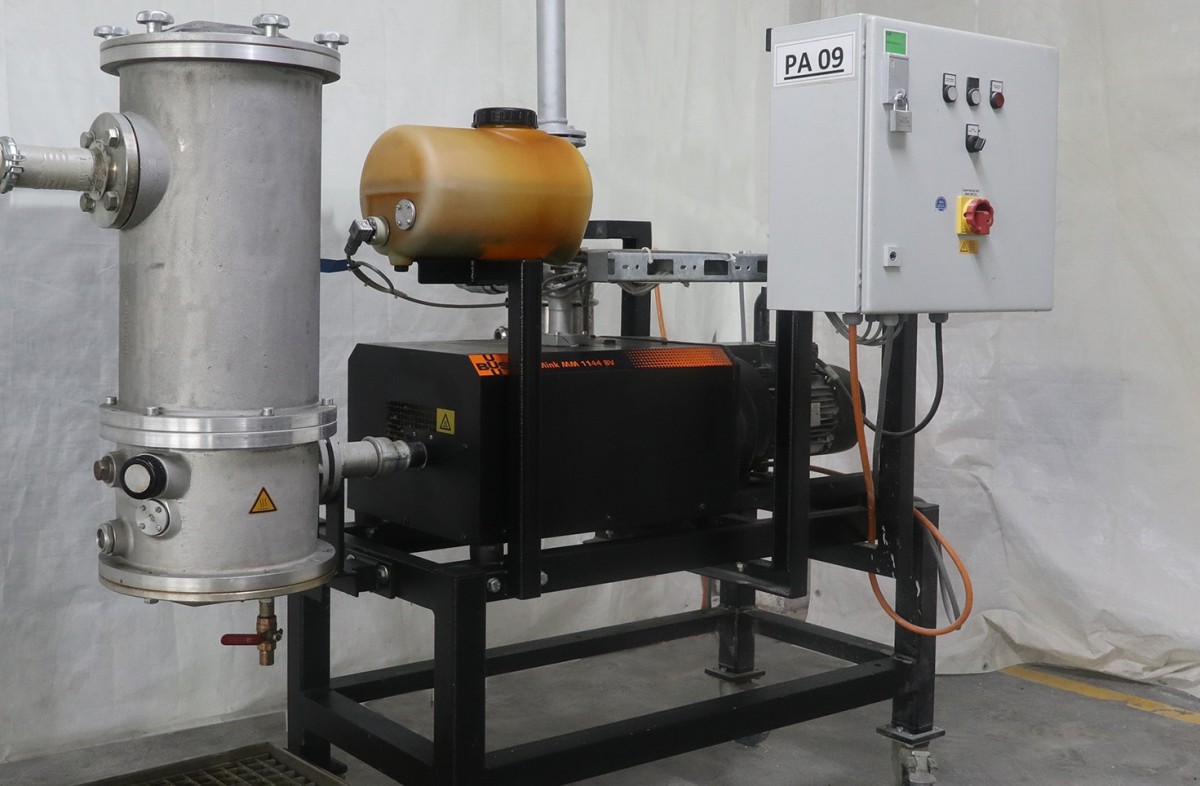
Tecnología de vacío de última generación para desgasificación del plástico durante la extrusión
Sin embargo, hay una constante en todas las extrusoras: para la extracción de vapores y gases del material fundido en las diferentes secciones del tornillo, PolyComp confía exclusivamente en los sistemas de desgasificación PLASTEX de Busch Vacuum Solutions. Equipados con bombas de vacío de rotores de uña MINK, estos sistemas son excepcionalmente fiables y fáciles de mantener.
-
Fig. 1: Uno de los siete sistemas de desgasificación PLASTEX de PolyComp. Están instalados un piso por encima de las extrusoras.
