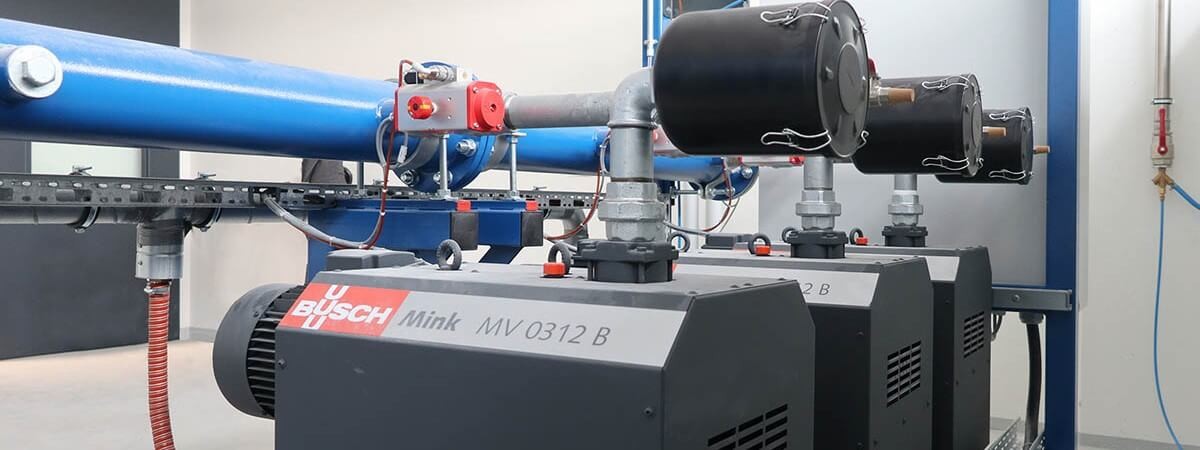
Fig. 1: A central vacuum supply at Fuyao Europe delivers the vacuum for eight windshield production lines. Source: Busch Vacuum Solutions.
Energy-Efficient Vacuum Supply in the Production of Windshields
Fuyao Europe
At its state-of-the-art manufacturing plant in Leingarten, Germany, Fuyao Europe produces ready-to-install glass windows for the automobile industry from raw glass. To hold the windshields during the finishing process, Fuyao Europe opted for an exceptionally effective and efficient method of vacuum generation.
A central vacuum supply from Busch Vacuum Solutions delivers the vacuum to ensure safe handling on the eight production lines for windshields.
Fuyao Europe GmbH is the European subsidiary of the Fuyao Glass Industry Group. The company was founded in China in 1987 and produces automobile glass. They are processed to a stage that enables vehicle manufacturers to install them directly into their cars. With a total of 25,000 employees, the Fuyao Group has become one of the world’s largest producers of automobile glass. Opened in 2017, the Leingarten production plant in the German state of Baden-Württemberg is equipped with cutting-edge production technology. The plant supplies European vehicle manufacturers including the VW Group, BMW, Audi, Ford and Opel. The factory runs a three-shift model for round-the-clock production.
In his bid to continuously streamline production, CTO Torben Ludwig is always on the lookout for new, innovative technical solutions. For instance, he had been looking for a way to reduce the setup times for windshield production. Windshields are manufactured on eight production lines. These include a holding and assembly device that is used to hold the inserted windshield in the correct position. The sealing profile of EPDM (ethylene propylene diene monomer) rubber is then stuck onto the windshields while they are in these devices. The water tank profile is also attached to the bottom of the window; this profile ensures that rainwater is drained into the intended channels.
-
Fig. 2: By switching from a decentralized system to a central vacuum supply, CTO Torben Ludwig was able to significantly reduce setup times, considerably decrease power consumption and move heat and noise emissions away from the production lines. Source: Busch Vacuum Solutions.
The shape of the windshields differs depending on the brand and the vehicle’s model series. This means that a particular holding and assembly device is used for every brand and every model and this device has to be switched every time the product changes. In the past, each of these devices was equipped with an individual vacuum pump, which had to be connected every time the device was switched.
To speed up this process, the vacuum specialists from Busch recommended using a central vacuum supply. Connected via pipelines, this central system supplies all eight devices with vacuum, which can be easily connected via quick-release mechanisms. What is more, a central vacuum supply like this can help to save a great deal of energy.
CTO Torben Ludwig opted for this solution, which was then installed and commissioned in September 2019.
As well as a significant reduction in setup times, additional benefits soon become apparent. Where eight oil-lubricated vacuum pumps with a rated current of 2.2 kW each once ran around the clock, there is now one demand-driven central vacuum supply with three MINK claw vacuum pumps. The claw vacuum pumps were generously dimensioned in view of potential plans to add further holding and handling devices to the supply in future. At the moment, only one of the three MINK claw vacuum pumps ever runs at one time; a second claw vacuum pump can be activated briefly to cover peaks in demand. Thanks to the demand-driven operation, the system only delivers as much performance as actually required. An intermediary vacuum buffer makes sure the required vacuum level is applied directly to the devices when needed.
Each of the three MINK claw vacuum pumps is driven by a motor with a rated current of 5.5 kW. In practice, however, only one of the three vacuum pumps runs constantly. A second vacuum pump runs for no more than half of the operating time. Compared with the eight original vacuum pumps and their 2.2 kW drive units, which ran permanently during the three shifts, this has achieved an energy saving of over 50 percent.
A further benefit is that the central vacuum supply is set up in a separate room. This eliminated noise and heat emissions at the work stations.
MINK claw vacuum pumps from Busch work completely dry. This means that the compression chamber contains no oil or any other operating fluids. As a result, they are nearly maintenance-free. Compared to oil-lubricated vacuum pumps, they therefore require none of the maintenance jobs related to the operating fluid oil, such as changing the oil, filters or seals, thus eliminating the costs for procuring and disposing of the operating fluids.
The vacuum system has a redundant operating model. This ensures maximum operational safety on the one hand and, on the other, sufficient power reserves to connect additional vacuum consumers. What is more, the system can be enlarged at any time. The demand-driven control system has been developed to make sure all three of the MINK claw vacuum pumps have the same number of operating hours.