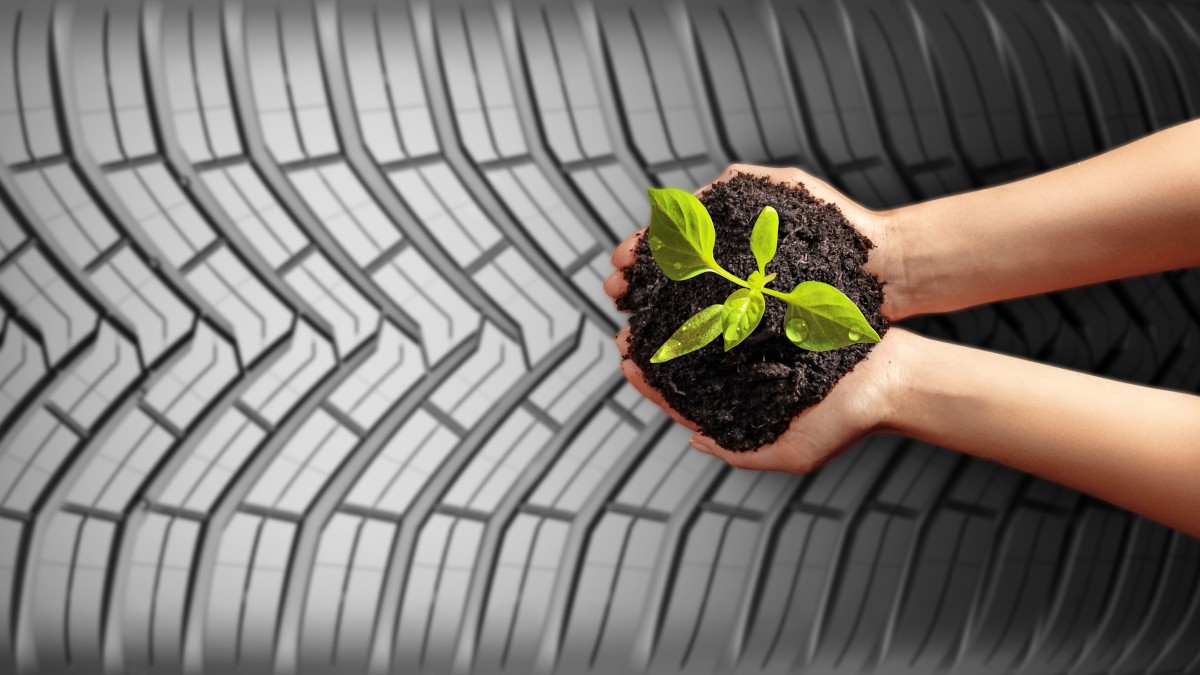
Fig. 1: Los neumáticos de Continental se fabrican utilizando tecnología de vacío avanzada de Busch. Foto: Continental Reifen GmbH
Nueva solución de vacío garantiza unos neumáticos seguros y sostenibles en Continental
Continental Reifen Deutschland GmbH
Continental Reifen Deutschland GmbH fabrica neumáticos de alta calidad para automóviles y furgonetas en su planta de producción de Aachen, Alemania. En su proceso de fabricación de neumáticos, Continental utiliza un método de generación de vacío extremadamente efectivo y, sobre todo, eficiente, en el que un suministro de vacío centralizado de Busch Vacuum Solutions abastece el vacío necesario para garantizar una manipulación segura en tres máquinas de corte textil. Además de reducir considerablemente el ruido en la sala de producción, esta solución de vacío también permite un alto nivel de ahorro en energía y costes de mantenimiento para el fabricante de neumáticos.
Casi uno de cada tres vehículos en Europa utiliza neumáticos fabricados por Continental, que mezcla la propia materia prima de caucho natural, después la extruye y, tras varios pasos intermedios, la procesa para obtener neumáticos listos para montar. Un solo neumático está formado esencialmente por tres componentes: cable textil, cable de acero y una mezcla de caucho natural. Estos tres materiales básicos se combinan de una forma específica en cada componente del neumático, después se ensamblan, se les da la forma del neumático y se endurecen.
El cable textil está formado por una gran cantidad de hilos textiles y se introduce en una calandradora mediante un gran dispositivo de desenrollado. Allí es donde el cable textil se recubre con caucho natural y se crea una red cauchutada en forma de una banda larga continua de menos de un milímetro de grosor. Esta red se corta a la anchura deseada en perpendicular al patrón trenzado y se prensa de nuevo en un rodillo textil para su posterior procesamiento. El material textil se fija más tarde a la capa más interna del caucho. Funciona como un elemento de refuerzo en el interior del neumático. La orientación radial de los hilos asegura una mayor estabilidad. Esta capa influye principalmente en la capacidad de carga del neumático, así como en el comportamiento de suspensión y en las características de manipulación.
Casi uno de cada tres vehículos en Europa utiliza neumáticos fabricados por Continental, que mezcla la propia materia prima de caucho natural, después la extruye y, tras varios pasos intermedios, la procesa para obtener neumáticos listos para montar. Un solo neumático está formado esencialmente por tres componentes: cable textil, cable de acero y una mezcla de caucho natural. Estos tres materiales básicos se combinan de una forma específica en cada componente del neumático, después se ensamblan, se les da la forma del neumático y se endurecen.
