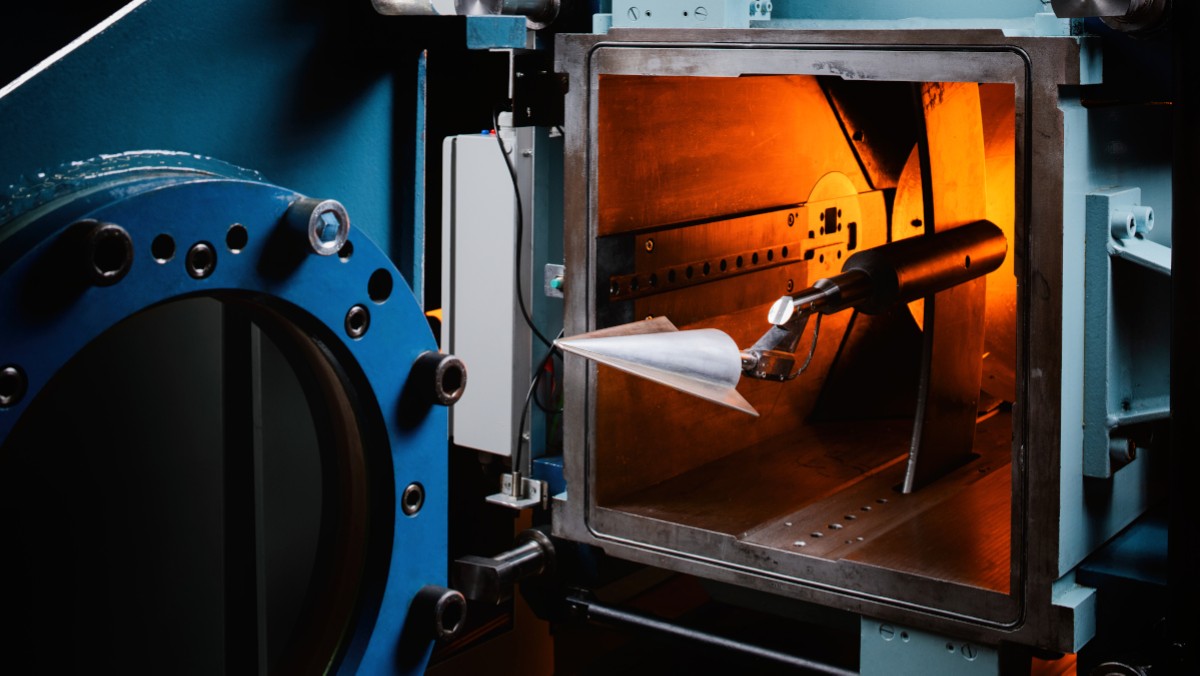
The German Aerospace Center (DLR) in Göttingen is researching fluid mechanics phenomena, which are essential for adequately predicting the performance of supersonic aircraft. Source: DLR.
From Wind Tunnels to Space: Vacuum for Aerospace Research
German Aerospace Center (DLR)
At the German Aerospace Center (DLR) in Göttingen, scientists are exploring the phenomena of compressible flow mechanics in Europe’s largest and most powerful tube wind tunnel using a COBRA screw vacuum pump from Busch Vacuum Solutions. The goal is to make the aerospace of tomorrow safer and more efficient.
Two accumulator tubes of more than 80 meters in length run over an open space next to the building and pass through the solid outer wall to the inside: The enormous dimensions of the research facility become clear as soon as you enter the site around the Institute of Aerodynamics and Flow Technology at the DLR in Göttingen. Inside, a giant vacuum vessel with a volume of 50 m³ is connected to the tubes. Detailed and fundamental studies are carried out there to investigate the fluid mechanics phenomena that are essential for adequately predicting the performance of supersonic aircraft. How can the aerospace vehicles of tomorrow become more environmentally friendly, safer and more efficient? And how can you use precise computer simulation of supersonic flight to evaluate new configurations while still in the design process? The scientists want to provide answers to these questions, and many others, with the tube wind tunnel.
The large-scale research facility was opened in the 1950s. Göttingen-based physicist and flow researcher Prof. Hubert Ludwieg developed a revolutionary drive system for intermittently operating high-speed wind tunnels, which enabled studies with supersonic and hypersonic flows to be carried out. He called this principle a tube wind tunnel – which to this day is also known around the world as a “Ludwieg tube.” In 1968, the Ludwieg Tube Wind Tunnel, Göttingen (RWG) was the first of these large-scale aerodynamic research plants in the world to be put into operation. It is still in use at the DLR to this day.
Vacuum technology from Busch is an indispensable part of these research projects.
The large-scale research facility was opened in the 1950s. Göttingen-based physicist and flow researcher Prof. Hubert Ludwieg developed a revolutionary drive system for intermittently operating high-speed wind tunnels, which enabled studies with supersonic and hypersonic flows to be carried out. He called this principle a tube wind tunnel – which to this day is also known around the world as a “Ludwieg tube.” In 1968, the Ludwieg Tube Wind Tunnel, Göttingen (RWG) was the first of these large-scale aerodynamic research plants in the world to be put into operation. It is still in use at the DLR to this day.
