to seven metres deep in the ground. The number of these suction pipes, their distance from one another and the filters used depend on ground conditions.
To prevent groundwater from penetrating an excavation pit or, alternatively, to prevent an excavation pit from having to be drained, suction pipes with filters are placed around the pit one to two metres apart from each other. These can be up to six to seven metres deep in the ground. The number of these suction pipes, their distance from one another and the filters used depend on ground conditions.
-
Fig. 2: The operating principle of the vacuum method for groundwater lowering: 1 Groundwater lowering system, 2 Manifold, 3 Excavation, 4 Suction pipe, 5 Suction filter, 6 Groundwater. Source: Busch Vacuum Soultions.
All suction pipes are connected to the groundwater lowering system using a manifold. This groundwater lowering system always consists of one or two vacuum pumps, a vacuum container and one or two water pumps as well as a control system.
Procedure
- When the system is turned on, the vacuum pumps pump all the air out of the container and the entire pipe network.
- The vacuum created by this process sucks groundwater from the vicinity of the individual filters, which lowers the overall water table.
- The water is sucked into the container by the vacuum.
- As soon as a certain level is reached in the container, the water pump, usually a centrifugal or submersible pump, begins to pump the water out of the container and directs it into the sewer system or a body of water via a hose.
- Once the level of water in the container is reduced to a minimum, the water pump shuts off and the vacuum once again sucks groundwater into the vacuum container.
This process repeats itself constantly around the clock to ensure that the excavation pit is drained during the construction phase. Depending on how long the excavation lasts, this process can go on for weeks to months.
The liquid ring vacuum pumps often used for this process have the drawback that they require water as an operating fluid. This water is continuously fed into the liquid ring vacuum pump by way of an internal circulation system. In the process, the amount of water must be checked regularly to ensure that the pump does not run dry, which would lead to pump failure.
Despite circulatory operation, fresh water must be regularly fed into the system during operation of the liquid ring vacuum pump. In practice, this can be difficult during excavation work. Groundwater that has been sucked in must not enter this circulatory system in any case because, despite filtering, groundwater often carries fine and abrasive sand that quickly causes wear on the liquid ring vacuum pumps.
Despite circulatory operation, fresh water must be regularly fed into the system during operation of the liquid ring vacuum pump. In practice, this can be difficult during excavation work. Groundwater that has been sucked in must not enter this circulatory system in any case because, despite filtering, groundwater often carries fine and abrasive sand that quickly causes wear on the liquid ring vacuum pumps.
-
Fig. 3: Cross section of a dry, non-contact Mink claw vacuum pump. Source: Busch Vacuum Solutions.
Up to now, Gerhard Wagner mainly used oil-lubricated rotary vane vacuum pumps to lower groundwater. They are reliable. However, they require a certain level of maintenance. Dry-running rotary vane vacuum pumps turned out to be completely unsuitable.
Whereas the oil in oil-lubricated rotary vane vacuum pumps creates a protective film inside the pump, protecting it against corrosion,
dry-running rotary vane vacuum pumps always risk becoming corroded during downtimes, in which case they fail to start. Even after a break in operation of only one day, the vanes can become stuck in the rotor. When starting, they can break and lead to greater damage inside the vacuum pump.
Whereas the oil in oil-lubricated rotary vane vacuum pumps creates a protective film inside the pump, protecting it against corrosion,
dry-running rotary vane vacuum pumps always risk becoming corroded during downtimes, in which case they fail to start. Even after a break in operation of only one day, the vanes can become stuck in the rotor. When starting, they can break and lead to greater damage inside the vacuum pump.