El cable textil está formado por una gran cantidad de hilos textiles y se introduce en una calandradora mediante un gran dispositivo de desenrollado. Allí es donde el cable textil se recubre con caucho natural y se crea una red cauchutada en forma de una banda larga continua de menos de un milímetro de grosor. Esta red se corta a la anchura deseada en perpendicular al patrón trenzado y se prensa de nuevo en un rodillo textil para su posterior procesamiento. El material textil se fija más tarde a la capa más interna del caucho. Funciona como un elemento de refuerzo en el interior del neumático. La orientación radial de los hilos asegura una mayor estabilidad. Esta capa influye principalmente en la capacidad de carga del neumático, así como en el comportamiento de suspensión y en las características de manipulación.
Uso de vacío en máquinas de corte textil
La tecnología de vacío se utiliza en tareas de manipulación en la máquina de corte textil. La red cauchutada se corta a la longitud deseada y después se aplica directamente a otra banda mediante pick and place. En este paso, una colocación correcta es el aspecto más importante para la calidad de la red textil acabada. Cada capa debe colocarse exactamente encima de la otra. Antes había una soplante de canal lateral instalada en cada una de las tres máquinas de corte textil. Estas suministraban el vacío necesario para manipular las bandas textiles. Las soplantes funcionaban constantemente a plena potencia y, por tanto, consumían grandes cantidades de energía. Además, creaban una considerable contaminación acústica para el personal de producción.
Suministro sostenible de vacío Busch para máquinas de corte textil
Un empleado de Continental Reifen sugirió a través de su sistema de gestión de ideas que se revisara el suministro de vacío de las máquinas de corte textil. Su mayor preocupación era la aguda contaminación acústica debido a las soplantes de canal lateral que utilizaban. Dado que Continental siempre está buscando formas de mejorar, decidieron buscar una solución más ergonómica y eficiente. Los expertos en vacío de Busch Vacuum Solutions recomendaron usar una bomba de vacío de rotores de uña MINK para generar vacío y les suministraron un sistema de prueba. Ingmar Heinze, director de servicios e infraestructura sostenible, solo tardó un par de días en convencerse de que había encontrado la solución adecuada para generar vacío. Tras la prueba, se instaló un sistema de vacío con dos bombas de vacío MINK MV Synchro en Continental. Este sistema ha sustituido las tres soplantes de canal lateral anteriores y ahora suministra de forma centralizada el vacío necesario para varias máquinas de corte textil a través de unos tubos de acero inoxidable. Las bombas de vacío MINK MV Synchro están equipadas de serie con un convertidor de frecuencia y una unidad de regulación basada en la demanda. Las bombas de vacío detectan el caudal que necesitan suministrar en el proceso en curso para sujetar de forma segura el cable textil cauchutado y colocarlo con precisión.
-
Fig. 2: Suministro de vacío con dos bombas de vacío de rotores de uña MINK MV para la manipulación de cables textiles. Fuente: Busch Vacuum Solutions.
Beneficios del suministro de vacío de Busch en el corte de textiles
Afortunadamente, el uso de este nuevo sistema de vacío no solo resolvió el problema principal de la contaminación acústica. Los soplantes de canal lateral anteriores alcanzaban unos niveles sonoros de 94 dB. Esto suponía unos altos niveles de contaminación acústica para el personal en la sala de producción. Con el nuevo sistema de vacío de Busch, el nivel sonoro de la unidad de vacío ni siquiera se puede detectar, ya que queda ahogado por el ruido ambiente normal, lo que significa que está por debajo de los 72 dB.Además de esta considerable reducción del ruido, el nuevo sistema de vacío también ha supuesto un ahorro energético significativo. Gracias al control basado en la demanda, no siempre se utiliza el rendimiento completo, lo que significa que el sistema de vacío a menudo funciona con una velocidad de rotación y un consumo más bajos. Además, el sistema se apaga automáticamente cuando no es necesario sostener bandas textiles. El consumo de los soplantes que se utilizaban anteriormente era generalmente de 15 kWh. Cuando se tomaron mediciones con el nuevo sistema de vacío, se determinó un consumo medio de solo 800 vatios por hora.
Esto equivale a un ahorro de costes energéticos de más del 90 %. De este modo, la inversión se amortizó rápidamente y, gracias a sus características energéticas, reúne los requisitos para solicitar financiación de la Oficina Federal de Economía y Control de las Exportaciones (BAFA).
La nueva solución también ahorra cerca de un 90 % de costes de mantenimiento anuales. Los soplantes de canal lateral requerían reparaciones intensivas y eran una fuente de costes elevados. Las bombas de vacío de rotores de uña MINK MV ofrecen una compresión completamente seca del aire de entrada, por lo que funcionan sin fluidos de trabajo, como aceite y agua. Esto significa que las bombas de vacío prácticamente no necesitan mantenimiento. Los tiempos de inactividad para el mantenimiento también solían suponer un problema. Con el nuevo sistema de vacío con dos bombas de vacío de rotores de uña MINK, las pocas operaciones de mantenimiento que requieren se pueden llevar a cabo en una de las dos bombas de vacío mientras la otra continúa suministrando vacío al sistema. Esto permite acabar con las interrupciones y permite una mayor disponibilidad de las máquinas de corte textil.
El nuevo sistema de vacío lleva en funcionamiento desde enero, e Ingmar Heinze se muestra completamente satisfecho.
Estamos muy satisfechos con nuestro nuevo suministro de vacío para manipular bandas textiles durante la producción. No solo hemos podido reducir considerablemente la contaminación acústica para nuestros empleados, sino que también hemos reducido enormemente el consumo y el esfuerzo de mantenimiento, aumentando la productividad del sistema. ¡Esto sí que es un buen ejemplo de mejoras sostenibles!»
-
Fig. 3: Tuberías para el suministro de vacío de las máquinas de corte textil en Continental Reifen Deutschland GmbH. Fuente: Busch Vacuum Solutions.