-
Construction of the Ludwieg Tube Wind Tunnel, Göttingen. Source: DLR.
Experiments at supersonic speed
The operating principle of the tube wind tunnel uses the interaction of pressure and vacuum, where the accumulator tubes serve as pressure vessels in which the air is compressed. To prevent air condensation in the ultrasonic nozzle, which occurs due to the strong expansion and the associated cooling of the air, the accumulator tubes must be heated to simulate high supersonic velocities.
The accumulator tubes are connected to the ultrasonic nozzle via a quick-action slide valve. The measuring section is found at the end. This is where experiments are carried out. At the end of the measuring section is the vacuum vessel, which the vacuum pump is connected to. A vacuum slide valve between the measuring section and the vacuum vessel enables access to the measuring section as required. The vacuum vessel is evacuated using the vacuum pump. A COBRA NX screw vacuum pump from Busch Vacuum Solutions is used for this. It generates vacuum of approximately 10 to 40 mbar in the vacuum vessel. In the accumulator tubes, there is overpressure of approximately 2 to 40 bar.
To perform a test, the test model is placed in the measuring section using a movable model holder. Test models include aircraft models, sensors or material samples. Opening the quick-slide valve creates a running dilution wave that flows into the accumulator tube and accelerates the accumulator air towards the nozzle. Due to the differential pressure between the accumulator tube and the vacuum vessel, and thanks to the specially shaped ultrasonic nozzle, an ultrasonic flow is created in the RWG measuring section. Speeds of up to Mach 7 can be achieved – corresponding to seven times the speed of sound. Measurement times of up to 350–400 milliseconds are realized in the RWG. This is a peak value for wind tunnels of this type and gives researchers enough time to study the flow around the test models. During this time period, statistically relevant data or image sequences can be recorded to enable reliable data averaging and analysis.
The operating principle of the tube wind tunnel uses the interaction of pressure and vacuum, where the accumulator tubes serve as pressure vessels in which the air is compressed. To prevent air condensation in the ultrasonic nozzle, which occurs due to the strong expansion and the associated cooling of the air, the accumulator tubes must be heated to simulate high supersonic velocities.
The accumulator tubes are connected to the ultrasonic nozzle via a quick-action slide valve. The measuring section is found at the end. This is where experiments are carried out. At the end of the measuring section is the vacuum vessel, which the vacuum pump is connected to. A vacuum slide valve between the measuring section and the vacuum vessel enables access to the measuring section as required. The vacuum vessel is evacuated using the vacuum pump. A COBRA NX screw vacuum pump from Busch Vacuum Solutions is used for this. It generates vacuum of approximately 10 to 40 mbar in the vacuum vessel. In the accumulator tubes, there is overpressure of approximately 2 to 40 bar.
To perform a test, the test model is placed in the measuring section using a movable model holder. Test models include aircraft models, sensors or material samples. Opening the quick-slide valve creates a running dilution wave that flows into the accumulator tube and accelerates the accumulator air towards the nozzle. Due to the differential pressure between the accumulator tube and the vacuum vessel, and thanks to the specially shaped ultrasonic nozzle, an ultrasonic flow is created in the RWG measuring section. Speeds of up to Mach 7 can be achieved – corresponding to seven times the speed of sound. Measurement times of up to 350–400 milliseconds are realized in the RWG. This is a peak value for wind tunnels of this type and gives researchers enough time to study the flow around the test models. During this time period, statistically relevant data or image sequences can be recorded to enable reliable data averaging and analysis.
-
Recording of a test model in the RWG measuring section. Source: DLR.
More efficient testing thanks to vacuum
Vacuum technology is important not only for accelerating, but also for slowing down the high flow velocity. The air from the accumulator tube is collected in the vacuum vessel during the test and then discharged outside as normal ambient air. Dr. Erich Schülein, Group Leader and Scientific Supervisor of the RWG at the Institute of Aerodynamics and Flow Technology, explains: "Thanks to vacuum technology, we can carry out the tests much more efficiently. Without it, we would not only have to significantly increase the boost pressure in the accumulator tube, but also the requirements for the stability of the entire system and the testing technology in order to achieve the required pressure ratio in the ultrasonic nozzle at all. The technical effort required for this would be enormous. The vacuum pump does this work for us. The combined application of pressure and vacuum accumulators makes it easy to change the pressure level and thus the Reynolds number of the flow."
The tube wind tunnel in Göttingen has been in use since 1968 together with an old rotary vane vacuum pump. In 2021, it was high time to replace it. Busch was able to win the contract as part of a tender. The company’s experts then provided support with their expertise in selecting and dimensioning the system to find a suitable solution. A solution was quickly found with the dry COBRA NX.
