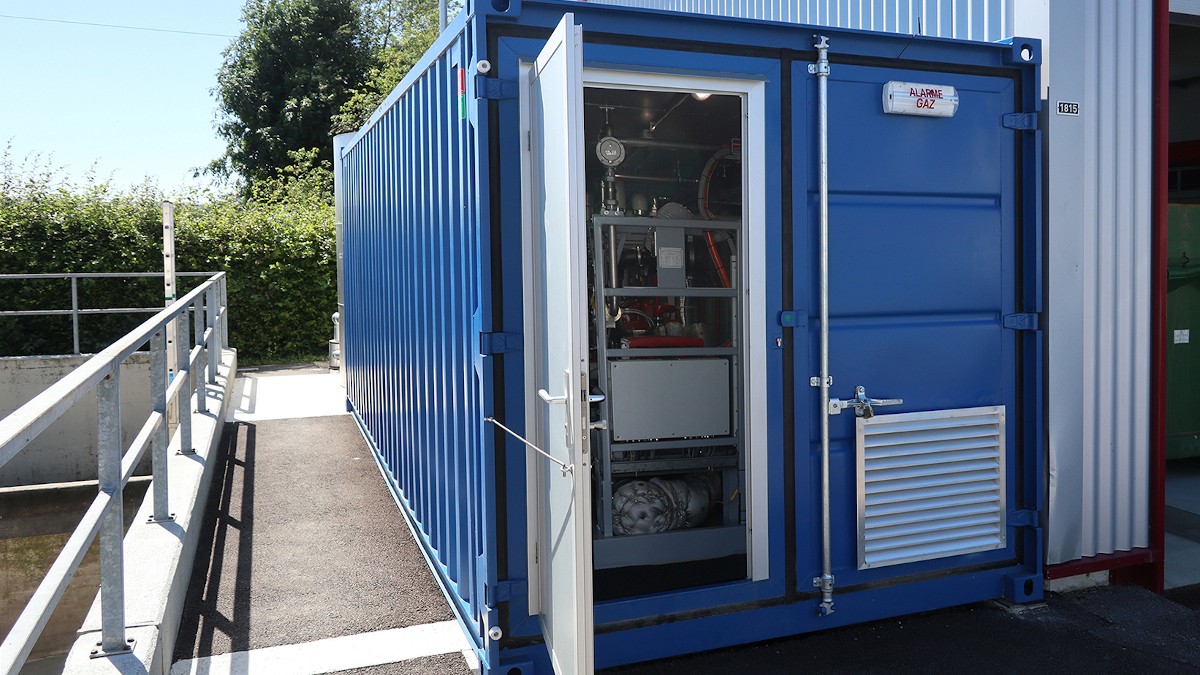
Fig. 1: The new cogeneration unit at Echallens wastewater treatment plant is installed in a container. Using the biogas recovered from the sludge, it generates 150,000 kilowatt-hours of power per year. Source: Busch Vacuum Solutions.
Producing Energy with Less Energy
Ever since it was commissioned in 1974, Echallens wastewater treatment plant in the Swiss canton of Vaud has been generating power from the recovery of biogas. In May 2020, two old oil-lubricated piston compressors used to mix the sludge in the digester were replaced by one MINK claw compressor from Busch Vacuum Solutions. This enabled the amount of power required for this process to be reduced by up to 40 percent. For the director of the treatment plant, this means he needs less energy to produce energy.
Echallens treatment plant is operated by the municipality of Echallens, located not far from Vaud’s capital Lausanne, and treats the wastewater from the towns of Echallens, Montilliez and Villars-le-Terroir. It was designed to cater to a population equivalent of 10,000 - a capacity limit that has been largely exhausted. The canton’s plans for the region of Echallens Haut-Talent include the consolidation of wastewater treatment by the year 2025 in an effort to make these operations more economically efficient in future. The plans also aim to improve the treatment of micro-pollutants. In future, the plan is that Echallens treatment plant will replace all other local sewage treatment plants and then treat the wastewater from nine of the district’s municipalities in total. To achieve this, Echallens is due to be expanded to a population equivalent of 26,000.
In 2019, a new cogeneration unit (Fig. 1) was already built on the treatment plant’s premises and generates an annual volume of 150,000 kilowatt-hours of power from the biogas plant. The warm water recovered from the cogeneration unit is mainly used for the plant’s own needs, for instance, to warm up the sludge in the digester or heat indoor areas. To make the process of recovering biogas (Fig. 2) from the digester more economically efficient as well, a decision was taken to optimize the circulation of biogas within the digester, which has a capacity of 350 cubic meters. A portion of the biogas generated in the digester is fed back into the sludge. To do this, the biogas is suctioned out of the top part of the digester, compressed with a compressor and fed back into the sludge at the bottom of the digester. The biogas flows through the sludge and then collects back up at the top of the digester, where it is fed through a line and into a gas tank as an interim reservoir. From the gas tank, the biogas then goes straight to the cogeneration unit. This currently runs for 20 hours a day and is only switched off for a few hours at night.
-
Fig 2: Process for generating power from biogas at Echallens treatment plant. Source: Busch Vacuum Solutions.
The process of circulating biogas has the following benefits: 1. The concentrated sludge is heated to 38° Celsius in the digester. Flooding the sludge with biogas helps to ensure that the heat is evenly distributed. 2. Mixing the sludge also helps to avoid deposits collecting and compacting at the bottom of the digester. 3. The rising of the gas bubbles up through the sludge improves the microbiological degradation processes in the sludge, which ultimately leads to a higher gas yield. 4. Circulating biogas through the sludge also means that it does not have to be mixed mechanically.
Two piston compressors were installed in 1974 to mix the biogas into the sludge, though one was designed to be redundant to allow the process to continue should the other compressor break down. In practice, however, it turned out that the capacity of one compressor was not sufficient, so both compressors ran all the time and there was no longer any redundancy. Both compressors were equipped with a motor with a rated current of 6.7 kilowatts.
After consulting a process engineer from the Swiss company Busch AG, a company belonging to the international group Busch Vacuum Solutions, the operator decided to purchase a MINK claw compressor (Fig. 3) from Busch.
-
Fig. 3: Up to 95 cubic meters of biogas per hour are transported by the MINK claw compressor at an overpressure of 0.6 bar. Source: Busch Vacuum Solutions.
This compressor is ATEX-certified (II 2G IIB3 T3 (i)/II 3G IIB3 T4(o)), which means that flame arresters are no longer required. Furthermore, it is equipped with a variable speed drive so that the volume flow can be adapted precisely to the requirements in the digester.
The MINK claw compressor has been in operation since May 2020 and normally runs at full load with a power consumption of 4.5 kilowatts and a constant overpressure of 0.6 bar. Compared to the power consumption of the two older piston compressors, which had one 6.7-kilowatt motor each, this results in theoretical energy savings of more than 65 percent.
MINK claw compressors compress biogas without using any oil at all. This is made possible by the compressors’ contact-free operating principle, which means that the internal moving parts do not come in contact with each other or the housing. As a result, no oil changes are needed, unlike the oil-lubricated piston compressors which required two each year. As the 4.5 liters of oil from each compressor came into contact with the biogas, the old oil had to be disposed of accordingly. MINK claw compressors have an internal gearbox. This contains 0.85 liters of gearbox oil. Busch recommends an oil change after no more than 20,000 operating hours and an annual visual inspection to check the condition and oil quantity as a precaution.
The operator has also noticed yet another advantage during the first few months of operation:
The claw compressor is much quieter than even just one of the piston compressors we used before. Noise levels have more than halved.