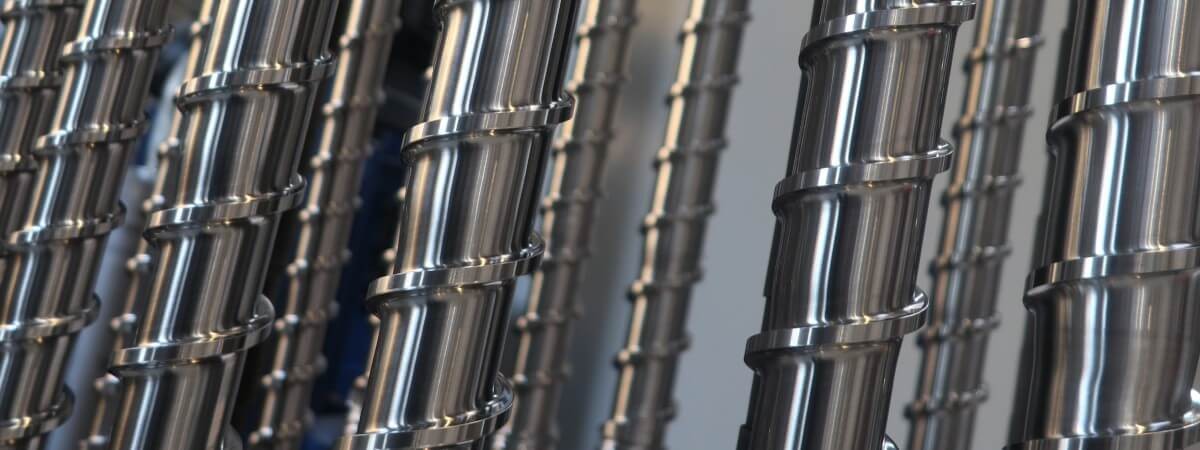
Fig. 1: Tornillo de extrusora nitrurado con plasma y preparado para el proceso de recubrimiento PVD. Fuente: Busch Vacuum Solutions.
Bomba de vacío de tornillo para recubrimientos mediante Arc PVD
La actividad principal de Dreistegen GmbH es el acabado de superficies de grandes herramientas y componentes metálicos. La empresa utiliza distintos tratamientos de capa de difusión, como la nitruración, la nitrocarburación o la oxidación, así como técnicas de recubrimiento como la deposición física del vapor (PVD) y la deposición química del vapor (CVD), bajo la aplicación de plasma en frío.
Para aplicar capas finas endurecidas mediante evaporación por arco (Arc PVD) bajo vacío, Dreistegen utiliza una bomba de vacío de tornillo COBRA NC de Busch Vacuum Solutions. Como bomba primaria, funciona con dos bombas de vacío turbomoleculares para generar el vacío en la cámara de recubrimiento.
En 2008, el doctor Oliver Kayser puso en marcha su propia empresa en los edificios de una antigua fábrica textil en la localidad de Monschau de la región alemana de Eifel. Kayser, cuyo negocio se centraba inicialmente en la nitruración por plasma y en el recubrimiento PVD para herramientas y componentes, devolvió la vida a aquel antiguo edificio industrial con más de 200 años de antigüedad. Lo que empezó modestamente en unos edificios medio derruidos, se ha transformado actualmente en una moderna empresa de tamaño medio con 40 empleados que aplican capas finas a piezas de trabajo para protegerlas contra el desgaste y la corrosión. Y lo que es más, estos recubrimientos pueden ayudar a impedir que se formen residuos sobre las superficies. De este modo se evitan las reacciones parásitas con otros materiales. Muchos de los clientes de Dreistegen provienen del ámbito del procesado de plásticos, y suelen encargar a la empresa el recubrimiento de herramientas moldeadas por inyección, extruidas o moldeadas por soplado. El doctor Oliver Kayser desarrolló una forma de recubrimiento especial que impide que la estimulación catalítica de la superficie de la herramienta degrade el plástico fundido. Como resultado, el plástico no se pega al molde. Para el operador, esto significa que puede cambiar el material y el color rápidamente en aplicaciones de extrusión o moldeo por inyección. Además, puede reducirse la cantidad de agente desmoldeante, o incluso eliminarse por completo.
Dreistegen también recubre herramientas de formado y moldes de fundición, principalmente para la industria automovilística y sus proveedores. Dreistegen ofrece una gama de recubrimientos y acabados de nitruración, PVD y CVD.
El doctor Oliver Kayser se dedica activamente al desarrollo de técnicas de recubrimiento modernas y siempre experimenta con modos de optimizar las capas finas para darles propiedades específicas que generen beneficios para sus clientes en aplicaciones concretas. Esto también incluye la optimización de la tecnología de su planta.