Acerca de PolyComp
PolyComp se fundó a raíz de una compra de acciones por parte de los ejecutivos en 2000 y tiene su sede en Norderstedt, a las afueras de Hamburgo, Alemania. En 2013, PolyComp fue adquirida por el grupo Feddersen de Hamburgo, que está centrado en el comercio global de productos químicos y técnicos.El negocio central de PolyComp incluye los compuestos de poliolefinas (PP/PE), así como EVA, PA, PBT, PC, ABS, EVOH, POM y PMMA. Estos compuestos se mezclan con distintos aditivos que van desde el carbón, las fibras naturales o simples rellenos hasta cuentas de cristal, aditivos de color o ceras.
Compuestos de lámina
Una de las especialidades de PolyComp son los compuestos de lámina, que requieren cantidades de gel extremadamente bajas. El proceso de producción implica una fase de extrusión con configuraciones de tornillo específicas y la aplicación de un cambio de filtros con un alto grado de precisión en la filtración. La empresa utiliza un total de ocho extrusoras de tornillo único o doble. El material fundido se desgasifica en seis de las extrusoras. Hasta el año 2009, la empresa utilizó bombas de vacío de anillo líquido para este proceso.La eliminación del agua utilizada era cada vez más problemática, ya que los gases y vapores se mezclaban con el agua y la condensaban. El coste del tratamiento o de la eliminación del agua era cada vez más elevado.
Nuestra solución
Buscando una solución más respetuosa con el medioambiente, en 2009 la empresa se puso en contacto con Busch, que le ofreció el sistema de desgasificación PLASTEX (fig. 1), que no requiere fluidos de trabajo. El sistema está formado principalmente por una bomba de vacío de rotores de uña MINK (fig. 2), un separador de líquidos y polvo previo y un filtro fino. Los filtros se utilizan para separar los condensados y los sólidos. Las bombas de vacío de rotores de uña MINK no requieren ningún fluido de trabajo, como agua o aceite. Esto significa que los vapores y gases bombeados no entran en contacto con ningún fluido de trabajo con el que puedan mezclarse o reaccionar. Sin embargo, ni siquiera la tecnología de separación más cuidadosa es capaz de evitar siempre que los monómeros residuales se introduzcan en el interior de las bombas y se depositen. Por esta razón, la bomba de vacío de rotores de uña MINK está equipada con un dispositivo de inyección. Esto permite introducir una dosis precisa de líquido de lavado en la bomba de vacío tras intervalos de tiempo definidos, lo que ayuda a eliminar cualquier deposición. El responsable de mantenimiento, Stefan Stolp, definió la cantidad de líquido de lavado y los intervalos de limpieza de cada uno de los materiales extruidos. El proceso de lavado se puede llevar a cabo en periodos de inactividad o incluso con la producción en marcha.-
Fig. 2: Las bombas de vacío de rotores de uña MINK son el núcleo de los sistemas de desgasificación PLASTEX. Gracias a su principio de funcionamiento sin contacto, no requieren ningún fluido de trabajo, como agua o aceite.
La ingeniera Simone Patermann encuentra otra ventaja en el uso de los sistemas de desgasificación PLASTEX. Como jefa de la producción, siempre controla el consumo energético, entre otras cosas porque PolyComp tiene el certificado ISO 50001 para sistemas de administración de energía.
En 2018, PolyComp introdujo una nueva línea de extrusión, cuyo núcleo es una extrusora de doble tornillo con un rendimiento de hasta 1.500 kilogramos por hora. Las unidades de dosificación en dos laterales (fig. 3) permiten añadir distintos tipos de rellenos en polvo a la vez, que se combinan con una alta capacidad de rendimiento. Puede conectarse una unidad de dosificación en un lateral del sistema de desgasificación PLASTEX. Esto reduce la cantidad de relleno y permite triplicar la densidad aparente en comparación con una unidad de dosificación en un lateral sin desgasificar. Esto aumenta considerablemente el rendimiento total.
-
Fig. 3: Las unidades de dosificación de dos laterales en la extrusora de tornillo doble. Un sistema de desgasificación PLASTEX ayuda a reducir el volumen cuando se añade el material de relleno. Fuente: PolyComp