Vacuum technology is important not only for accelerating, but also for slowing down the high flow velocity. The air from the accumulator tube is collected in the vacuum vessel during the test and then discharged outside as normal ambient air. Dr. Erich Schülein, Group Leader and Scientific Supervisor of the RWG at the Institute of Aerodynamics and Flow Technology, explains: "Thanks to vacuum technology, we can carry out the tests much more efficiently. Without it, we would not only have to significantly increase the boost pressure in the accumulator tube, but also the requirements for the stability of the entire system and the testing technology in order to achieve the required pressure ratio in the ultrasonic nozzle at all. The technical effort required for this would be enormous. The vacuum pump does this work for us. The combined application of pressure and vacuum accumulators makes it easy to change the pressure level and thus the Reynolds number of the flow."
The tube wind tunnel in Göttingen has been in use since 1968 together with an old rotary vane vacuum pump. In 2021, it was high time to replace it. Busch was able to win the contract as part of a tender. The company’s experts then provided support with their expertise in selecting and dimensioning the system to find a suitable solution. A solution was quickly found with the dry COBRA NX.
-
The COBRA NX screw vacuum pump provides reliable and efficient testing conditions. Source: Busch Vacuum Solutions.
Karsten Pfeiffer, Technical Manager of the RWG, explains: "For us, it is crucial that the vacuum pump used works reliably, because the flow generated in the tube wind tunnel must be clean. The tests are often carried out several times, and it is important that the conditions are reproducible at all times – which is why nothing should interfere with the flow." The performance of the COBRA also made a very positive impression. Compared to the previous rotary vane pump, the Busch screw vacuum pump evacuates the vacuum vessel twice as fast. The most commonly required pressure of 50 mbar in the vessel is now reached after just 15 minutes instead of half an hour. These shorter run times have a very positive effect on the energy consumption of the plant. In addition, a frequency converter adapts the vacuum pump's rotational speed to the required pressure conditions.
The institute’s employees are also pleased with the new vacuum solution. Previously, they were unable to use the working rooms directly above the plant during the tests due to the high noise level and vibrations generated by the old vacuum pump. With the COBRA, this is no longer a problem, as it operates very quietly and with low vibration. "You can't hear anything except a slight buzz," laughs Pfeiffer. Another major benefit is oil-free operation. "In the past, I had to do hands-on work regularly and change the oil – and then also change my resulting dirty clothes. This is no longer necessary. Maintenance is carried out by a Busch service technician as part of a maintenance contract. All I have to do is switch on the pump and it starts running," says Pfeiffer happily.
Clean vacuum for technological progress
The reliable vacuum solution from Busch plays a key role in the success of the experiments in the RWG and supports technological progress. The DLR makes the results of its basic research available to companies in the aerospace industry to develop and refine technologies for current and future missions. The Göttingen-based scientists also work closely with international organizations such as NASA, ESA and the other DLR sites on global research projects. In the past, for example, a model of the X-38 spacecraft was tested in the Göttingen Ludwieg Tube Wind Tunnel on behalf of NASA and ESA. This craft was intended as a crew return vehicle (CRV) to be able to bring ISS astronauts back to Earth in the event of an emergency. This type of spacecraft must withstand enormous heat and mechanical loads when entering the Earth’s atmosphere. These conditions were replicated as accurately as possible in the tube wind tunnel .
The institute’s employees are also pleased with the new vacuum solution. Previously, they were unable to use the working rooms directly above the plant during the tests due to the high noise level and vibrations generated by the old vacuum pump. With the COBRA, this is no longer a problem, as it operates very quietly and with low vibration. "You can't hear anything except a slight buzz," laughs Pfeiffer. Another major benefit is oil-free operation. "In the past, I had to do hands-on work regularly and change the oil – and then also change my resulting dirty clothes. This is no longer necessary. Maintenance is carried out by a Busch service technician as part of a maintenance contract. All I have to do is switch on the pump and it starts running," says Pfeiffer happily.
Above all, the proximity of Busch to customers is a key benefit. Thanks to the company's extensive service network, the local contact person can be on site very quickly when needed.
Clean vacuum for technological progress
The reliable vacuum solution from Busch plays a key role in the success of the experiments in the RWG and supports technological progress. The DLR makes the results of its basic research available to companies in the aerospace industry to develop and refine technologies for current and future missions. The Göttingen-based scientists also work closely with international organizations such as NASA, ESA and the other DLR sites on global research projects. In the past, for example, a model of the X-38 spacecraft was tested in the Göttingen Ludwieg Tube Wind Tunnel on behalf of NASA and ESA. This craft was intended as a crew return vehicle (CRV) to be able to bring ISS astronauts back to Earth in the event of an emergency. This type of spacecraft must withstand enormous heat and mechanical loads when entering the Earth’s atmosphere. These conditions were replicated as accurately as possible in the tube wind tunnel .
-
This model of the X-38 spacecraft was examined in the RWG system on behalf of ESA and NASA. Source: DLR.
"Despite enormous advances in numerical flow mechanics, many phenomena in turbulent flows still cannot be adequately and accurately predicted. In our studies, we create an important validation database that helps improve existing models and develop new numerical calculation methods. We see this as the actual purpose of this research facility," says Schülein. Vacuum technology from Busch is an important part of this.