El sistema de recubrimiento PVD que adquirió, con un diámetro de giro utilizable de 1.200 milímetros y una altura utilizable de 1.500 milímetros, se instaló originalmente con un sistema de vacío compuesto por una bomba de vacío de paletas rotativas lubricadas con aceite como bomba primaria y dos boosters de vacío. Este sistema generaba el vacío necesario para las dos bombas de vacío turbomoleculares, que funcionaban en paralelo. Kayser sustituyó toda esta unidad de vacío primaria por una COBRA NC 400 B de Busch. La bomba de vacío de tornillo alcanza un vacío límite de 0,05 mbar (hPA) en una sola etapa. De este modo, es capaz de sustituir la antigua unidad de vacío de tres etapas de otro fabricante con el mismo vacío límite y caudal y, al mismo tiempo, ofrecer una eficiencia energética mucho mayor.
Kayser valora el rendimiento estable y fiable de la COBRA NC, así como su funcionamiento silencioso. Además, ocupa mucho menos espacio que el sistema de vacío anterior.
-
Fig. 2: Sistema de recubrimiento Arc PVD que utiliza una bomba de vacío de tornillo COBRA NC como bomba primaria para dos bombas de vacío turbomoleculares. Fuente: Busch Vacuum Solutions.
Kayser también examinó atentamente las bombas de vacío de tornillo de otro fabricante. Estas tenían un sistema de rodamientos de una cara y estaban impulsadas por un motor especial muy difícil de sustituir.
Kayser quedó impresionado por el diseño modular y funcional de la COBRA, que ofrece un sistema de rodamientos de doble cara en los dos rotores de tornillo y un motor estándar montado con bridas, que puede sustituirse en cualquier momento.
Desde la carga de la cámara de recubrimiento hasta la retirada de las piezas de trabajo, el proceso Arc PVD dura entre 14 y 18 horas. La bomba de vacío COBRA NC sigue funcionando en los breves descansos entre dos procesos para montar y retirar las piezas de trabajo. Esto significa que la COBRA NC permanece todo el año encendida. Para Kayser, la configuración actual para generar el vacío del proceso en su sistema de recubrimiento –que consiste en la combinación de una bomba de vacío de tornillo COBRA NC y dos bombas de vacío turbomoleculares montadas después de esta en paralelo– es la solución ideal.
El material básico de la pieza de trabajo debe tener un determinado nivel de endurecimiento de la superficie para poder recibir un recubrimiento PVD. Por esta razón, Dreistegen suele preparar las piezas de trabajo que va a recubrir mediante un proceso de nitruración por plasma.
A continuación, las piezas nitruradas con plasma se someten a un arenado con perlas de vidrio o se pulen ligeramente si es necesario. Una vez limpias las piezas de trabajo, se fijan en los soportes y se cargan en la cámara de recubrimiento. Después, la cámara cerrada se evacúa hasta un nivel de vacío de entre 10 y 5 mbar (hPA). Las piezas de trabajo se calientan dentro de la cámara hasta una temperatura máxima de 450 °C.
Una vez alcanzada la temperatura del proceso, los óxidos naturales se erosionan en un plasma de argón de descarga luminiscente. Las evaporadoras de arco se encienden y pueden moverse. Sin embargo, permanecen unidas a los materiales donantes de electrones del titanio, el cromo o sus aleaciones debido a los imanes permanentes de su parte posterior. También pueden utilizarse aleaciones de aluminio u otros metales.
En el arco, el material donante de electrones se vaporiza en un proceso similar a una explosión y las partículas de vapor individuales se ionizan casi por completo. La proyección de electrones (BIAS) se utiliza para disparar los iones contra las piezas de trabajo. También se añaden gases reactivos, como el nitrógeno, el acetileno, el metano, el oxígeno y el hidrógeno. La adición de estos gases hace que la presión de la cámara de recubrimiento suba hasta los 10-2 mbar (hPa). Los gases reactivos liberados del plasma se unen a los iones de metal en la superficie de la pieza de trabajo para crear las capas de recubrimiento duro. Algunos de los compuestos típicos son el nitruro de titanio (TiN), el carbonitruro de titanio (TiCN), el nitruro de cromo (CrN), el nitruro de titanio aluminio (AlTiN) y el óxido de cromo (Cr2O3). Debido a la alta energía de las partículas y a la potencia del lanzamiento, el recubrimiento que se obtiene es excepcionalmente adhesivo y uniforme, incluso en piezas de trabajo con formas complejas. Las capas finas que crea Dreistegen con la evaporación mediante arco logran un nivel de dureza de más de 2.000 HV (Vickers Hardness).
En comparación con la unidad de vacío original, la cantidad de tareas de mantenimiento requeridas en el sistema de vacío es considerablemente menor gracias al uso de la bomba de vacío de tornillo COBRA NC.
La única tarea requerida en la bomba de vacío de tornillo es un cambio anual del aceite de engranajes.
El doctor Oliver Kayser destaca que la seguridad absoluta del funcionamiento de la bomba de vacío de tornillo es muy importante para él. La pérdida de la bomba de vacío durante el proceso causaría un daño enorme, ya que las costosas piezas de trabajo quedarían inutilizables.
Tras dos años de funcionamiento ininterrumpido de la COBRA NC, el doctor Oliver Kayser comenta:
En Dreistegen somos clientes satisfechos de Busch y estamos impresionados por la calidad de las máquinas.